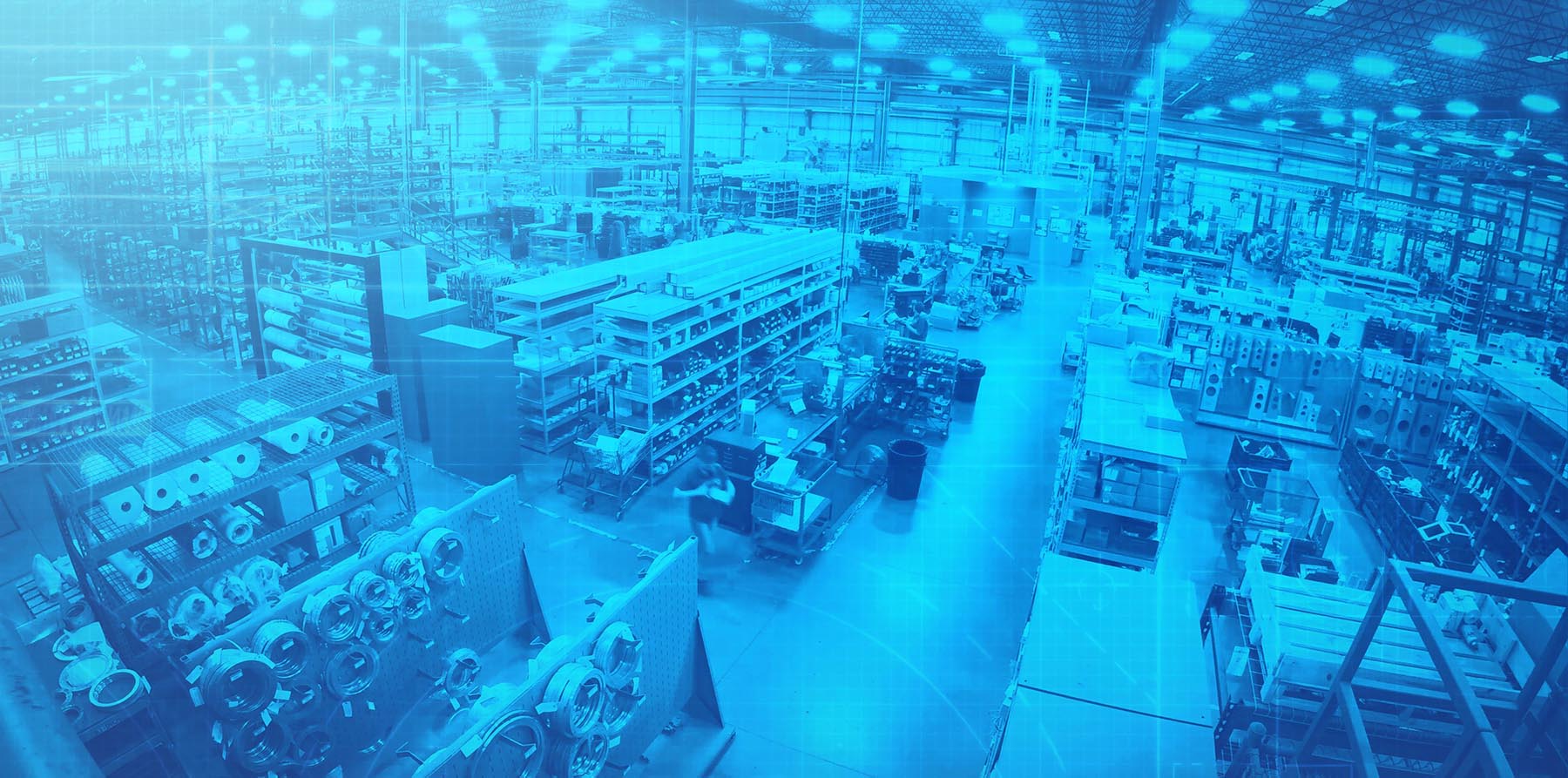
Client:
Quantity:
Size:
Application:
Some factories temporarily shut down each year for scheduled plant maintenance shut-down. Within that period of time, the plant floor is cleaned, equipment is inspected or replaced, processes are improved, and/or production lines are added. The “off-line” time can be detrimental, or advantageous, to your bottom line depending if a plan is properly prepared and executed through these 5 phases.
Phase I: Define and Implement Strategies for Plant Maintenance Shut-Down
- Provides a foundation for the goals of your plant maintenance shut-down.
- Analyzes how frequently plant maintenance must be performed to allow the production process to function optimally.
