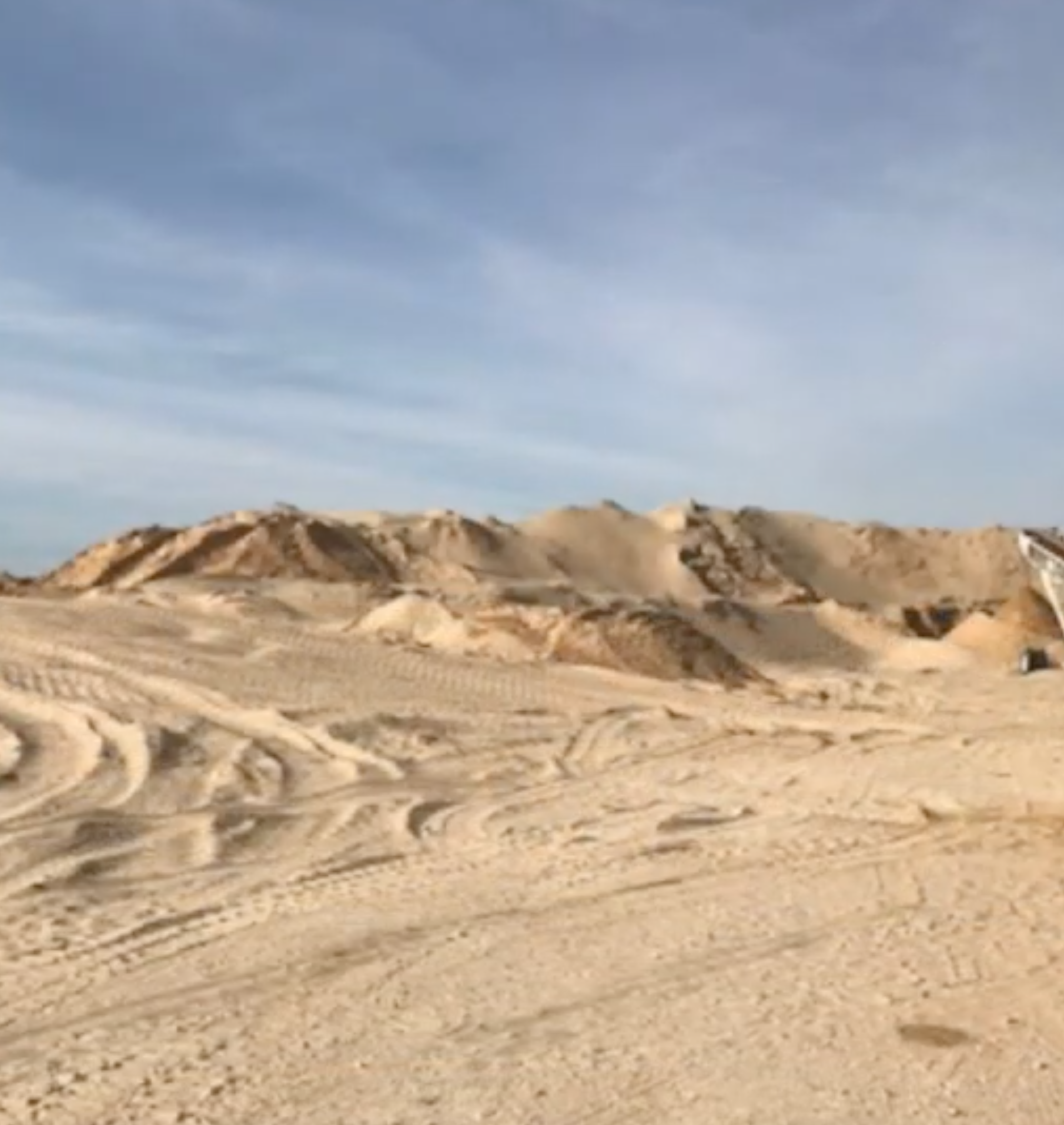
Client:
Quantity:
Size:
Application:
In 2017, Vortex completed a large project with an industrial sand manufacturer to construct a new sand processing facility. As part of this project, the client sought solutions for:
- Diverting sand into screeners, where the sand is sized and then transferred into a series of holding bins.
- Loading sand from each holding bin into enclosed trucks below.
Due to the abrasive properties of industrial sand, this client sought reliable components designed for durability and longevity. Having enjoyed the quality of Vortex components when using them in previous projects, this client opted to source 17 Pivoting Chute Diverters, 9 Titan Lined Diverters (TLDs), 5 Titan Slide Gates (TSGs), 5 Vortex Loading Spouts, and 14 Titan Maintenance Gates.
Diverting from the Initial Duct Line toward Various Production Processes
Once raw industrial sand is introduced into the manufacturing process, it is conveyed through an initial duct line. From that duct line, Vortex Titan Lined Diverters are being used to divert sand materials toward various production processes. This client sourced TLDs for their abrasion-resistance, longevity, and their ability to be maintained in-line.
9 Vortex Titan Lined Diverters (TLDs)
- Size (qty. 5): 10 in | 254 mm
- 3 diverters with a straight leg design; 2 diverters with a traditional design.
- Size (qty. 4): 16 in | 406 mm
- 1 diverter with a straight leg design; 3 diverters with a traditional design.
Diverter Specifications:
- Body, blade & material contact areas constructed from 400 BHN abrasion-resistant steel.
- Replaceable 400 BHN abrasion-resistant steel liners throughout the diverter’s internal body.
- Round transition pieces at the diverter’s inlet and outlet legs. Constructed from 400 BHN abrasion-resistant steel. Configured for ANSI bolt-through pattern.
- Blade seal constructed from polyurethane. Shaft seal constructed from PET. Shaft seal is live-loaded using silicone rubber.
- Outlet legs offset 45° from center.
- Continuous service for maximum product temperature 180° F (82° C).
- Air cylinder equipped with a magnetic piston to accommodate magnetic reed switches for blade position indication.
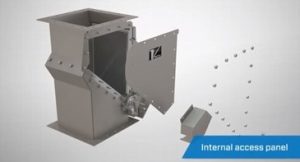
Like the Pivoting Chute Diverter, the TLD also features a removable access door that allows inspection and maintenance to be performed without removing the diverter from service. TLDs also feature replaceable abrasion-resistant liners and removable wetted parts.
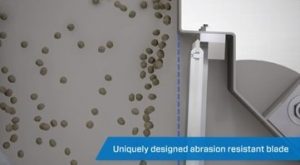
For return-on-investment purposes, these features are beneficial because they allow for the replacement of worn parts, rather than full diverter replacement.
The TLD is also designed so that the leading edge of the blade enters a recessed area. This feature ensures that the leading edge of the blade is protected from the material flow stream, to prevent material leakage to the opposite leg.
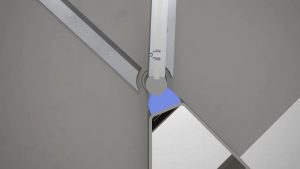
Below the blade shaft, the TLD features a shaft seal which self-compensates for wear. As the blade actuates back and forth, any frictional wear between the blade shaft and the shaft seal is compensated by compressed rubber backing. This design ensures the blade shaft and the shaft seal are continuously forced together, protecting the blade shaft from abrasion and preventing materials from migrating to the opposite leg.
Continue reading about this project:
Part 2 | Part 3 | Part 4 | Part 5