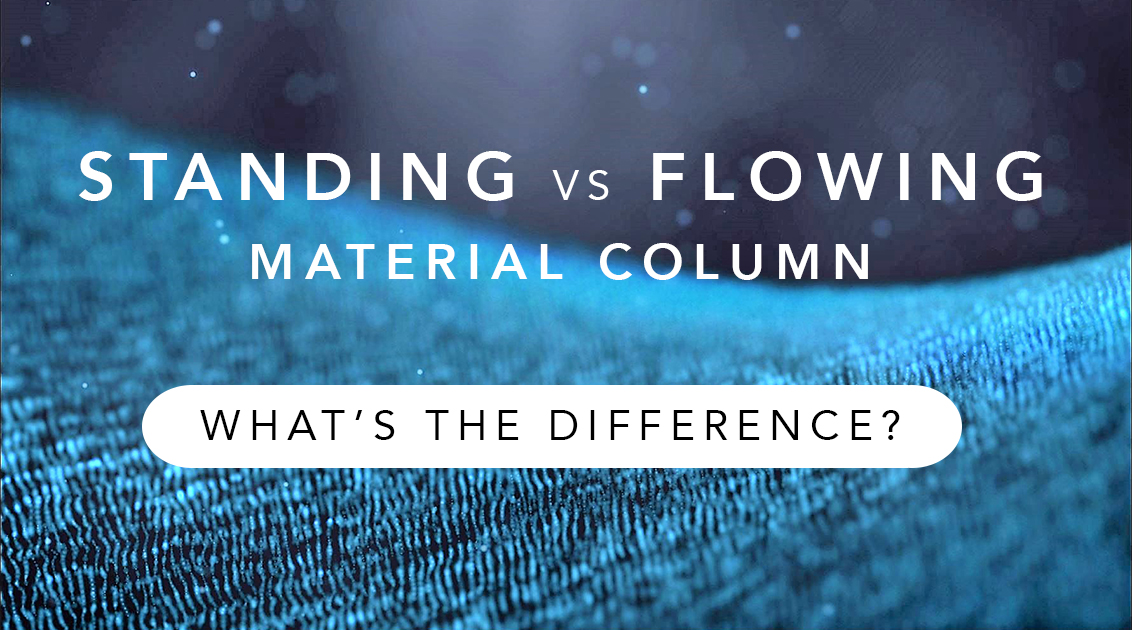
Client:
Quantity:
Size:
Application:
In process engineering, for every solution to consider, three more considerations often arise. Material conveyance and valve selection are no exception. This white paper will address the difference between a standing column of material versus a flowing column of material, as well as considerations to be made when selecting a process gate to address each.
Standing Column of Material
A “standing column” describes material accumulation above and below the gate.
Flowing Column of Material
A “flowing column” describes materials freely passing through the gate.
What's the Difference?
The primary difference is that a “standing column” describes static materials at rest, while a “flowing column” describes suspended materials in motion.
Are the Two Mutually Exclusive?
No. A process gate intended primarily for closing through a flowing column of material may also be tasked with closing through a standing column of material, in some applications. For example, a process gate may normally close on a flowing column as materials discharge from a silo into a belt or screw conveyor. If the conveyor below malfunctions, materials will build up between the conveyor and the silo. So that conveyor maintenance can be performed, the process gate must be closed through a standing column of material to minimize product loss out of the silo. If a process gate cannot be closed through a standing column of material, a maintenance gate may be necessary, in addition to the process gate.
Considerations
Equipment Above & Below
As exemplified above, equipment above and below the gate can determine whether or not a process gate must also serve a maintenance purpose.
Material Type/Particle Size
Generally speaking, closure through a standing and/or flowing column of material becomes increasingly difficult with larger particle sizes. For example, closure through fine materials and powders, such as flour, is relatively simple, while closure through larger sized aggregates is quite challenging. Contact us to discuss your materials handled and their suitability for closure on a standing and/or flowing column.
Material Bulk Density
The handled material’s bulk density is a primary variable in calculating force required to close through a flowing or standing column of material. If material bulk density surpasses the load-bearing capacity of the sliding blade, it can put undue stress on the blade and create issues in gate closure. Contact us to discuss additional engineering considerations and specifications.
Closing Force Requirements
Generally speaking, less force is required to close through a flowing column of material, compared to the force necessary to close through a standing column of material. The reason being that flowing columns have space available for materials to be manipulated, putting less resistance on the closing blade, compared to a standing/static material column.
Actuator Type/Size
Depending on application, a standard actuator size may not supply the force required to close through a flowing or standing column of material. To provide the necessary closing force, Vortex engineers consider gate type, gate size and actuator type, among other variables, to upscale the gate’s closure capabilities. Contact us to discuss additional engineering considerations and specifications.
Accessories for Closing through Material Columns
In both standing and flowing column applications, a Special Service Inlet can assist with seal wear and closing force. By design, a Special Service Inlet acts as a funnel to direct material flow through the center of the gate. Its primary purpose is to create a void between materials, the blade, and the gate’s seals. For protection against seal wear and actuation issues, a Special Service Inlet allows materials remaining at the leading edge of the blade to fall away before entering the end seal, which hinders material packing. For enhanced closing force, the Special Service Inlet’s inherent void allows the blade to begin and conclude its closure process with little resistance from materials.
Tip: Seek Expert Advice
If a gate will be tasked with closing through a standing and/or flowing column of material as part of your manufacturing process, it is recommended to first contact your valve supplier to discuss the gate’s suitability for that application. With 300 years of combined application experience and dry bulk handling expertise, Vortex engineers rely on in-depth knowledge to develop the right solutions for even the most demanding applications.
For more information about standing and/or flowing columns of material, or to discuss your material handling application, please contact us.