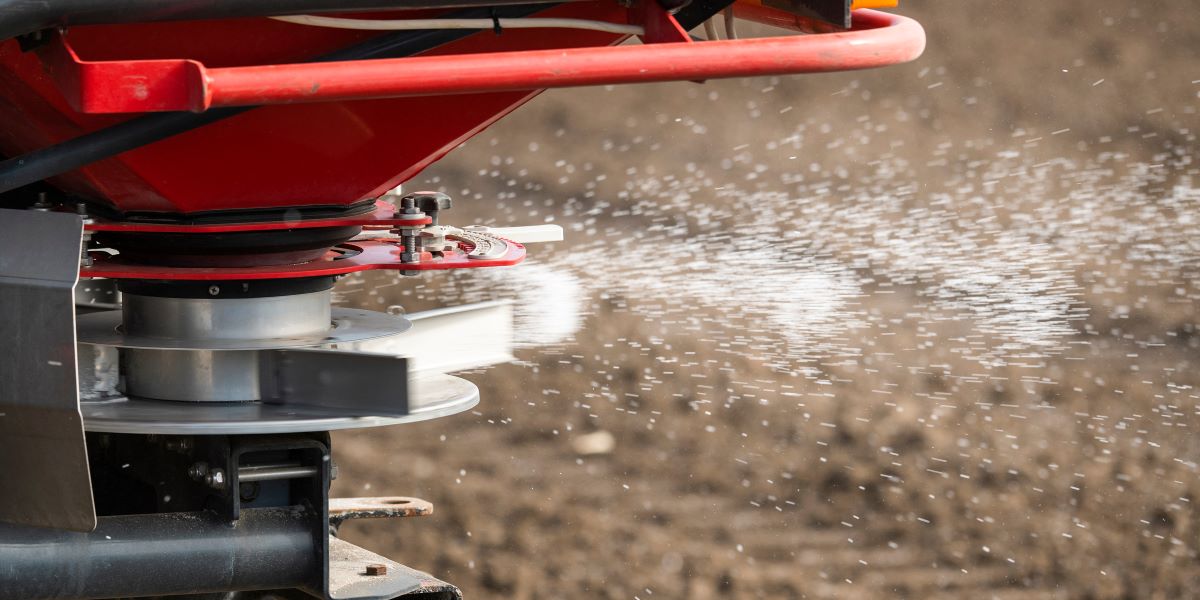
Client:
Quantity:
Size:
Application:
Fertilization has been a key component of growing healthy plants and crops for centuries. While early fertilizers were derived from natural and organic resources (i.e. compost, manure and minerals) the 19th century brought about a revolution in the fertilizer industry and the introduction of synthetic fertilizers featuring a variety of chemicals.
Many of the ingredients and chemical compounds used in the production of fertilizer require the need for special consideration when selecting the components to be used in its manufacturing. These compounds can have a plethora of reactive effects on the materials of construction and can cause dusting to the atmosphere if proper dust-tight components are not sourced.
The emission of dusts into the atmosphere during the production of fertilizer can have a variety of negative effects on nearby communities and ecosystems. As government regulations on dust control tighten, manufacturers of products such as fertilizer face tighter restrictions. Corrosive materials often used to make fertilizer can also wreak havoc on the equipment used in its production. These concerns have led to the evolution of dry bulk handling components that are manufactured to specifically address these concerns.
Among the many ingredients commonly used in the development of fertilizer are sulphur, potassium sulfate and urea. These ingredients and finished fertilizer all have unique traits that require specific attention when designing manufacturing systems. Sulphur can often times have a corrosive reaction with mild steel, therefore 316 stainless steel is recommended to withstand the material being handled. The salt content within potassium sulfate can also cause damage to and corrode materials. Urea can have a variety of reactions with certain materials of construction. The loadout of finished fertilizer can be a dusty endeavor, making a dust control system necessary.
Dust Control in Fertilizer Manufacturing
Material dusting and leakage is a problem for manufacturing plants and factories around the world. Manufacturers of fertilizer face dusting concerns when handling various ingredients, as well as finished fertilizer, in their processes. The hazards generated by dust include health and safety concerns, risk of explosion, material waste and loss of profit, and the pollution of nearby neighborhoods and ecosystems.
As environmental regulations strengthen, facilities have faced tighter restrictions to keep their employees and neighbors safe. Negative effects of dust leakage and exposure include allergic reactions and skin irritation, irritation of the lungs due to inhalation of potentially toxic chemicals, and the accumulation of dust on surfaces leading to falls. In some cases, fugitive dusts can accumulate to form a cloud that can ignite, burn and potentially explode.
