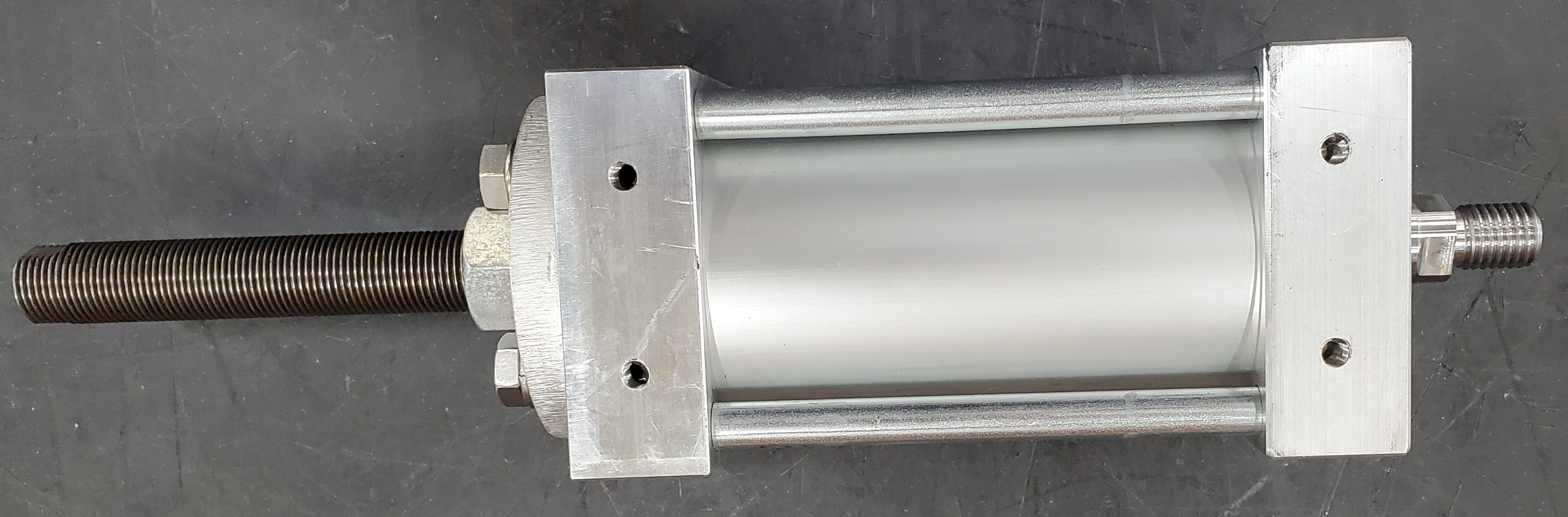
Client:
Quantity:
Size:
Application:
Slide gates are typically utilized to completely open or completely shut off material flow within a conveying system. There are material handling applications that demand the ability to limit the material amount that flows through the slide gate. These applications include:
- Batching – precisely measuring different ingredients before mixing them.
- Dribble feeding – limiting material flow prior to obtaining a desired weight.
- Loss-in-weight feeding – adjusting material discharge rates.
- Metering of material – controlling material flow into conveyors, mixers, or blenders.
- Scaling – obtaining a specific material weight.
Slide gates are usually controlled by electric or pneumatic actuators. An electric linear actuator has the ability to provide very precise blade positioning. In environments where cold temperatures are present or compressed air is not available, electric actuators are a good choice. However, electric actuators are expensive and move the blade at a slower speed.
When considering applications where the adjustment of material flow is involved, the ability to quickly move the slide-gate blade to an intermediate position between fully open and fully closed is essential. Pneumatic actuators are less expensive and have the ability to quickly reposition the blade. A pneumatic actuator is made up of an air cylinder, piston or diaphragm, rod, and valve stem. Several control options for material flow control devices are available to add onto a pneumatic actuator to assist in measuring material.