- Estimates how long plant maintenance shut-down must occur, and assesses the best time for plant maintenance shut-down to occur, in relation to manufacturing forecasts. Plant maintenance shut-down is a long-term business strategy – not a “week of” decision.
- Key drivers of plant maintenance shut-down:
- Improve equipment to reduce waste in manufacturing resources, thus reducing operating costs.
- Improve overall equipment effectiveness (OEE).
- Maintenance equipment to sustain its equipment life cycle.
- Maintenance equipment to improve mean time between failure (MTBF).
- Equipment inspection.
- Equipment repair.
- Replacement of worn equipment.
- Replacement of broken equipment.
- Replace depreciated equipment (ie: Equipment that has reached the end of its useful life).
- Ensure compliance with health & safety codes.
- Be mindful of and create a budgetary buffer for the fact that unexpected issues will be found internal to the system, once maintenance inspections have begun.
- Appoint a steering committee to lead the plant maintenance shut-down. That committee should host meetings with executive management to assess how the maintenance shut-down will impact the greater good of the company, and to assess what Key Performance Indicators (KPIs) are most important to the company’s long-term business goals. Typical KPIs include safety, cost, production scheduling, labor hours, overtime hours, lead times, and more. By assessing KPIs, a business can prioritize its investments in system components, based on level of importance to the business’ common, overarching goals. (Example: If the goal is to increase capabilities at bulk bag loading stations, a wise investment would be in a flap diverter to double the loading capacity capabilities. A less appropriate investment would be in a new silo of equal size above the loading station, if that silo was still capable of efficiently holding materials.)
- Make a list of all equipment parts that should be up for debate. Categorize those list items based on what items are required for maintenance to remain compliant with agency guidelines, and which improvements are “a la carte” to benefit the system’s goals, ranking in level of importance. Use data analysis to determine what equipment areas are “bottlenecks” and more degrading to efficiency, in comparison to the rest of the system. Upon analysis of improvement priorities, finalize what improvements will be made during the curing system shut-down by adding them to the CMMS (Computerized Maintenance Management System). Those improvements that were opted against for this shut-down should be noted, so that they can be re-considered for the next system shut-down.
- Be sure the improvements being made during plant maintenance shut-down can only be done during full shut-down. If a task can be performed while the system remains active, the company is not best utilizing their shut-down resources.
- Document the estimated costs, down-time schedule, list of jobs, and estimated resources needed to complete the shut-down project. This allows the company to anticipate the full scope of the project. Have this agreement approved by the shut-down steering team and the company executive team before the project is to begin. Once approved, disseminate the information throughout the organization, so that there is project transparency across company sectors.
Phase II: Plant Maintenance Shut-Down Preparation
- Develop plans for how the maintenance will be performed, prior to project execution. To reinforce the improvements being made, consider adjusting the company’s environmental, health and safety plans. Analyze the different manufacturing departments to determine if they can be optimized or otherwise improved in any way. Determine the logistics on what materials are needed for the shut-down project, when they will arrive on-site, how they will arrive on-site, and who will be working on this equipment during the shut-down. Make sure equipment and materials are ordered early, so that the shut-down is not delayed. Consider how the equipment and materials will be stored until they are called upon during shut-down.
- Develop plans for quality assurance. This provides standard procedures for quality control techs, so that they can inspect new equipment after system shut-down has concluded, to be sure the equipment is running safely and efficiently.
- Using information from Phase I, develop the work package. A work package details the job scope, the number of laborers assigned to the shut-down project, the estimated number of labor hours needed for project execution, and scheduling of task completion. This includes a detailed, step-by-step instruction plan on how the project will be complete. Include safety steps and precautions to be taken, drawings of the project at-hand, and photos to support how each sub-project will be completed most effectively.
- Determine what steps of the shut-down will be completed using internal resources, and which project stages will external resources be necessary. For those jobs demanding external resources, begin fielding bids from contractors for such jobs. (Example: Contracting a crane company to remove valves from line.)
- Create contingency plans, to account for any risks or problems that may occur during plant maintenance shut-down.
- Determine any necessity work that must be done pre-shut-down. Complete those jobs, so that they are ready to accommodate the shut-down improvements, when called upon. (Example: If adding a production line, prepare new piping to run toward the inlet and outlet of new equipment.)
- If Phase II is done correctly, a full, detailed schedule of the plant maintenance shut-down will be complete, and cost figures will be estimated within approximately 10 percent of budget allocations.
- Have plans approved by both the shut-down steering committee and the company executive team. Once approved, communicate Phase II to each of the company’s departmental sectors, to create project transparency.
- It is also important to consider the effects the shut-down may have on your customers and constituents. If the shut-down will have a direct impact on the customer, frequent and effective communication is crucial. Update your customers regularly throughout the process to reduce the risk of dissatisfaction and future loss of business.
