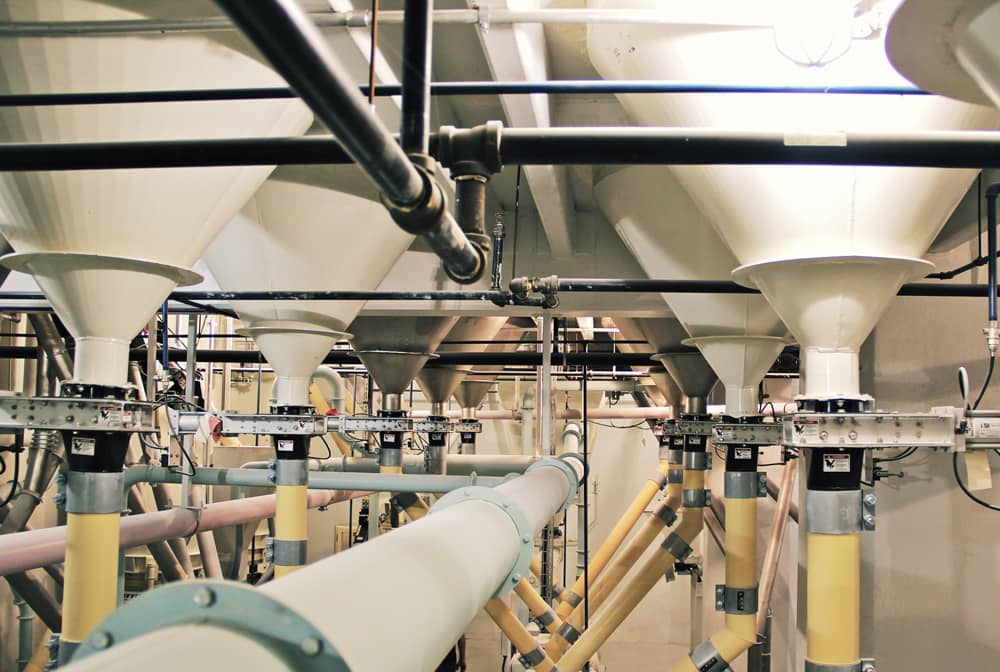
Client:
Quantity:
Size:
Application:
hopper [hop-er] – a funnel-shaped chamber or bin in which loose material, as grain or coal, is stored temporarily, being filled through the top and dispensed through the bottom. (source: dictionary.com)
Unlike a silo, which is used to store large volumes typically for extended periods of time, a hopper is used for a specific process in the system such as batch mixing or weight scaling. Other synonymous names for a hopper in the bulk solids handling industry are bin, receiver, or even sometimes, vessel.
Hoppers can be separated into three different categories based on what they are used for.
Scale Hopper with Slide Gate
A scale hopper is used to meter ingredients in a gravity or pneumatic application. This scale is used to fill bulk bags with a consistent weight and usually does not need to be pinpoint accurate. The scale hopper sits on load cells to get the correct weight. Once the pre-selected batch weight is met, the load cells triggers a signal to dump the material from the hopper to the fill equipment ( i.e. mixer, bulk bag, or tote) below. A slide gate below the hopper is the easiest solution to start or stop the flow of material during processing or maintenance. A majority of the time, the slide gate stays in a full-open or a full-close position since you do not need to close on the material.
