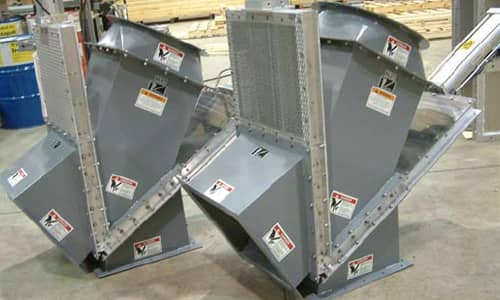
Client:
Quantity:
Size:
Application:
Features:
- Oversized, double-acting air cylinder actuator. Air cylinder is equipped with a magnetic piston, to be used with magnetic reed switches for gate position indication.
- Body constructed from 6061-T6 aluminum.
- Blades constructed from 304 stainless steel and is electropolished to handle sticky materials.
- Material contact areas constructed from 304 stainless steel & carbon steel.
- Inlet/outlet flanges constructed from carbon steel.
- Outlet legs offset 60° from horizontal.
- Because zinc oxide is a fine powder, a return pan was included on each gate. On the top side of each gate, a solid bonnet cover is used. On the outlet side of each gate, the return pan is a fabricated metal transition. It is angled to create an inverted “ramp” – beginning narrow at the back of the gate and gradually steepening as it approaches the gate’s opening. As materials migrate into the bonnet area, rather than building up and causing potential actuation issues, they are deposited down onto the return pan and reintroduced into the material flow stream. A return pan is an inexpensive way to prevent product loss and dusting into the atmosphere.
Results:
This simple suggestion from the equipment company made a huge difference in capacity and efficiency for this new plant expansion.
The Vortex Gravity Vee Diverter's dust-tight sealing capabilities and maintenance friendly features were also valuable to the client. On the sides of each gate, milled access slots allow for bonnet seal replacement while the valve remains in-line. As new bonnet seals are driven into the slot, the worn bonnet seals are simultaneously ejected out the other side of the gate. At the wear-compensating side seals, if the compression load is lessened and materials begin to migrate passed the gate, externally adjustable cam rollers can be tightened to "lift" the blade against the side seals and restore the compression load while the gate remains in-line.