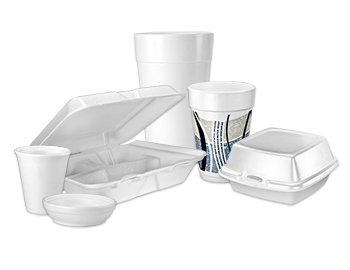
Since 2007, Vortex has been providing a U.S. plastics company with solutions for transporting plastic materials throughout their production facility. Because this plastics plant operates 5 shifts, 24 hours per day – and all but two days each year – the client places a particular emphasis on sourcing components designed for reliability and longevity. Having enjoyed the quality of Vortex components, this plastics company currently has 7 Roller Gates, 31 Wye Line Diverters, and 32 Quantum Orifice Gates in their facility.
The Process
In this client’s process, Vortex components have been sourced to assist in several areas, including:
- Handling plastic regrind, so that scrap materials can be reintroduced into the extrusion process.
- Handling resins and raw plastic compounds, prior to the plastics extrusion process.
- Converging plastic materials from several sources to transport toward a single destination.
The client’s end product is polystyrene tableware – more commonly known as, “foam cups, plates and bowls.”
Regrind, Recycling & Reuse
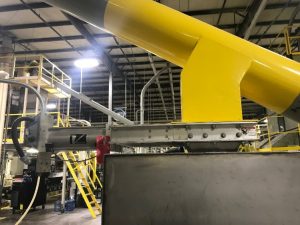
This plastics company uses Vortex Roller Gates to process plastic plate regrind. Once sprue, runners, flash, and other off-spec polystyrene materials are produced as a result of the plastics extrusion process, they are chopped, ground, reintroduced and reprocessed alongside new plastic resins, so that quality finished products can still be forged from recycled materials.
By reusing scrap materials in production, this plastics company has reduced its manufacturing waste to be less than 1%.
- 6 Vortex Roller Gates:
- Gate Size: 10 in. (254 mm)
- 1 Vortex Roller Gate:
- Gate Size: 16 in. (406 mm)
- Gate Specifications:
- Gate body constructed from aluminum.
- Blade constructed from 304 stainless steel.
- Material contact areas constructed from 304 stainless steel.
- Each gate is equipped with a Special Service Inlet.
*To compensate for each gate’s long stroke, each was equipped with an oversized pneumatic actuator. Each pneumatic actuator was built with a magnetic piston, to accommodate magnetic reed switches for blade position indication.
The Vortex Roller Gate features live-loaded, wear-compensating bonnet seals, which are constructed from hard polymer and compressed rubber. As the gate experiences many actuations over time, the blade will begin to wear against the polymer seals. The compressed rubber backing allows the seals to self-compensate for wear, so that the gate’s dust-tight seal is maintained for an extended period of time.
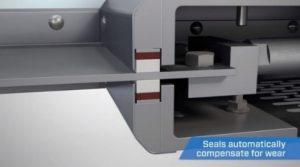
Roller Gates also feature CAM-adjustable rollers, which are constructed from hard polymer. If the gate begins to lose its seal, the rollers may be adjusted upward so that the blade is once again compressed against the seals. This maintenance procedure can be quickly and easily performed while the gate remains in place, and is performed using only simple tools.
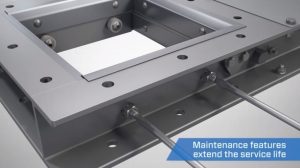
If material begins to escape into the gate’s bonnet, the Roller Gate features removable panels along the side frame that allow access to replaceable bonnet seals. Using only simple tools, the panels can be removed from each side of the gate body. Then, a new bonnet seal can be driven into the seal port as the old seals are simultaneously ejected out the other side of the valve. This allows for quick and easy seal replacement without removing the gate from place.
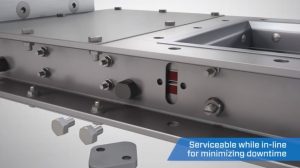
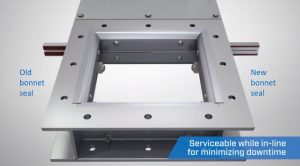
Special Service Inlets were added to these Roller Gates to direct material flow through the center of each gate’s inlet. In doing so, a Special Service Inlet protects a gate’s rollers by shielding them from the material flow. Special Service Inlets also create a dead pocket that allows material to fall away from the leading edge of the blade as it closes. This feature hinders material from packing into the gate’s end seal, which would otherwise cause material leakage through the valve and other blade actuation errors.