Dust-tight valves and loading spouts equipped with dust collection systems can help facilities mitigate the detrimental effects of dusting. Dust travels through the path of least resistance. This can be a challenge when using soft polymers and packing as seals. Dust-tight valves designed today feature hard polymers as a sealing surface, due to better wear characteristics for most applications. It is crucial to verify that connections between the valve and equipment above and below are tight. A good seal on every connection is critical to minimizing the escape of dust from your equipment.
When loading dry bulk materials, properly equipped loading spouts can eliminate fugitive dusts. Throughout the loading process, displaced air and dust can aspirate out of the enclosed vessel via the spout's filtration system. A reverse pulse jet allows the air-dust mixture to be continuously filtered and reintroduced into material flow. This creates a completely closed loading cycle, which prevents dust emissions and minimizes material loss.
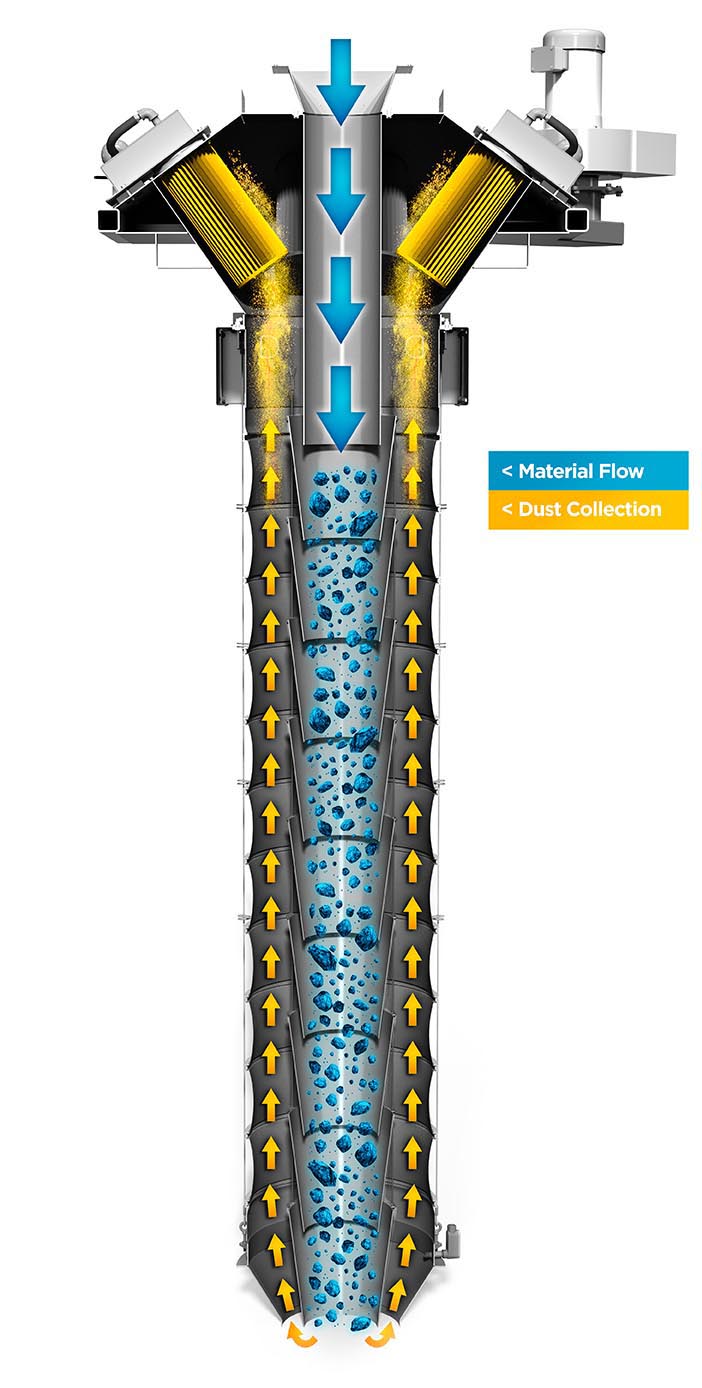
Vortex and Dust Control
Vortex slide gates, diverter valves and loading spouts are specifically designed to address dusting concerns and material leakage. Facilities have an obligation to protect against the hazards of manufacturing. Vortex closely monitors trends in air quality, environmental dust emissions, workplace safety and evolving regulations to develop its components to comply and address these concerns.
