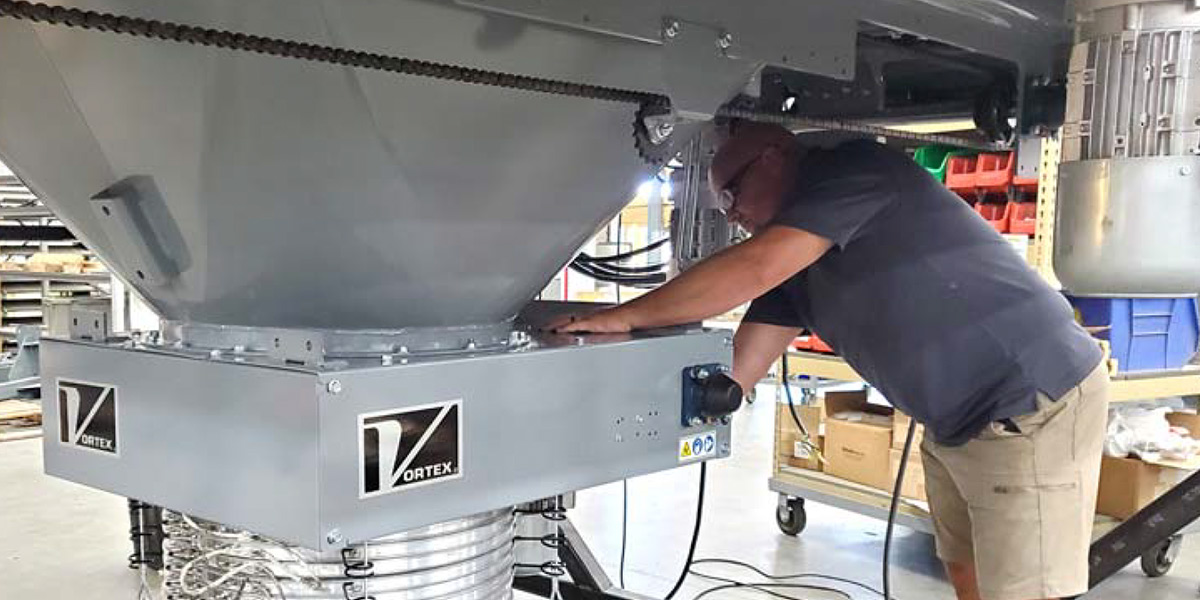
Client:
Quantity:
Size:
Application:
As published in BMHR, a supplement to World Cement
By Austin Anderson
The loading of dry bulk material into trucks and rail cars can be a complex endeavor. From flow rate, dusting concerns and equipment stack up heights – many factors are taken into consideration for each specific application. All of these elements can be attributed to the positioning of trucks as they enter and exit a loadout facility.
The implementation of a loadout system incorporating a positioner at truck loadout stations can eliminate the need to reposition vehicles once they have entered the loading station saving valuable time and preventing unnecessary wear and damage to a loading spout.
While many truck drivers master the art of positioning trucks for loadout, some find the skill more difficult. Frequent and improper repositioning of trucks can lead to a plethora of negative effects on your loading spout and loading process including damage and unnecessary wear to the spout, costly spout maintenance and material dusting within your facility and to the atmosphere.