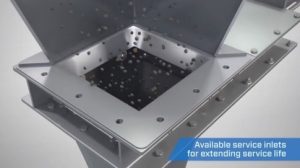
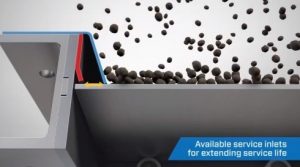
Extrusion
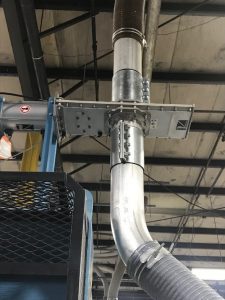
In this client’s facility, Vortex Quantum Orifice Gates assist in the conveyance of resins, compounds, and other plastic materials throughout the stages of production.
Polystyrene is a thermoplastic, meaning raw plastic materials will soften in the presence of heat. Thus, heat is introduced begin the extrusion process. Once softened, the polystyrene is molded into its desired shape. As it exits the extrusion line, the molded polystyrene returns to ambient temperature and hardens in its desired shape as a cup, plate or bowl.
- 32 Vortex Quantum Orifice Gates
- Gate Size: 6 in. (152 mm)
- Gate Specifications:
- Gate body constructed from aluminum.
- Blade constructed from 304 stainless steel.
- Material contact areas constructed from 304 stainless steel.
- Each gate is equipped with a Special Service Inlet.
*To compensate for each gate’s long stroke, each was equipped with an oversized pneumatic actuator. Each pneumatic actuator was built with a magnetic piston, to accommodate magnetic reed switches for blade position indication.
Vortex Quantum Orifice Gates are designed for use in gravity flow, pressure or vacuum applications up to 15 psig (1 barg). In this client’s process, plastic materials are being pneumatically conveyed by pressure in dilute phase.
In 1980, Vortex founder Neil Peterson determined that traditional bullnose slide gates and butterfly valves are well-designed to handle gases and liquids, but not dry materials. They rely on soft rubber seals which erode or tear away during use, allowing leakage of air and material through the valve or into atmosphere. Wearing seals cause frequent need for valve maintenance, production inefficiencies, and unclean plant environments.
With these deficiencies in mind, the Vortex Orifice Gate was patented as the first slide gate specifically designed for handling dry bulk materials. It incorporates hard polymer seal plates that compensate for wear over time, which is achieved by “live-loading” the seal plates against the blade. As the valve cycles, any frictional wear between the blade and seals is compensated by compressed rubber backing on the seal plates. These seals are also protected from blast abrasion, permitting long service life and durability without frequent maintenance.
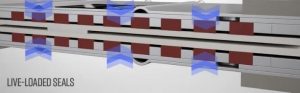
The Orifice Gate’s blade and seal designs allow the valve to “self-clean” on the opening stroke, which prevents material packing in the valve’s internal seals. This feature is critical to inhibit material leakage across the valve or into atmosphere.
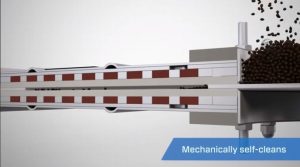
To ensure the valve’s dust-tight seal can be maintained over time, the Orifice Gate features a patented shimming system along the lateral aspect of the gate. This feature allows maintenance engineers to increase the compression load between the seal plates and blade by removing shim along each side of the valve – doing so while the equipment remains in-line. Unlike most valves, preventative maintenance of the Orifice Gate requires the removal of parts, rather than replacing them.
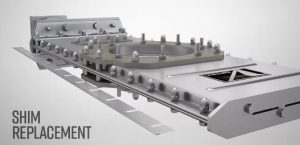
At the front of the valve, the Quantum Orifice Gate features three small weep holes (pictured). After many actuations over time, the pressure plates may begin to lose their seal and allow material dusts to enter the valve body. At that time, trace amounts of material dust are allowed to exit the valve through the weep holes. The purpose of this feature is to indicate to maintenance technicians when maintenance must be performed to restore the diverter’s dust-tight seal.
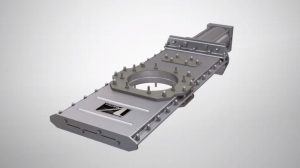
Collectively, these features improve process efficiency through a dust-tight seal that prevents air and material leakage to atmosphere.
Transporting Materials throughout the Facility
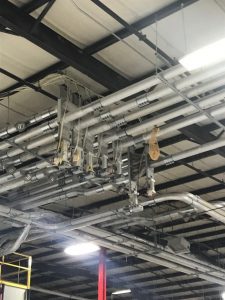
This plastics company has configured Vortex Two-Way & Four-Way Wye Line Diverters to create “banks” for automated transport of plastic materials throughout their facility. Pneumatic “banks” allow various convey lines to meet and either divert materials toward several destinations, or converge materials for transport toward a common destination.
To accommodate the client’s pre-existing footprint, most of the diverters were constructed to match up with OD tube sizes, but several were constructed using Schedule 10 pipe sizing.