Phase III: Execution of the Project
- As previously discussed, once the project begins, it is the inevitable that undetected and unpredictable findings will arise during inspection. On the fly, it is important to assess these issues to determine the necessity of their repair, the costliness of their repair, and how they will affect the overall scope of completion for the original project. Be sure to stay true to the work package, to avoid working over-budget, and to be sure the important projects are brought to fruition during the allotted project time schedule.
- Be sure the internal and external resources on the project are well-managed, so that the project is being executed efficiently.
- Update the work package schedule daily, so that resources who finish their tasks early can be re-delegated to assist on tasks that are understaffed, not begun, incomplete, or otherwise behind schedule. Prioritize which projects are more pertinent to the project’s overall success, as well as which projects are more or less time-consuming. This creates a planned sequence for job tasks. Continuously update the package, so that communication across the project team is transparent for what projects have or have not been completed, and which projects are currently in progress.
- Track data to compare with the pre-determined KPIs – ie: actual vs. estimated labor hours, actual vs. estimated overtime hours, actual costs vs. budgeted costs, etc. This data is critical to project progression, in order to maximize costs and labor utilization. For example, if the project is developing too slowly and the staff is at maximum utilization plus ample overtime, it may be necessary to contract more resources to assist on the project. Oppositely, as the project comes to an end, often times, only a few tasks remain. In many instances, the crew becomes overstaffed for completing these minor tasks. KPI analysis allows the project supervisor to determine when resources are not being fully utilized, so that they can make the decision to cut resources for project cost efficiency.
- Once improvements and repairs have been complete, the system must be tested to be sure all improvements are running as predicted.
Phase IV: Start Up & Turn Over
Part I: Handoff
- Once testing has been complete by the shut-down team, the operations team is introduced to the new system. Then, the operations team runs testing on the full asset base to be sure the process was actually improved. The shut-down team stands by as tests are performed, to provide technical support, if necessary.
Part II: Ramp Up
- Once testing has been complete by the operations team, trials runs are performed by the system, so that the equipment can be observed in-operations and adjustments can be made accordingly. This stage is arguably the most important aspect of plant maintenance shut-down, as it is the time when errors are most likely to occur, and it is the most important aspect of the project because it determines how the system as a whole will operate and stabilize, moving forward.
Part III: the Punch List
- Once the shut-down team and the operations team are satisfied with the results of the shut-down, the shut-down team does a final walk-through to assess what tasks on the project list were completed, and which ones were not. Because of budgetary issues and un-predictable issues, it’s nearly impossible to finish all items on the punch list. However, by determine what items were not complete during this shut-down, it creates a starting point when planning the next system shut-down.
Phase IV: Evaluation
- Demobilize the work site: Plan the logistics for returning any external resources or equipment. Determine how unused resources will be disposed. Clean the work site to prepare it for operations. Get rid of the equipment removed from the system. Tear down any trailers/offices constructed for the purpose of the maintenance shut-down (ie: Those assembled to house external work teams).
- Host a post-mortem meeting to summarize the success/failures of the shut-down project. Detail the work that was complete, what remains to be complete, and lessons learned on the project. Assess the KPIs and determine the efficiency of the project’s completion, to learn from the data to better shut-down practices for next time. The premise is that if best practices can be determined, fewer problems and unforeseen complications will arise during upcoming projects, making the project streamlined of error or ambiguity.
- Finally, tie up the loose ends of the project. For bookkeeping purposes, close purchase orders, work orders, external resource contracts, or any other financial paperwork that must be processed for project completion. Keep records of how much material was used versus quantities returned upon project completion, so that more accurate material quantities can be ordered when they are needed for the next shut-down project.
- Make a cost analysis document to directly compare estimated/budgeted costs versus actual costs. Based upon this analysis, draw conclusions on how the numbers can be more accurately aligned on future projects.
- Over time, until the next shut-down is to occur, continuously monitor the equipment that was improved during the previous shut-down. This helps to justify the effectiveness of decision making in previous shut-down(s), and gives insight on major equipment categories that are most impactful for improving the asset base.
Because career changes occur, it is unlikely that the same shut-down team will work on multiple projects – especially consecutively. This is why thorough and formal documentation is necessary throughout each phase of shut-down, as it serves as an “instruction manual” for the team(s) to follow. The key factors to successful plant maintenance shut-down are simple: Outstanding management, repeatability, and consistency. If the best practices are streamlined, understandable and attainable for any team, regardless of ever-changing resources, shut-down projects themselves will also be well-oiled machines.