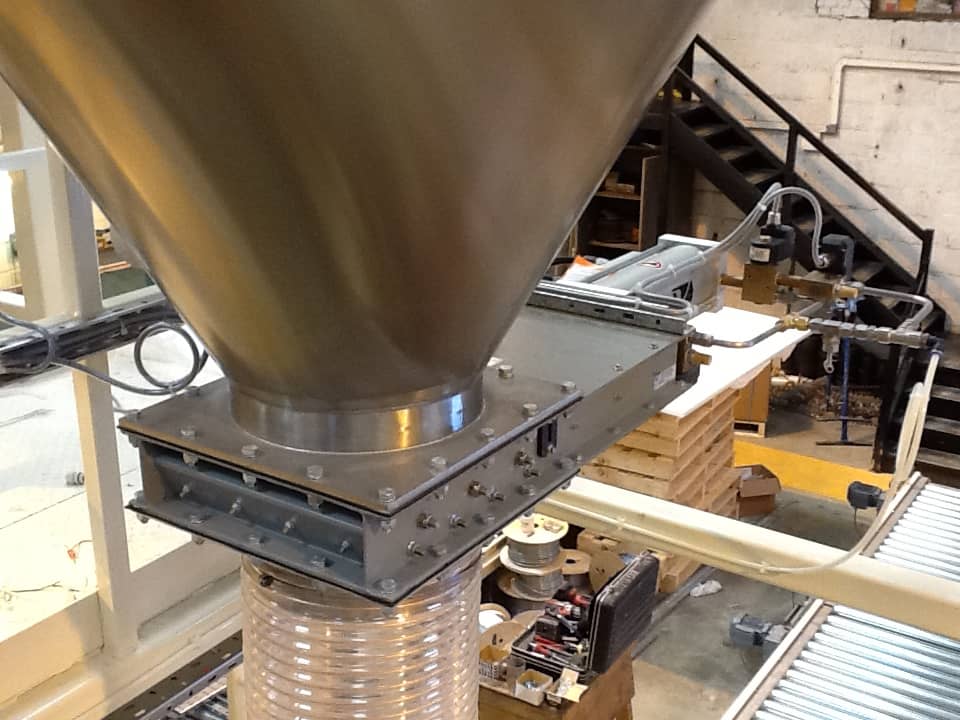
Surge Hopper with Slide Gate
A surge hopper is used to feed into a scale hopper, feeder, or a screw conveyor in a gravity or pneumatic system. The slide gate can have metering controls such as a variable position control to dribble material, or be used in a full-open or a full-close position. The purpose of a slide gate below a surge hopper is to shut off material flow so it will not leak to the atmosphere or pressurize the equipment below in most cases. The best type of slide gates to install below surge hoppers are Roller Gates for sticky materials, or Orifice Gates if you need to seal differential pressures.
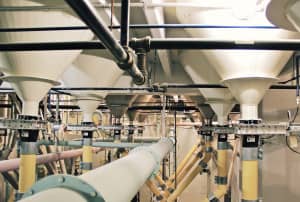
Day Bin with a Slide Gate
A day bin is also used as a temporary storage for materials in a gravity or pneumatic system. This type of hopper is normally used to feed material into a processing piece of equipment such as an extruder, mixer, or blender. The slide gate is used to shut off the flow or meter the material into the process line.
Questions to ask when installing a slide gate below a hopper:
Which slide gate should you use under a hopper? There are many things to consider. To answer this, you need to know:
- What size and shape is the hopper’s outlet? You can match the opening to the slide gate, or use a transition.
- What material is being conveyed? A bulky, aggregate like coal or a heavy material such as zinc oxide would need a more robust slide gate such as a TSG so the seals don’t wear out as fast. A Special Service Inlet can also be attached to extend the service of your slide gate.
- What is the flow rate or bulk density? If the material is lightweight, you can save some money by choosing a more simple actuation method such as a hand slide gate.
- How often will you be shutting off the material flow from the hopper? If you are only shutting it down during cleanings, a simple maintenance gate with a hand crank would be more economical. But a system that will need to be shut down quite often would save the company time and increase efficiency if a pneumatic actuation is attached to the slide gate.
- What flow aids are used in the hopper to move the material? The material in the hopper can be moved out of the hopper by gravitational pull, vibrators for material that doesn’t flow well such as talc, or aeration pads for material that tends to pack such as cement or limestone powder.
- You also need to look at where the material is going next in the system. If the material is being flowed into an airlock, then a Clear Action Gate would be the best slide gate. If the next location is to a drag conveyor or bucket conveyor, the material is dumped from the hopper funnel periodically into the space between the drags. In this case, you wouldn’t need a slide gate.
- If you need more assistance in choosing the correct slide gate to install under your hopper, ask your slide gate manufacturer for the best solution for your system.