- 5 Vortex Wye Line Diverters
- Valve Size (Outside Diameter): 4 in. (102 mm)
- Inlet & outlet weldments constructed from 304 stainless steel.
- 11 Vortex Wye Line Diverters
- Valve Size (Outside Diameter): 6 in. (152 mm)
- Constructed using Schedule 10 pipe sizes.
- Inlet & outlet weldments constructed from aluminum.
- Diverter Specifications:
- Two-way design.
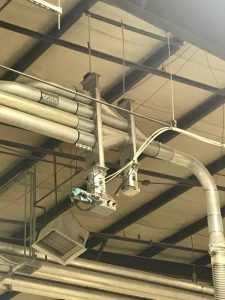
- Valve body constructed from aluminum.
- Blade constructed from 304 stainless steel.
- Material contact areas constructed from 304 stainless steel.
- Straight leg diverting design.
- PET pressure plates.
- 15 Vortex Wye Line Diverters
- Valve Size (Outside Diameter): 4 in. (102 mm)
- Diverter Specifications:
- Four-way design.
- Valve body constructed from aluminum.
- Blade constructed from 304 stainless steel.
- Inlet & outlet weldments constructed from 304 stainless steel.
- Material contact areas constructed from 304 stainless steel.
- Straight leg diverting design.
- PET pressure plates.
*To compensate for each gate’s long stroke, each was equipped with an oversized pneumatic actuator. Each pneumatic actuator was built with a magnetic piston, to accommodate magnetic reed switches for blade position indication.
Vortex Wye Line Diverters were sourced to pneumatically convey plastic materials throughout the manufacturing facility. Wye Line Diverters are designed for use in pressure or vacuum applications up to 15 psig (1 barg). In this client’s process, plastic materials are being pneumatically conveyed by pressure in dilute phase.
Wye Line Diverters can either be used to divert materials from a single source toward multiple destinations, or converge vice versa. In this client’s process, plastic materials are being converged from multiple sources toward a common destination, in order to feed the extrusion line.
Unlike ordinary flapper-style diverters, the Wye Line Diverter features a sliding blade with a machined hole to match the inside diameter of the convey line, so that unobstructed airflow can carry materials downstream. For conveying ports that are closed, the sliding blade’s solid section halts material flow, resulting in a positive shutoff. This allows the Wye Line Diverter to be shifted “on the fly.”
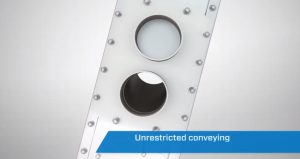
As is the case in the Quantum Orifice Gate design, the Vortex Wye Line Diverter features live-loaded, wear compensating pressure plates to sandwich the sliding blade. As the valve cycles, any frictional wear between the blade and seals is self-compensated by compressed rubber backing on the seal plates. This ensures the valve’s dust-tight seal can be maintained over time with very little maintenance intervention. Unlike ordinary flapper-style diverters – which rely on elastic seals that are exposed to the material flow stream – the Wye Line Diverter’s pressure plate seals are protected from blast abrasion, affording them durability and longevity in their application.
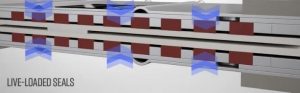
The Vortex Wye Line Diverter also features a patented shimming system along the lateral aspect of the gate. This feature allows maintenance engineers to increase the compression load between the seal plates and blade by removing shim along each side of the valve – doing so while the equipment remains in-line. Unlike most valves, preventative maintenance of the Wye Line Diverter requires the removal of parts, rather than replacing them.
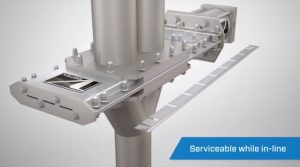
As airflow carries materials downstream, a naturally occurring high-pressure airfoil is created in the closed conveying ports, which deflects materials that have entered closed-line segments back into the material flow stream.
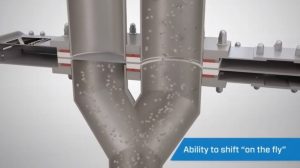
At the front of the valve, the Wye Line Diverter features three small weep holes (pictured). After many actuations over time, the pressure plates may begin to lose their seal and allow material dusts to enter the valve body. At that time, trace amounts of material dust are allowed to exit the valve through the weep holes. The purpose of this feature is to indicate to maintenance technicians when maintenance must be performed to restore the diverter’s dust-tight seal.
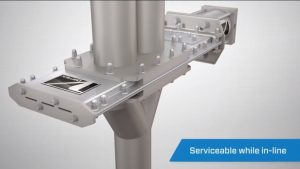
Collectively, these features create a dust-tight seal that prevents material leakage to atmosphere and hinders materials from migrating to the diverter’s opposite port(s).
For a full demonstration on the functionality of Vortex products, visit www.vortexglobal.com/animations.