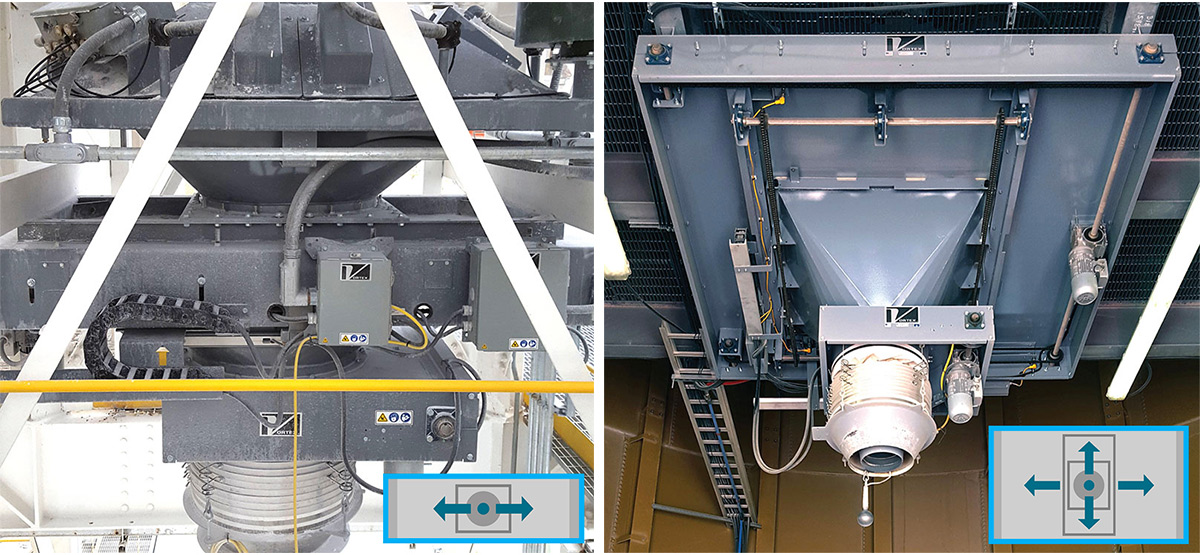
In the case of an improperly positioned truck, the spout scavenger is not seated properly into the hatch. This allows for dust to escape into the atmosphere causing both employee and environmental health and safety concerns. As facilities face tighter regulations and restrictions by local and federal agencies to protect their employees and prevent environment pollution, controlling dust is a key component in loadout processes.
Issues faced by employees in dust-ridden environments include irritated skin to due allergic reaction, irritation of the lungs due to inhalation of potentially toxic materials, and slips, trips and falls due to dust accumulation on surfaces. Fugitive dusts can also accumulate to form a dust cloud that can ignite, burn, and, in some instances, explode.
In addition to dusting, the irregular material flow through the angled trajectory of a misaligned can exacerbate unnecessary wear to the interior cones and outer sleeve. Continuous and frequent wear leads to expensive maintenance and the ability for even more dust to escape.
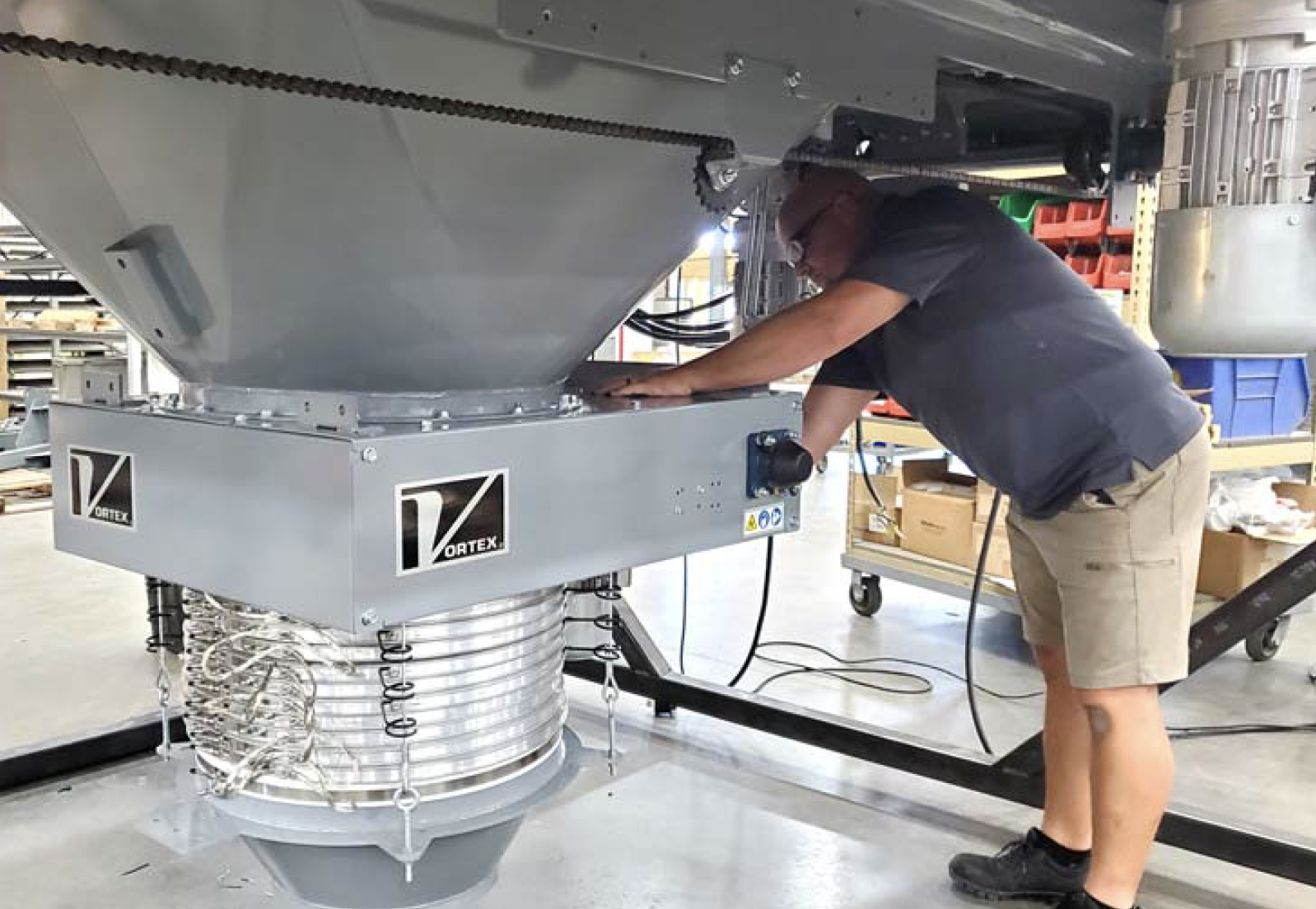
Vortex Loading Spout Positioners
Loading Spouts provide fast and steady material flow during the loading of dry/bulk solid materials in open and/or enclosed vessels such as trucks, railcars, tank vehicles, ships, barges, and stockpiling. When paired with additional products from Vortex’s line of loading solutions products, such as positioners and filters, the loading process can become even more efficient.
Vortex offers a complete line of telescoping loading spout systems for the loading process. These loading solutions systems can be custom engineered to meet the most demanding and complex loadout application requirements, including corrosive or hazardous materials, long distances, low and high temperatures, etc.
The Vortex Loading Spout Positioner is used in conjunction with standard volume loading spouts to facilitate and speed up the loading of open or enclosed trucks and railcars at loadout stations. The positioner allows for the fast and accurate single-axis or double-axis placement of the loading spout, which eliminates the need to reposition vehicles once they have entered the loading station. Loading spout positioners are made from steel and can be designed and manufactured to meet individual project specifications to handle almost any flow rate and travel distance.
These spout positioners are designed so that materials pass through a fixed inlet. Below, a traversing hopper slides across a fixed support pan. The support pan stays stationary, allowing the hopper to easily slide and find its destination. A loading spout is attached beneath the hopper to allow exact positioning of the spout above a truck or railcar waiting below.
Depending on the application, positioners can be designed with a single or dual axis. The single-axis positioner allows spout movement along either an X-axis or a Y-axis. Depending on orientation, a single-axis positioner can either be moved from front-to-back or side-to-side above a loading vessel. A dual-axis positioner allows spout movement along both an X and Y-axis, allowing it to traverse from front-to-back and side-to-side above a loading vessel.
The inlet cone and traversing hopper are constructed from the same metal material(s) as specified for the corresponding loading spout’s material contact areas while the fixed support pan is constructed from A36 mild steel.
