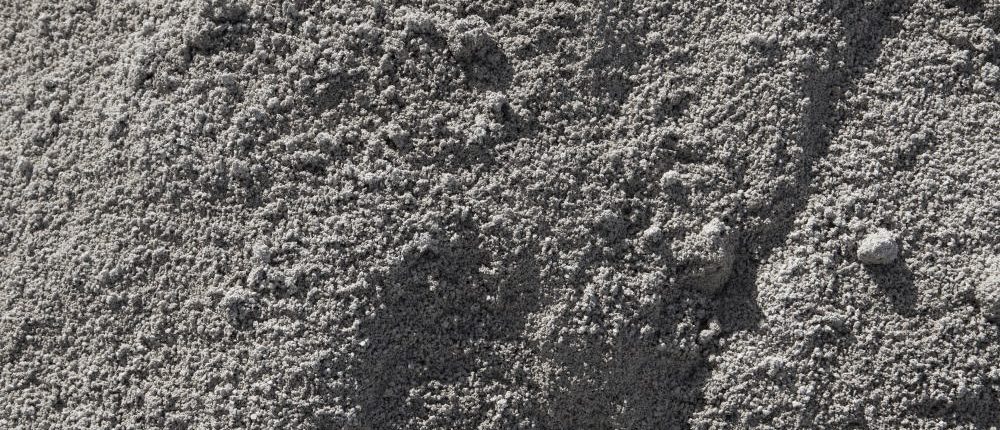
Client:
Quantity:
Size:
Application:
Introduction
In August 2015, one of the representative groups for Vortex Global approached Vortex regarding a customer issue with the valving used to shut off material in a finished cement pressure transfer line. The company manufactures and distributes cement worldwide. The problem existed at one of its plants located in the US.
The Problem
At the point in the operation where finished cement was being transferred to storage bins, butterfly valves were being incorporated to open or shut off the flow of cement to ten different storage bins. Cement was conveyed through the system at approximately 35 psig (2.41 bar). A butterfly valve consists of a circular disc located within the convey line, with its pivot axis at right angles to the direction of the flowing material. To shut off material flow, the disc rotates to close into an elastomer seat. The valves were a constant source of irritation. The disc closing on the abrasive cement quickly wore the seat to the point where the valve would not properly seal the material or the conveying line pressure.
While butterfly valves are a good choice when handling air, gas, steam, or liquids, care must be taken when applying a butterfly valve to a semi-abrasive or an abrasive dry material. Common challenges in this type of application include the following:
- In the open position, the exposed disc is susceptible to premature wear from the handled material. The exposed disc also reduces material flow.
- Upon closing, material can become trapped between the valve’s disc and the elastomer seat. If a significant amount of material is trapped, the disc is unable to fully close, causing air loss and material leakage through the valve.
- As the disc closes, it grinds dry material against the valve’s elastomer seat. Over time, this type of wear will cause the elastomer seat to erode or tear away. The wear and abrasion of the disc and the seal create ongoing issues in maintaining and even replacing the valves.
Such was the case at the aforementioned cement plant. The maintenance department grew tired of spending their time on top of 100 ft (30 m) silos, allocating their budget to valve repair and replacement. The customer asked the local equipment representative if a solution existed that could be considered.
The Proposal
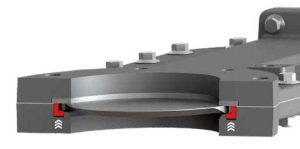
The Vortex TPV slide gate was suggested as a replacement. Vortex engineered this gate specifically for highly-abrasive applications that required minimal maintenance over the life of the valve.
The Vortex TPV is a fully bonneted slide gate consisting of cast ductile iron flanges and a hardened 440C stainless steel blade and seat (440C stainless measures between 58 − 65 on the Rockwell C hardness scale). The design of the gate addresses safety issues (the moving blade is fully enclosed) and environmental issues (no external bonnet seals to contend with and material is prevented from escaping into the atmosphere).
Not only does the blade address abrasion and wear issues, it is unique in its patented design. The blade is kept in constant contact with its seat through its entire stroke with the aid of blade guides (Figure 1). The guides are supported by multiple wave springs on both sides of the blade. The guides apply constant upward pressure to help seal the gate. As the blade closes, its beveled leading edge slightly lifts into the metal end seat. Beneath the closed leading edge is a displacement pocket that allows material to “fall away” rather than packing and jamming, which cause wear to the blade and seat.
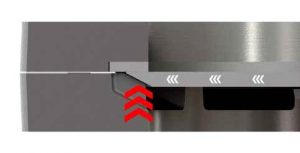
Figure 2: Beneath the closed leading edge is a displacement pocket that allows material to “fall away” rather than packing and jamming, which could otherwise cause wear to the blade and seat.
Because the seals for the TPV are metal, the gate is rated for use in higher temperature applications, over 660° F (350° C). In this particular application, the material temperatures would be between 160 − 250° F (70 − 120° C).
Vortex engineers equipped the TPV slide gate with an air purge port. This port is used to pressurize the valve body, keeping material in the flow stream and out of the gate. The air purge is essential when conveying fine material in higher-pressure applications.
The customer was informed that the special blade design made it necessary for the gate to be mounted in a horizontal plane in the case of a vertical convey line or on its side (actuator parallel with the ground) in the case of a horizontal convey line. This mounting is necessary to keep material from building up in the area where the displacement pocket is located. In this application, the convey lines were horizontal and the required mounting specifications would not be an issue.
Consideration & Solution
The customer purchased and had success with Vortex slide gates and diverters in the past; however, it was not aware of the newer TPV slide gate. The customer asked for a quotation in an 8 in. (200 mm) size. The quotation came in at a higher cost than the plant expected and plant personnel decided to look at other options.
During the next four months, the maintenance planner researched different gate valves. There were many rounded blade gates that were similar to the Vortex gate; however, these gates presented the following concerns that they felt were mechanical disadvantages:
- The flat blade closing on material into an elastomer end seal would surely abrade away the seal over time (or cause material build up not allowing the blade to completely close). This would create leakage of material and air within the system.
- The exposed blade created external pinch points: a safety hazard.
- Once the exterior bonnet seal wore through, material would escape to atmosphere: an environmental hazard.
When comparing costs with a butterfly valve, the planner learned that the cost of the TPV seemed high; however, there were less cost differences between the TPV and similar slide gates. It was calculated that if the TPV slide gates could last 6 months without having to make repairs, they would more than pay for their purchase.
In the middle of December 2015, a purchase order was submitted for eight, pneumatically actuated, 8 in. Vortex TPV slide gates. The gates shipped in January 2016, and were installed in February of that year. An additional number of 8 in. TPV Gates were ordered six months following the install of the initial gates. At the writing of this article (December 2017), no repair parts have been ordered for any of the Vortex TPV gates.
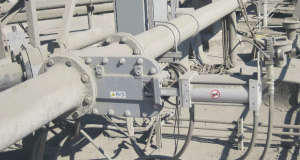
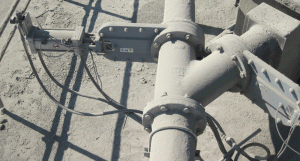