Over the past four decades, Vortex has provided dust-free solutions to customers in the chemical and fertilizer industries where dusting and material leakage is a concern. While each application has its unique challenges when it comes to dust, the principles used to develop Vortex products can be applied in a variety of applications.
Case study: Loading Spout Handling Fertilizer
A fertilizer supplier sourced a Vortex Loading Spout (also referred to as loading chute) to handle fertilizers in their production process. The loading spout is being used at a barge transload facility to convey finished fertilizers.
The in-line filtration system is designed to collect fugitive dusts by means of air withdrawal. This system is designed to minimize product loss and to prevent dusting.
The in-line filtration system is designed to collect fugitive dusts by means of air withdrawal. This system is designed to minimize product loss and to prevent dusting.
Size and Weight:
Diameter: 355 mm (14”)
Travel Distance: 3.66 m (12’)
Volumetric Flow Rate: 250 CFM
Features:
This specific Vortex Loading Spout is intended for enclosed loading and features a four-cable lifting design with CNC-machined pulleys to reduce cable wear and backlashing. The Vortex In-Line Filtration System installed above the spout features pulse jets above each filter. The pulse jets continuously purge the filters so that accumulated dusts are routed back down through the spout and into the loading vessel below. This process improves operations by allowing material dusts to be loaded as product, rather than being transferred as waste to a dust collection system.
Handling Corrosive Materials
This Vortex retractable loading spout is being used at a barge transload facility to convey finished fertilizer.
This Vortex retractable loading spout is being used at a barge transload facility to convey finished fertilizer.
Case study: Seal Tite Diverter Handling Urea
A Russian fertilizer producer contacted Vortex to assist in their process. This Vortex Seal Tite Diverter is manufactured of 304 stainless steel with EDPM elastomer seals due to the reactive effects urea has with other materials of construction.
This Vortex Seal Tite Diverter is manufactured of 304 stainless steel with EDPM elastomer seals due to the reactive effects of urea.
This Vortex Seal Tite Diverter is manufactured of 304 stainless steel with EDPM elastomer seals due to the reactive effects of urea.
Size and Weight:
850 mm (33.5”) – 1088 kg (2400 lbs)
Features:
The Vortex Seal Tite Diverter is used in gravity flow applications where dry bulk solid materials must be diverted from one source toward up to three destinations. This diverter’s side access panel allows for internal inspection or maintenance without having to remove the diverter from place. Additionally, the diverter is designed with recessed areas that shield the leading edge of the blade from the material flow stream prolonging the diverter’s sealing ability.
Case study: Pivoting Chute Diverter Handling Potassium Sulfate
A minerals processor in the United States sourced the Vortex Pivoting Chute Diverter to handle potassium sulfate, a chemical compound commonly found in fertilizer.
Size and Weight:
254 mm x 1143 mm (10” x 45”) – 470 kg (1035 lbs)
Features:
These Vortex Pivoting Chute Diverters were manufactured out of 316L stainless steel.
These Vortex Pivoting Chute Diverters were manufactured out of 316L stainless steel.
Case study: Titan Slide Gate Handling Sulphur Pellets
This hydraulically actuated Vortex Titan Slide Gate is used by a fertilizer supplier to handle sulphur pellets. The gate is constructed of 316 stainless steel due to the corrosive reaction that the material handled exhibits with mild steel.
This hydraulically actuated Vortex Titan Slide Gate is constructed of 316 stainless steel due to the corrosive nature of the material being handled.
This hydraulically actuated Vortex Titan Slide Gate is constructed of 316 stainless steel due to the corrosive nature of the material being handled.
Size and Weight:
.6 m x 1.6 m (23.5” x 65.5”) – 907 kg (2000 lbs)
Features:
The Vortex Titan Slide Gate is ideal for handling heavy-duty aggregates and abrasive materials in installations above or below gravity-fed hoppers/silos, mixers, and augers/screw conveyors. This specific gate is installed beneath a storage hopper and is used to shut off material or allow material to be discharged onto a conveyor belt. The front displacement pocket minimizes jamming and packing of material that could prematurely wear out the end seal. It is a standard feature for this gate that will occasionally be closing on material.
For over 40 years, Vortex Global has provided quality slide gates, diverters, iris valves and loadout equipment designed specifically for handling dry bulk solids in gravity, vacuum, dilute, or dense phase applications. Vortex equipment is engineered for dependability, durability, easy maintenance, and offers proven solutions to material handling and process efficiency problems. With an in-house team of engineers, Vortex products can be completely customized for individual applications or special installations. For more information, visit www.vortexglobal.com.