Control variable position open option
One material flow control option is the control variable position open (CVPO) modification, which is useful for applications that need to limit the full-open position so as to not flood downstream processes. With the CVPO modification, the air cylinder itself is equipped with a threaded rod at the cylinder housing’s end, as shown in Figure 1, opposite the actuator rod (the rod attached to the blade). The threaded rod may be manually adjusted to limit the opening stroke of the blade. The air cylinder piston contains a magnetic strip that allows proofing – the ability to determine the blade position – through the use of a magnetic reed switch mounted to one of the air cylinder tie-rods. As the opening stroke of the blade is changed, the magnetic reed switch can be manually repositioned accordingly. When using this option, the full-open position of the blade becomes the setpoint established by the threaded rod.
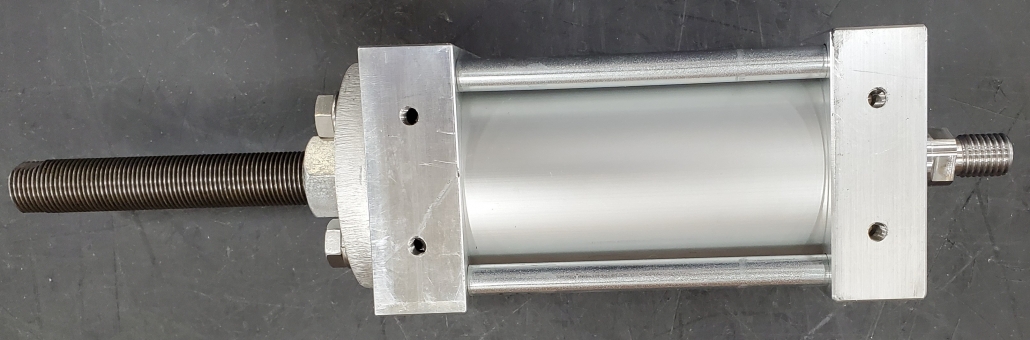
Be aware that not all pneumatic actuators are built with a magnetic strip in them. Sometimes, the magnetic strip is sold as optional. However, not incorporating a magnetic strip in a pneumatic cylinder upon purchase and needing a strip later on can create issues. Be sure to verify with the vendor that the pneumatic actuator comes with a magnetic strip.
Two-stage air cylinder
Another material flow control option is the two-stage air cylinder, which is suitable for applications where the blade needs to only stop at the exact same intermediate position every time. The two-stage, three-position pneumatic cylinder features an air cylinder connected to another air cylinder as shown in Figure 2. The combined cylinder provides blade positioning at blade open, blade partially open, and blade closed. Each individual cylinder is manufactured in a length to accommodate the required blade-partially-open position. Through the use of air control solenoids, the blade can be moved from one position to another. The intermediate blade-partially-open position is predetermined and cannot be changed.
Please note that the air control solenoids for the pneumatic positioners are installed in such a way as to maintain equal pressure on either side of the air cylinder piston (and keep the blade from drifting when the blade is in an intermediate position). A minimum, constant air pressure of 80 psig is required for operation.
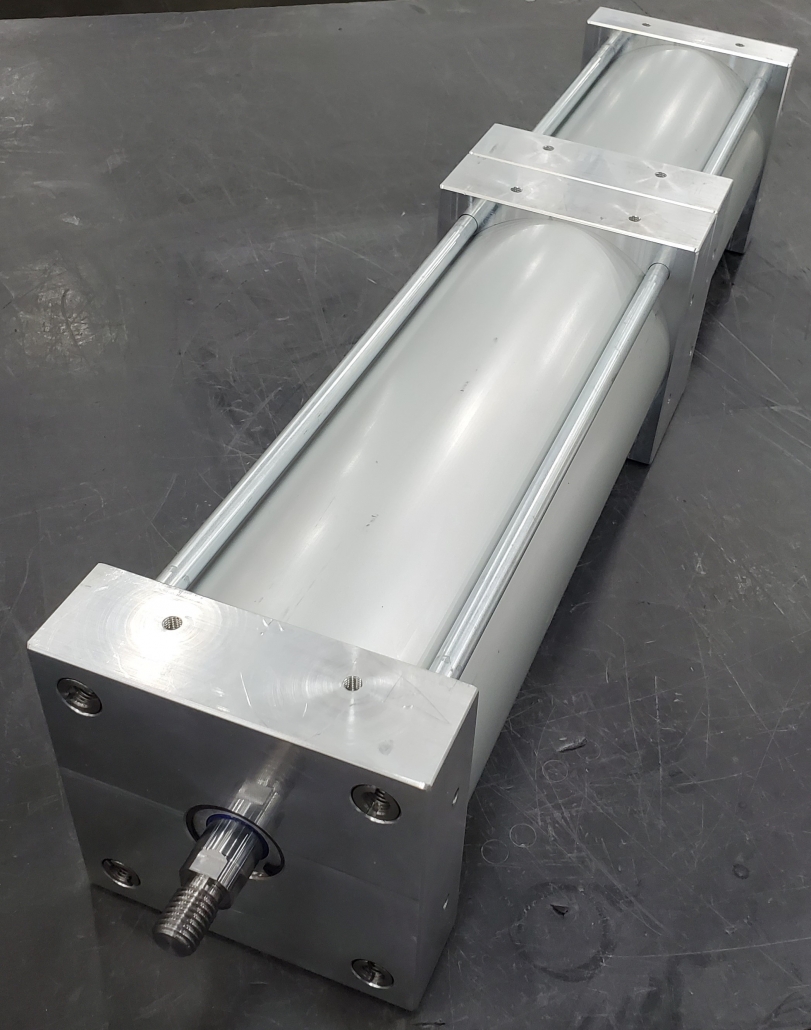
Variable position open assembly
The variable position open (VPO) assembly is another material flow control device and is used in applications when control of where the blade should be positioned during the opening blade stroke is important. This is especially useful when dribble feeding material prior to fully opening the gate is necessary so as to not immediately flood the downstream process. The VPO assembly allows manual adjustment of the intermediate blade position through the use of air control solenoids and a pneumatic trip switch. A threaded rod attaches to the