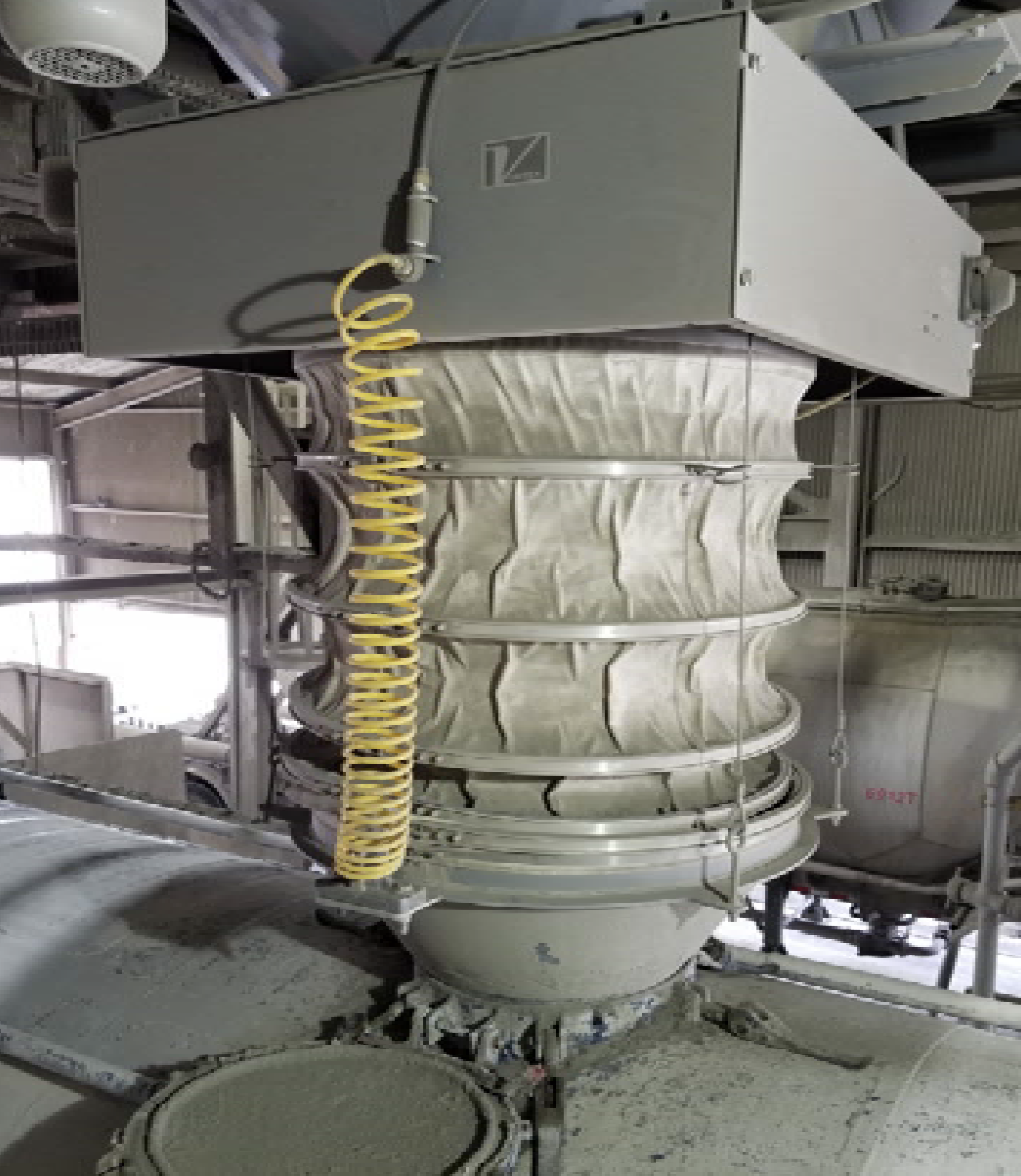
Case Study: Cement Plant Utilizes Vortex Loading Spout and Dual-Axis Positioner
A Vortex Loading Spout is utilized by an American cement plant to load cement into trucks and features a dual-axis positioner for ease of loading.
Application:
This 20” (508 mm) telescoping loading spout features a larger load rate capacity (400 – CFM). The Vortex Dual-Axis Spout Positioner allows the spout to traverse along both an X and Y axis (front-to-back and side-to-side).
Features & Results:
The larger spout allows trucks to be loaded quicker than a spout having a smaller load rate capacity. The dual-axis positioner enhances faster loading because trucks no longer need to waste precious time to reposition themselves directly below the spout.
Case Study: Loading Spout, Positioner, and In-Line Filter Handling Hydrocarbon Powder
A coal refinery sourced three items from the Vortex Loading Solutions line to assist in the handling of hydrocarbon powder: a loading spout, dual-axis spout positioner and an in-line filtration system.
Application:
These Vortex Loading Solutions products will be used in the coal refinery’s process of processing waste coal and turning it into a clean carbon fuel.
Features & Results:
The telescoping loading spout features a four-cable hoist system and CNC machined cable pulleys for less spout maintenance. The dual-axis positioner allows for 2’ (.6 m) of spout movement along the X and Y axis so trucks do not need to reposition when loading. An in-line filter traps dust during loading and reintroduces it back into the load reducing waste, increasing profits and keeping the facility dust-free.
Case Study: Loading Spout and Positioner Handling Industrial Sand
In this application, a loading spout (14” 355 mm) is attached to a traversing hopper that is part of a Vortex Dual-Axis Positioner. The system is used by a west Texas terminal to handle industrial sand.
