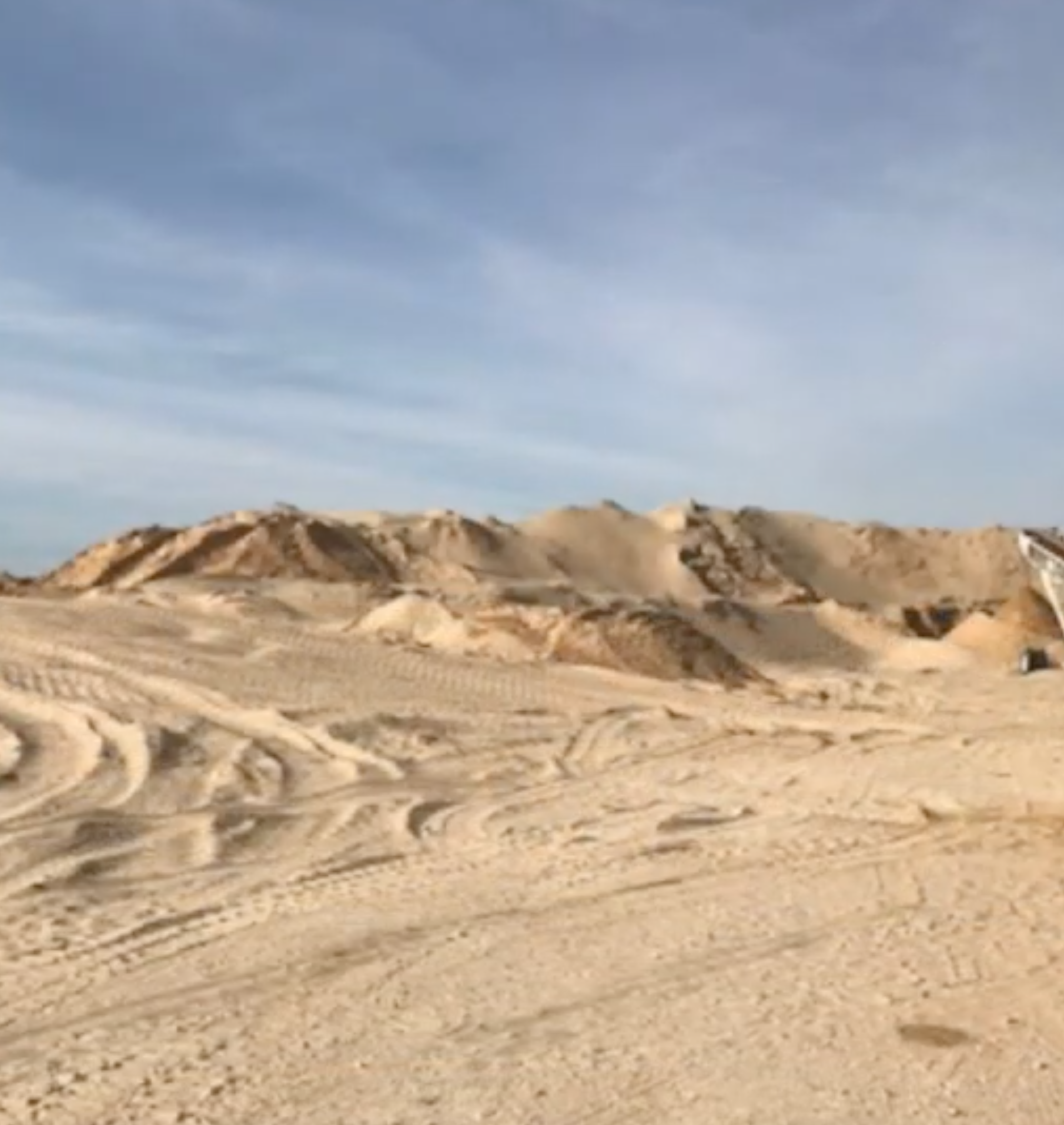
Client:
Quantity:
Size:
Application:
In 2017, Vortex completed a large project with an industrial sand manufacturer to construct a new sand processing facility. As part of this project, the client sought solutions for:
Diverting sand into screeners, where the sand is sized and then transferred into a series of holding bins.
Loading sand from each holding bin into enclosed trucks below.
Due to the abrasive properties of industrial sand, this client sought reliable components designed for durability and longevity. Having enjoyed the quality of Vortex components when using them in previous projects, this client opted to source 17 Pivoting Chute Diverters, 9 Titan Lined Diverters (TLDs), 5 Titan Slide Gates (TSGs), 5 Vortex Loading Spouts, and 14 Titan Maintenance Gates.
