
Client:
Quantity:
Size:
Application:
As featured in Dry Cargo International
by Kevin R. Peterson and Austin Anderson
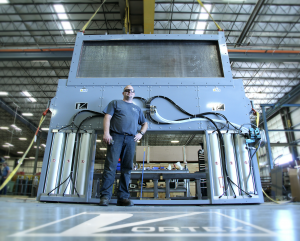
For more than 40 years, Vortex Global has provided quality slide gates, diverters, iris valves and loading spouts designed specifically for handling dry bulk solids in gravity, vacuum, dilute, or dense phase applications. Vortex valves and spouts are engineered for dependability, durability, ease of maintenance, and offer proven solutions to material handling and process efficiency problems. With an in-house team of engineers, Vortex products can be completely customised for individual applications or special installations.
Vortex manufactures many different products that address dry material handling in the coal industry. The Vortex Titan line of gates and diverters is specifically designed for applications that require larger sizes or are placed in abrasive-duty situations.
Slide Gates
One such application involved a slide gate with a 0.86 metre x 2.6 metre opening handling 50mm ‘minus’ bituminous coal. The gate was to be pneumatically actuated. One of the major requirements was that the gate had the ability to close through a standing column of product if an upset condition occurred.
Since Vortex manufactures pneumatic air cylinders, calculating the thrust requirements and providing additional cylinders to provide the added thrust was not an issue. For this application, six 203mm x 0.9 metre cylinders provided the necessary 24,000 pounds of thrust.
The open area between the cylinders allowed the gate to be installed around an existing material feed chute.
Diverter Valves
Another application involved a large flapper-style diverter (0.9 metre x 1.4 metre). A US-based coal-fired energy plant utilized a diverter of this size to handle 203mm ‘minus’ coal.
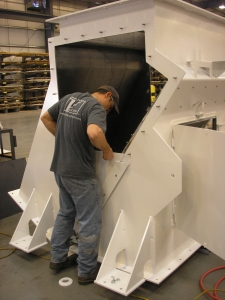
Over the years, the plant operators discovered that replaceable polymer liners worked well in addressing interior abrasion from the material handled. The major issue they faced was that the liners needed to be replaced approximately every 18 months.
Replacing the liners was a long, tedious, and expensive proposition. Due to the fact that access to the interior of the diverter was limited, production was shut down and a crane had to be sourced and rented to remove the 1,900kg diverter from place. Once removed, maintenance personnel had better access that allowed replacement of the liners. Then the diverter was hoisted back into place and re-installed.
Another issue was that the leading edge of the flapper blade rested against the diverter’s interior housing and was exposed to the material flow stream. Over time material would gradually wear away the tip of the blade, affecting the blade’s ability to seal product.
Two features that are standard with any Vortex diverter solved the customer’s issues:
Access Panel: Vortex diverter valves are manufactured with a removable, side access panel. This feature allows for inline inspection and maintenance. In most cases, replacement of interior parts can be accomplished without having to remove the diverter from place. For this application, Vortex added additional access areas to permit easy replacement of the polymer liners. Production loss was minimized major savings in maintenance costs were realized. The customer commented that “after two interior liner replacements, the diverter was paid for.”
Recessed Blade Compartment: Vortex flapper-style diverters are designed to shield the leading edge of the blade. Whether in the open or the divert position, the blade over strokes into an area where flowing material does not come in contact with the leading edge. Properly shutting off material flow prior to changing the position of the blade ensures that there is never an issue with leading edge blade wear.
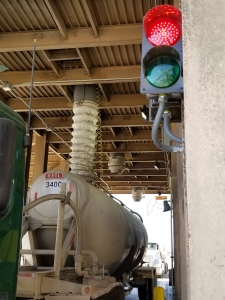
Telescoping Loading Spouts
Vortex Telescoping Loading Spouts are utilized in lorry, rail, barge, and ship loading operations. Vortex’s four-cable hoist drive offers enhanced stability and improved cable service as opposed to traditional two and three cable drives. Additionally, the use of three-piece, CNC machined pulleys with rounded edges and precision cable grooves drastically limits the cable wear experienced with traditional spouts.
Fly ash, the byproduct from burning pulverized coal in electric power generating plants, is utilized by many industries and especially by concrete manufacturers. Fly ash improves the workability, durability, and strength of concrete. As such, it is in great demand by the cement industry.
Independent companies throughout the US operate numerous terminal locations where concrete and ready-mix operations have a local source supply of fly ash. Contracts are established with fly ash producers and that material is transported to the terminals.
Vortex telescoping loading spouts are utilized at many of the producer and terminal locations to load fly ash into lorry and rail car vessels for transport. The standard features of the Vortex spouts offer a smooth, maintenance-friendly operation. Additionally, Vortex offers filters and positioners to complement its spout line.