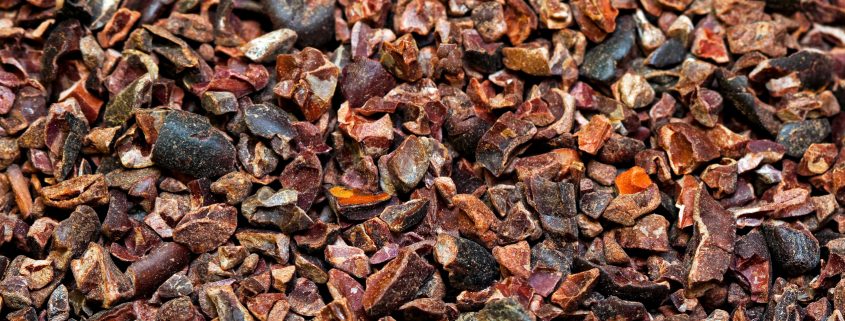
Client:
Quantity:
Size:
Application:
Features:
- Three-way diverting design.
- Diverter body constructed from aluminum.
- Blade, material contact areas, inlet & outlet weldments, and diverter’s housing are constructed from 304 stainless steel.
- Blade is electropolished.
- Pressure plates constructed from PET to accommodate wash-down.
- Flexible hose is twice the standard length. Hose is constructed from FDA-approved rubber and reinforced by a steel wire helix. For added support, the flexible hose is encased by a corrugated cover.
- Diverter features two view ports, each with a removable access door. Both doors are constructed from clear polycarbonate to allow observation into the diverter at all times. The doors are secured by spin knobs to allow internal access without the use of tools.
- Inlet & outlets are configured with schedule 40 pipe stubs to match up with the client’s pre-existing compression couplings.
- Equipped with a KPAN controller. (pictured)
- Rated for continuous service in 180° F (82° C) maximum material temperature.
- Rated for use in vacuum or positive pressure pneumatic conveying applications.
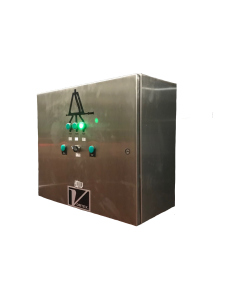
Results:
The flexible hose was made twice the standard length to reduce the degree of bend in the hose when shifted to ports 1 & 3. With the standard hose length, bends in the hose can be significant, which impacts material flow pattern as they pass through the hose. When handling abrasive materials, sharp bends in a standard hose can become wear points, allowing materials to abrade through the hose. However, if hose length is extended, bends in the hose are much more subtle – which creates a more direct path of travel through the hose and lessens the degree of wear.
Both view ports were specifically sized for ease of maintenance. The smaller view port was sized so that connection couplings can be removed, and the larger view port was sized so that the flexible hose can be removed for maintenance or replacement. Each door is secured by spin knobs to allow quick and easy access to the diverter’s housing without using tools. These processes can be performed while the diverter remains in-line – and without significantly disassembling the housing.
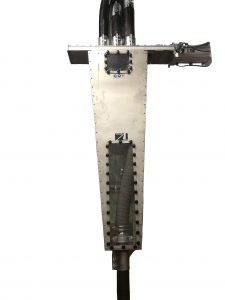