blade on one end and to a polymer block on the other end. The polymer block moves back and forth within a housing that is attached to the pneumatic cylinder’s side. An adjustable pneumatic trip switch is contained within the housing. During the blade’s opening stroke, the polymer block contacts the trip switch and the blade stops at a partially open position. From the intermediate open position, energizing or de-energizing the air control solenoids will move the blade either to the full-open position and then later to the closed position or back to the closed position.
The VPO accessory also allows the blade to travel from open to closed (and vice versa) without having to stop at the partially open position; however, the partially open position can only be reached from the closed position. Ideally, the intermediate position should be set between 20 percent open and 20 percent closed. Accuracy and repeatability of the open position setpoint is ± 1/6 of an inch. Multiple setpoints may be added, depending on the air cylinder’s length. Blade position is proofed through a magnetic piston strip in the air cylinder and a magnetic reed switch attached to the cylinder tie-rod.
Variable position closed assembly
The variable position closed (VPC) assembly is another material flow control device and is used in applications when control of where the blade should be positioned during the closing blade stroke is important. This is especially useful when dribble feeding material prior to fully closing the gate is necessary to get as close as possible to a certain material weight. The VPC assembly, as shown in Figure 3, is very similar to the VPO assembly except for the final blade positions. Like the VPO, the VPC allows manual adjustment of the intermediate blade position through the use of air control solenoids and a pneumatic trip switch. A threaded rod attaches to the blade on one end and to a polymer block on the other end. The polymer block moves back and forth within a housing that is attached to the pneumatic cylinder’s side. An adjustable pneumatic trip switch is contained within the housing. During the closing stroke of the blade, the polymer block contacts the trip switch and the blade stops at a partial closed position. From the intermediate closed position, energizing and de-energizing the air control solenoids will move the blade either to the closed position or back to the open position.
This accessory also allows the blade to travel from open to closed (and vice versa) without having to stop at the partially closed position; however, the partially closed position can only be reached from the open position. Ideally, the partially closed position should be set between 20 percent open and 20 percent closed. Accuracy and repeatability of the open position setpoint is ± 1/16 of an inch. Multiple setpoints may be added, depending on the air cylinder’s length. Blade position is proofed through a magnetic piston strip in the air cylinder and a magnetic reed switch attached to the cylinder tie-rod.
