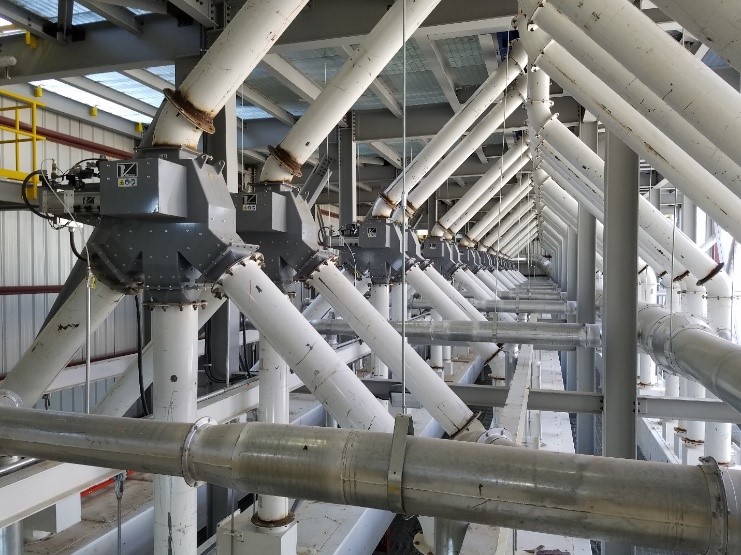
Client:
Quantity:
Size:
Application:
As published by Rock Products – February 2018
When the need arises to divert dry bulk material during gravity flow situations, one normally considers a typical flapper style diverter for the application. In applications where the sealing of non-abrasive, fine material is involved, the flapper is a perfect choice. There are applications and material handling situations, however, where a different style diverter might offer distinct advantages over a flapper. The Vortex Pivoting Chute Diverter embodies those advantages.
The Flapper Diverter
As stated, there are many applications where a flapper diverter is the diverter of choice. There are circumstances where one might consider a different diverter style.
When handling fine, abrasive material, the seal surrounding the flapper blade will be subject to extreme abrasion as the blade shifts and the seal grinds material between it and the interior diverter housing. Under this condition the material handled will create premature wear to the seal, eventually allowing material to escape into the outlet that is required to be closed.
When handling larger sized abrasive material, the blade and diverter interior must be designed to address abrasion and material impact. Often the portions of the diverter that experience material contact should additionally be lined with abrasive-resistant steel, chromium carbide, polymer, or other material suited to the application.
The flapper diverter is not designed to be shifted when material is passing through the diverter (shift “on the fly”). Fine material carried by the leading edge of the blade has a tendency to build up on either side of the interior housing. Once build up occurs the material seal is negated. Larger material at the blade’s leading edge will become trapped between the leading edge of the blade and the interior housing. This, too, negates the seal and additionally can create breakage of the blade, blade shaft, or actuation problems.
In certain instances, the application calls for flowing material to be directed to two destinations at once (splitter diverter). In the case of a flapper diverter, the leading edge of the blade must be protected from abrasion and wear created by the blade being positioned in the middle of the material flow stream. This situation creates other considerations including positioning and maintaining the integrity of the blade position (hard to accomplish using a pneumatic actuator) and additional wear to either side of the blade shaft.
The Pivoting Chute Diverter
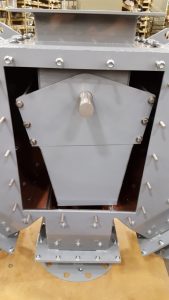
The Pivoting Chute Diverter was designed to offer uninterrupted flow of larger sized, abrasive materials such as aggregates and minerals. However, since the diverter has no interior seals to contend with, it also addresses applications handling smaller sized, abrasive material such as sand and limestone that typically wears out the internal seals of a flapper diverter.
The material contact areas through the standard Vortex Pivoting Chute Diverter (wetted parts) are designed to address abrasion and wear. The inlet chute, pivoting chute, and diverter outlets are constructed of abrasion-resistant steel (400 BHN). For applications requiring additional wear resistance, optional materials such as chromium carbide is available.
Due to the fact that there are no internal seals, very fluidizable material may migrate to the “off” leg (the outlet not being conveyed through). Vortex installs a replaceable material containment bar at the interior juncture between the diverter’s outlets. This aids in directing errant material through the desired outlet.
A major advantage of the Pivoting Chute Diverter is the ability to “shift on the fly” when handling smaller sized material. The material must be smaller than the clearance between the material containment bar and the bottom of the internal chute. If the material is larger than this clearance, it is suggested that the material flow be stopped prior to moving the interior chute.
The pivoting chute may be used as a “splitter” valve to direct flowing material to two outlets simultaneously by positioning the interior chute between two outlets. Depending on the abrasive qualities of the material handled, extra wear protection of the outlets may wish to be considered. (An electric actuator is typically employed in this type of application, as with a pneumatic actuator the chute has a tendency to “drift.”)
*Note: Keep in mind that when considering the Pivoting Chute Diverter that:
1) the stack-up height (flange to flange dimension) is taller than a flapper diverter; and
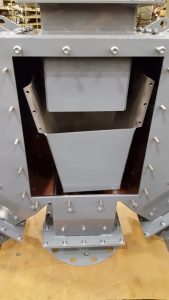
2) without internal seals there is the possibility of material dusting to the leg(s) not being conveyed through.
The Vortex Pivoting Chute Diverter
- Dust-tight to atmosphere.
- Standard size: 6 – 24 in | 150 – 610 mm (Custom sizes are available)
- Can handle material temperatures up to 400° F | 205° C, as a standard.
- Available in two- & three-way configurations.
- Choice of pneumatic, electric or hydraulic actuation.
- Optional round-to-square or square-to-round inlet & outlet transitions.
- Diverter body includes a front access panel, allowing inspection or maintenance of the diverter to be made without having to remove the diverter from place.
- Removable internal pivoting chute & inlet chute.