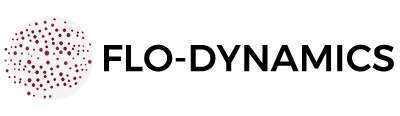
Client:
Quantity:
Size:
Application:
Background
For 18 years, Vortex and Flo-Dynamics Components, Inc. have nurtured a long-standing customer relationship with an East Coast, USA-based chemical supplier. In that time, Flo-Dynamics Components, Inc. has worked directly with the client’s Maintenance & Engineering teams to provide Vortex products and replacement parts.
Historically, this chemical supplier has sourced many customer-specified Vortex Orifice Gates. They have enjoyed the Orifice Gate’s long service life, and have found the gates are reliable when handling the large list of chemicals processed each day in their facility.
The Problem
Recently, the chemical supplier has experienced many changes. Of them, a new production manager has taken the helm and – more importantly – a revised list of chemicals to be processed in their daily operations. With several new chemicals being introduced into the process, the client was concerned about the Orifice Gate’s ability to continue operating properly.
The Solution
To alleviate the situation, the client and Flo-Dynamics Components, Inc. consulted Vortex’s Engineering and Customer Service Departments to discuss their concerns. Vortex assured that if the client continues to source Orifice Gates as previously specified, the gates will continue to work well in their chemical process for years to come.
The client’s specifications include:
- Gate Size: 8 in | 205 mm
- Features:
~Valve body, blade & material contact areas constructed from 304 stainless steel.
~Pressure plates constructed from nylon & “live loaded” with non-porous acetal copolymer.
~Equipped with a Special Service Inlet.
Because of the chemicals’ unique properties, non-porous acetal copolymer load seals were specified instead of the standard load seals constructed from compressed rubber backing. 304 stainless steel materials of construction were also sourced to protect the gate from its corrosive environment.
By design, a Special Service Inlet acts as a funnel to direct material flow through the center of the gate. The primary purpose of a Special Service Inlet is to create a void between materials, the blade, and the gate’s seals. In this client’s application, a Special Service Inlet was specified to hinder chemicals from migrating into the gate’s seals and causing damage.
Results
This project is a true testament to the strong, personalized relationships Flo-Dynamics Components, Inc. and Vortex strive to provide their clients, in order to cultivate positive, long-standing relationships.