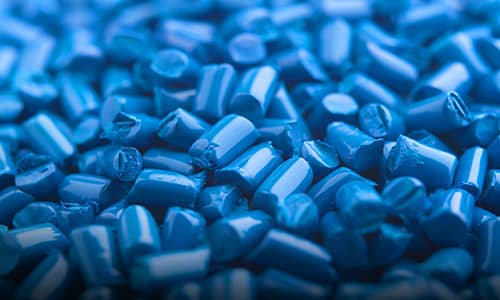
Client:
Quantity:
2 Two-Way Vortex Wye Line Diverters and 2 Four-Way Vortex Wye Line Diverters
Size:
Application:
Features:
- Diverter body & inlet/outlet weldments constructed from aluminum.
- Blade & material contact areas constructed from 304 stainless steel.
- Double-acting air cylinder actuator is equipped with a magnetic piston, to be used with magnetic reed switches for gate position indication.
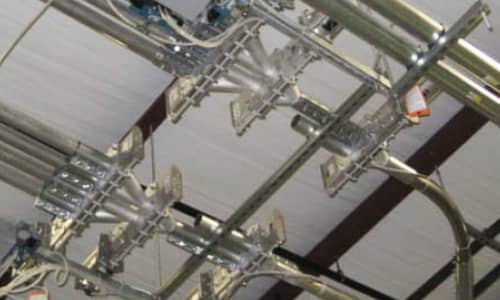
Results:
For this plastics manufacturer, the process of conveying plastic pellets was a production and safety nightmare. The hoses took up space on the production floor, employees moving through the facility had to be cognizant of the ever-changing location of the hoses, and production slowed as hoses were relocated to different source bins. On occasion, hoses were connected to the wrong source bin, causing the extruded parts to be made with improper materials – therefore deeming them off-spec and rejected.
The company had utilized Vortex Wye Line Diverters in other parts of their facility with great success. They were pleased with the valves’ performance and the lifecycle costs they provided. A decision was made to replace the hoses with additional Vortex Wye Line Diverters.
To free up space on the production floor and eliminate a potential safety hazard, the diverter valves were kept off the floor and instead installed in the ceiling. Because it is an automated system, operators are now able to remotely select a source bin for the different pellets. With each automated command, the Wye Line Diverter's sliding blade shifts into place and conveying automatically begins.
All safety, production and quality control issues were solved with this new installation. After install, the client had the foresight to expose one of the outlet ports in a two-way diverter valve – allowing an air intake so the system can be “purged,” on occasion.
“When the diverter valves arrived, we were surprised to see the new, lower profile design. The in-line serviceability and improved sealing features were an added bonus to a valve that has already provided us with quality performance.” – Production Superintendent