Sand Loadout into Enclosed Trucks
Various grades of industrial sand are being loaded into enclosed trucks below. For enclosed loading applications, the Vortex Loading Spout is designed to prevent dust emissions to atmosphere by closing off a vessel’s loading hatch at the scavenger.
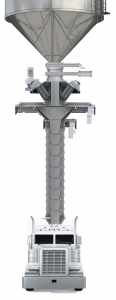
Quantity: 5 Vortex Loading Spouts
Specifications:
- Travel Distance: 6 ft | 1.8 m
- Outlet Scavenger Size: 14 in | 355 mm
- Load Rate Capacity: 250 ftᶾ/min (CFM) | 7 mᶾ/min (CMM)
- Intended for enclosed loading application.
Features:
- Stacking cones constructed from 400 Brinell Hardness Number (BHN) abrasion-resistant steel.
- Abrasive-duty outer sleeve.
- Each spout is equipped with a Vortex In-Line Filtration System, a Vortex Dual-Axis Spout Positioning System (2 ft | 0.6 m total travel), a Tilt Probe material level-sensing kit, and a Remote Control Pendant.
About: In-Line Filtration System
A Vortex In-Line Filtration System is installed directly above a Vortex Loading Spout to enhance dustless loading by means of an air withdrawal. Throughout the loading process, displaced air and dusts are simultaneously aspirated out of the enclosed vessel via the filtration system. By means of a vacuum pull, the air-dust mixture travels back upward along the spout’s outer sleeve. As dusts travel upward toward the filters, turbulence from materials flowing through the stacking cones causes some dust to be pulled between the cones and back into the material flow stream.
Any dusts that reach the In-Line Filtration System are temporarily captured in several filters. Throughout the loading process, the air-dust mixture is continuously filtered and a reverse pulse jet system purges the dusts back into the material flow stream. This creates a closed loading cycle that prevents dust emissions and minimizes material loss.
The system’s filters are designed to enhance maintainability and minimize dust build-up in the pleated cartridges. Above each filter cartridge, a hinged access cover is secured by a quick-lock handle. This allows filters to be quickly inspected, maintained or replaced without the use of tools. Also, by securing the covers with hinges and handles instead of bolts, it eliminates the risk of operators dropping hardware either external to the spout, or down into the spout and contaminating the load.
Do note: Vortex In-Line Filtration Systems can be supplied with bolted covers instead of hinged covers, if desired.
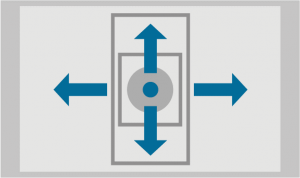
About: Dual-Axis Spout Positioning System
Using remote control, Vortex Dual-Axis Spout Positioning Systems allow operators to move a spout front-to-back and side-to-side above a truck. This improves loadout efficiency because rather than needing multiple trials to align a truck beneath a spout, the truck can make an approximated pull into the loadout station and the spout’s position can be adjusted to meet the truck’s position – in a much less time-consuming manner. Better positioning also improves material flow patterns and reduces spout wear.
About: Remote Control Pendants
Today, many facilities utilize control pendants. There are many pendant types, but among the most popular options are a chord to manually guide the spout into position. In this case, the client forwent manual chords and instead sourced Remote Control Pendants so that each spout can be guided into position using automation. For safety reasons, this technology is attractive because it allows operators to maneuver the spout remotely, keeping them off the tops of trucks and away from catwalks and other potentially dangerous equipment.
About: Material Level-Sensing Devices
For this enclosed loading application, a Tilt Probe material level-sensing device is used to prevent truck overfilling. The probe is mounted at the bottom of the spout’s outlet scavenger, so that it hangs down into the truck. As materials fill the truck, the probe slowly begins to tilt atop the material pile. Once the probe is tilted at an approximate 16° angle, the probe is synchronized with an Auto-Raise System that signals the conveying line to halt material flow. Then, the spout is retracted back out of the loading hatch.
In essence, a material level-sensing device complements the load cells to ensure a truck is not overweight at the loading scale. By preventing the truck from overfilling, it also prevents materials from backing up in the spout itself. Otherwise, once the spout is retracted, surplus materials will spill onto the floor of the loadout station, resulting in product loss.
By introducing automation into the loading process, it reduces risk for error and creates consistency in loading operations.
Continue reading about this project:
Part 1 | Part 2 | Part 4 | Part 5