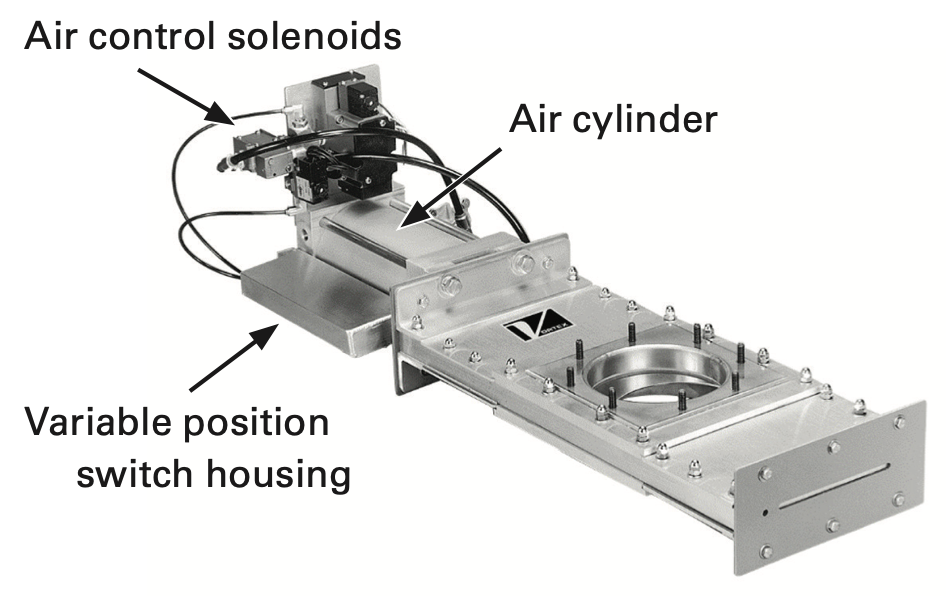
Variable position open-variable position closed assembly
For applications that require control of both the blade’s open and close positions to achieve a dribble feed of material, the variable position open-variable position closed (VPO-VPC) assembly combines the best of the VPO and VPC. The VPO-VPC allows manual adjustment of the intermediate blade position through the use of air control solenoids and a pneumatic trip switch.
A threaded rod attaches to the blade on one end and to a polymer block on the other end. The polymer block moves back and forth within a housing that is attached to the pneumatic cylinder’s side. An adjustable pneumatic trip switch is contained within the housing. The polymer block contacts the appropriate trip switch and the blade stops at the intermediate position. The intermediate position can be reached from either the open or closed position. Air control solenoids can be energized or de-energized to move the blade from the intermediate position to another intermediate position (if chosen), to the closed position, or to the open position.
This accessory also allows the blade to travel from open to closed (and vice versa) without having to stop at an intermediate position. Ideally, the intermediate positions should be set between 20 percent open and 20 percent closed and a minimum of 20 percent between each setpoint. Accuracy and repeatability of the open position setpoint is ± 1/16 of an inch. The gate size and air cylinder length determine how many setpoints will be effective with this option. Blade position is proofed through a magnetic piston strip in the air cylinder and a magnetic reed switch attached to the cylinder tie-rod.
Adjustable variable positioner
An adjustable variable positioner (AVP) is another way to control blade position, and the placement of the magnetic reed switches coincides with where the blade can be positioned. The AVP, as shown in Figure 4, provides automated adjustment of the intermediate blade position through the use of a PLC. Magnetic reed switches mounted to the pneumatic air cylinder’s tie-rod establish each blade setpoint (open, closed, and intermediate points) as well as proofing blade position. The blade can be programmed to travel from any setpoint to any other setpoint. Accuracy and repeatability of the setpoints are ± 3/16 of an inch.
