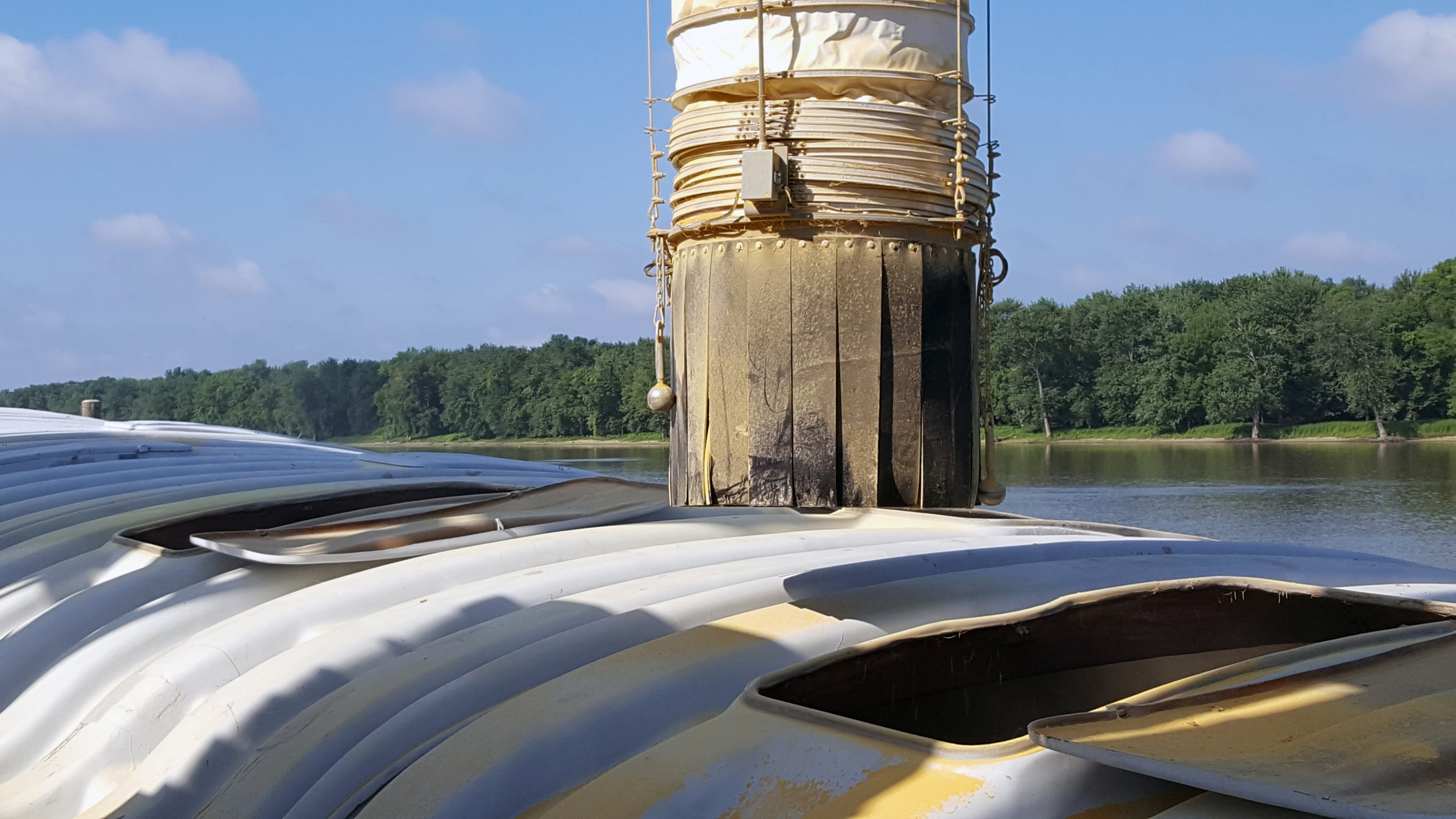
Client:
Quantity:
Size:
Application:
As featured in Dry Bulk Magazine
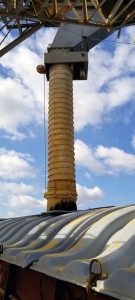
by Kevin R. Peterson
Barge freight is extremely energy efficient, considering the number of kilometers 1 t of material can be carried per liter of fuel. For instance, material transported by lorry will travel 25 km, material transported by rail will travel 85 km, and material transported by barge will travel 218 km.
Barges are available in different sizes. The typical European barge is 76.5 m long by 11.4 m wide, while the American barge is 59 m (195 feet) long by 11 m (35 feet) wide. In comparison to lorry and rail units, the cargo capacity of typical river barges is massive:
• Lorry – 23 t per unit
• Rail – 91 t per unit
• European Barge – 2700 t per unit • American Barge 1,361 t per unit
Barges normally move down river in a group of 15. Just one group of American barges equals 216 rail cars or 1,050 lorries. For facilities located on major waterways, barge freight offers definite material handling advantages.
When considering a product such as grain, for instance, with capabilities of loading 907 tph, a standard river barge can be loaded in a couple of hours. Compare this to the logistical nightmare of loading 60 lorries. Barges allow incredibly quick loading and movement of product.
Besides fuel efficiency, capacity and time constraints, other advantages of water transportation are that it is much safer (less accidents), offers less congestion and air/noise pollution, and creates minimal social impact.
As with any subject, there are also disadvantages. In the case of river barge transportation, it is much slower (so is not recommended for perishable goods), it is costly and time-consuming for short distance transport, and river levels and conditions can create potential shipping issues.
Worth noting, according to statistics, approximately 15% of US freight is carried by inland barges compared with almost 50% in the European Union.