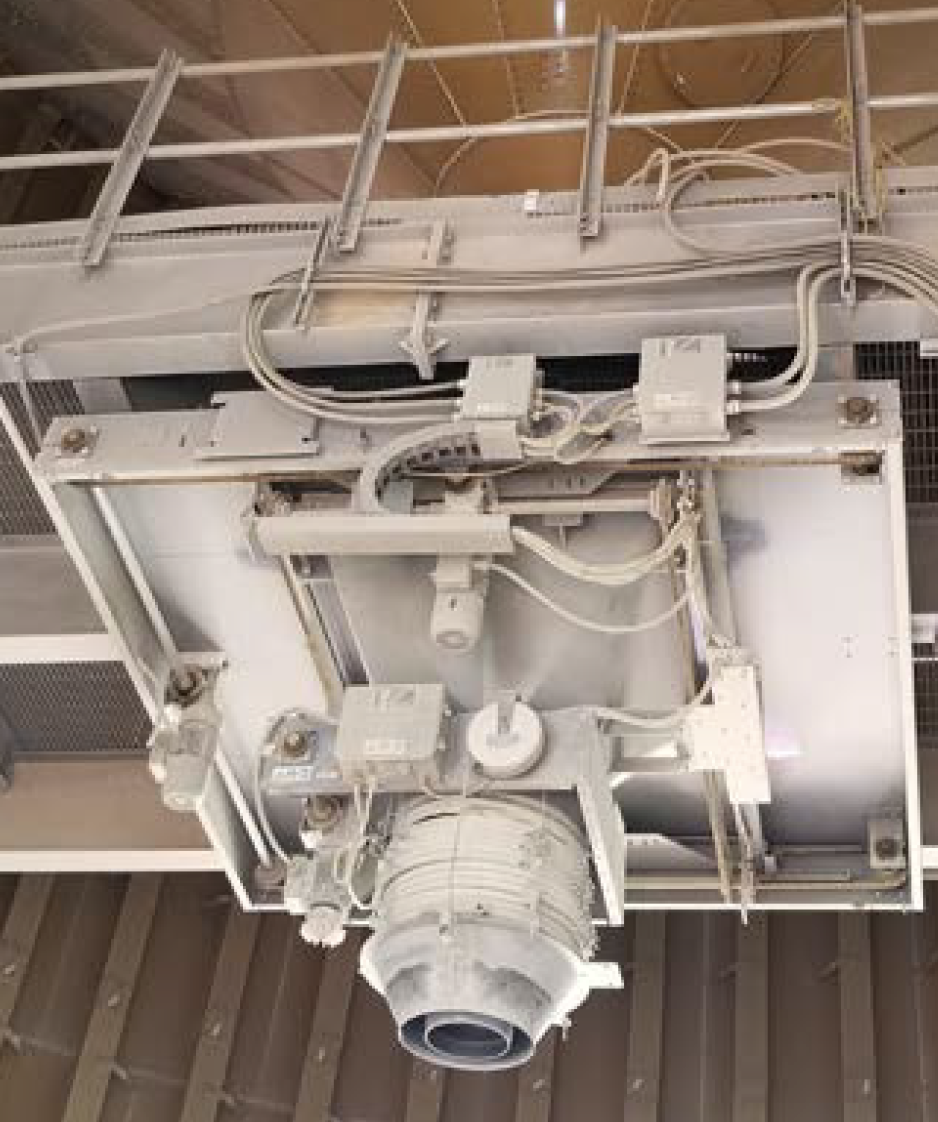
Application:
Loading is more efficient as trucks entering the loading bay do not have to spend additional time repositioning themselves directly beneath a fixed spout with no positioning capabilities. Wear to the spout’s internal cones is greatly reduced as material is properly routed (vertically) through the spout.
Features & Results:
The spout itself was ordered to provide six feet (1.8 m) of vertical travel down to a truck loading hatch. The positioner moves the hopper/spout along both an X and Y axis. This positioner was ordered to allow two feet (.6m) of travel in either direction.
Conclusion
When properly applied to a loading process, a loading spout positioner can greatly reduce the amount of time it takes for the vessel below to position itself. When filling open containers, positioners also ensure material is distributed evenly throughout the vessel. A loading spout coupled with a spout positioner is the key to an efficient and prompt loading system.