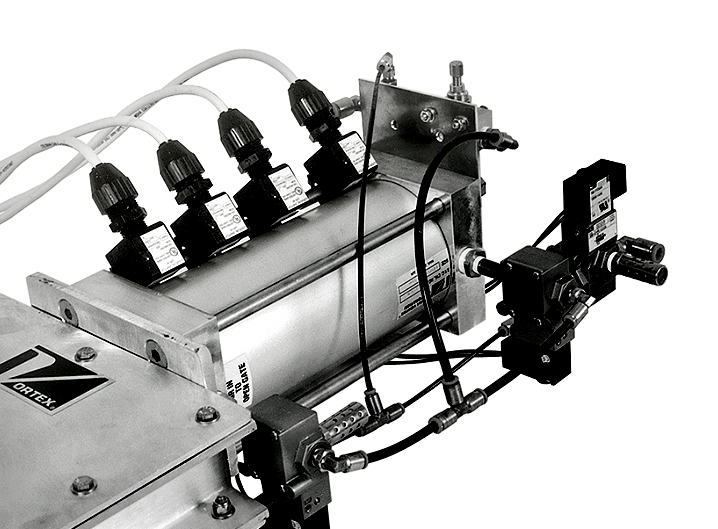
Infinite variable positioner
Like the name suggests, the infinite variable positioner (IVP) provides a wider range of positions where the blade can be set to go. The IVP, as shown in Figure 5, allows for finer control of variable blade positioning. A linear output transducer attached to the air cylinder relays blade position feedback along the entire stroke of the blade. This feedback capacity allows the blade to be moved to any position at any time. The blade is positioned using a remote controller that can be accessed at a nearby mounted control box or automated through a PLC. This option does not require manual adjustment of blade positioning or blade proofing.
Accuracy and repeatability of the blade positioning using the control box, meaning the blade is manually adjusted, is ± 4 percent of the blade’s total stroke. In automated mode, meaning through a PLC, accuracy and repeatability of the blade is ± 2 percent of the blade’s total stroke.
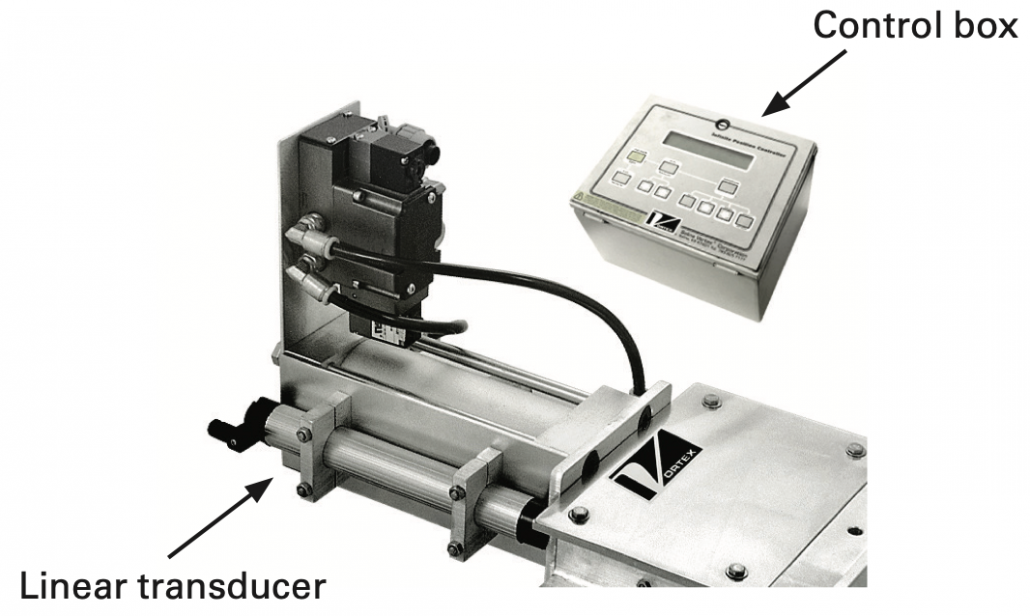
Many dry bulk material handles and processors require some type of material flow control within their system. These control devices vary depending on the characteristics of the material handled and where gate control is placed within a system. These variances explain the need for a variety of position control devices. Slide-gate manufacturing personnel can further assist in deciding what positioner would be best for any application.
About the Author
Kevin R. Peterson is the business development director for Vortex Global. He has written many articles and case studies with industries involved in dry bulk material handling. Kevin serves on the board of directors for the Industrial Minerals Association – North America.