Barge loading
There are many factors to take into consideration when loading river barges. River levels will change dramatically during the year, the level of the barge changes as the unit is filled with product, and typical loading systems will not reach the entire span of the barge.
Different types of river barge loading systems are available. They include open chutes, flexible hoses, belt conveyors, telescoping booms, and articulating arms.
Each consideration for loading offers pros and cons. Factors such as types of material handled, frequency of loading, ease of maintenance, overall equipment costs, and environmental concerns should be taken into consideration.
When loading material into river barges that contain individual hatch openings, it is important to be able to deposit material vertically into each opening for ease of loading, control of dust particulate, and limit wear to the equipment.
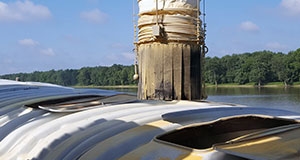
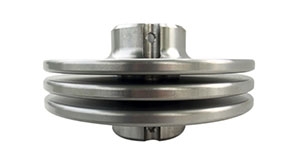
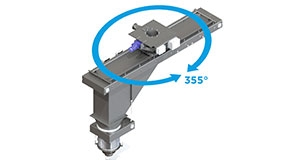
Due to the cost of many of the boom-type systems, typical hatch-style barge loaders utilise a loading system where a fixed loader supplies material to a barge that is moved multiple times during the loading process.
Case study – improving on an existing loading facility
One company that employed the “move the barge” style of loading wanted to make their process of loading agricultural-based products more efficient. The barges to be loaded contained 18 staggered loading compartments – nine on either side of the unit. The existing loader featured a long, flexible hose tied to a pulley that was used to load each compartment. The hose was fed by a belt conveyor. However, the hose could only reach one of the loading compartments at a time. As such, the barge was physically moved each time a new compartment needed to be accessed and loaded – a total of 18 separate movements. The hose was positioned at an angle which created premature hose wear causing maintenance issues and excessive downtime.
In considering an alternative to their loading procedure, one customer consulted Vortex Global, a US manufacturer of telescoping loading spouts. They agreed with the idea that if a spout that could be placed so material flowed directly into each compartment, there would be less equipment wear issues. However, they were aware of existing spouts that actually created additional maintenance issues, especially with their use of hoist cables. The main issues involved wear to the cables utilised to extend and retract the spout itself and the pulleys used to extend and retract the spout.
Addressing cable lifting systems
The typical telescoping loading spout employs either a two or a three-cable lifting system. With this system, major problems can occur if the cable breaks due to excessive wear. Should a cable break, it would need to be replaced immediately as the spout cannot be raised or lowered with just one or two cables. Of course, this results in unscheduled maintenance and downtime.
Vortex has standardised a four-cable hoist drive system. Four cables offer better stability and even weight distribution. The result is less stress to each lifting cable which reduces cable wear, increases the cable service life factor, and prolongs cable service life. Should a cable that is a component of a four-cable system break, the other three cables are capable of continuing to lower or raise the unit until maintenance can address repairs.
Addressing cable pulleys
Another issue that Vortex addresses is the cable lift pulley itself. The typical cable pulley contains a “sharp” edge. As the cable spools in and out of the pulley, that edge creates premature wear to the individual wires of the cable. Over time the cable will eventually wear and break.
The width of the pulley opening creates additional concerns. If the width is not sized exactly to the diameter of the wire cable, the cable will wind onto the pulley instead of overlapping itself. It becomes bound between the previous cable wrap and the side of the pulley. This causes additional cable wear and, more importantly, also creates slack within the cable (backlashing) as the spout is lowered and the cable unwinds from the pulley. The slackened cable has a propensity to “jump” the confines of the pulley before wrapping around the pulley shaft. If this happens, the loading process must be suspended until the cable is freed from the shaft.
Vortex’s CNC-machined, three-piece pulley with rounded edges and precision cable grooves ensures smooth, balanced spout extensions and retractions, and addresses the cable-related concerns expressed by barge loaders.
The dust skirt
A dust skirt is typically added to the bottom of the spout for open loading applications. It is constructed from heavy, durable neoprene rubber. Rather than flaring a skirt from a common piece of rubber, each flared section is a stand-alone strip. Individual strips overlap each other to help limit pathways for dust emissions into the atmosphere.
Positioning the spout
The company was also interested in addressing loading efficiency without spending a fortune to install transport booms or pivoting gimbals. The idea of a rotating horizontal positioner was addressed and quoted.
Vortex provided a positioner that travels horizontally and rotates 355°. The positioner allows for the spout to be positioned vertically above the loading hatch anywhere within a circular diameter that is twice the travel of the positioner. By utilising this positioner, the customer could reach two barge compartment openings with each reposition of the barge. The barge would only need to be moved nine times instead of the previous 18 times. The cost savings just to move the barge was a huge plus.
Considering loading rates and river height variances, a 610 mm Vortex spout with 10 m of vertical travel was ordered for the project.
The telescoping spout has been in service for 3 years now, providing reliable service for this river barge loading operation.
Looking ahead
Going forward, transportation of certain materials by river barge will face certain challenges, much like in other industries. Maintaining infrastructure, equipment, industry consolidation, environmental and government issues are just a few of many considerations.
In the midst of increasingly congested highways and railroads there is a growing world population in need of deliverable goods. It is refreshing to know that equipment manufacturers are continuing to address products that offer loading efficiency and reduced maintenance for companies using river barge transportation.
About the author
Now in his 24th year with the company, Kevin R. Peterson is the Business Development Director for Vortex Global. A board member of the Industrial Minerals Association of North America, Kevin travels extensively to meet with customers and customer prospects. He has created and shared hundreds of case studies and written numerous articles that share the successes Vortex products have experienced with industries that handle and process dry bulk material.