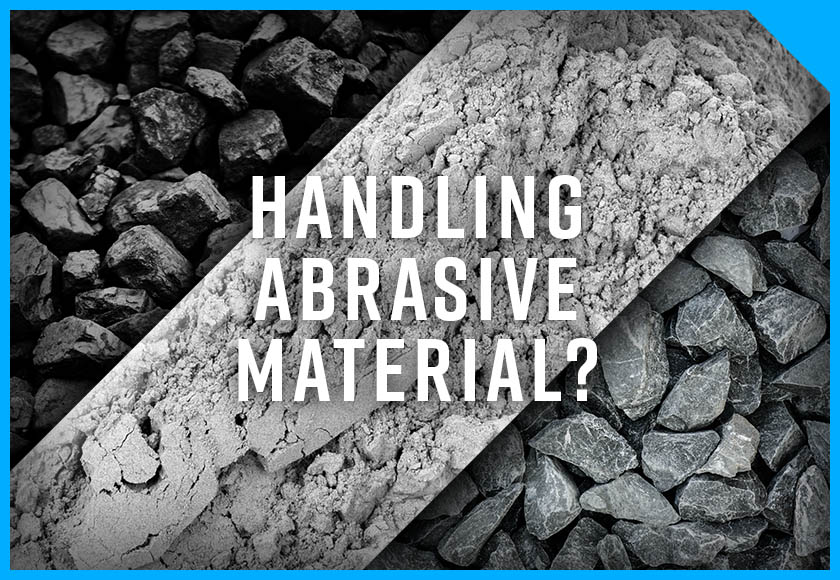
Client:
Quantity:
Size:
Application:
Many Vortex customers come from industries where conveying abrasive material is a recurring challenge. Configuring the appropriate slide gates and diverter valves for those customers is a challenge in its own right. In this article, we’ll analyze the key factors that influence the decision of which slide gate or diverter valve works best for handling abrasive materials.
Different Levels of Material Hardness Cause Different Levels of Wear
Abrasion occurs where the metal components of a valve are worn down by friction as handled materials impact those areas. Prior to assessing what type of gate or diverter is most appropriate for the application, special consideration must be given to material characteristics and how the material is being conveyed.
Minerals are categorized by a Mohs hardness scale. The scale characterizes the scratch resistance of various minerals by observing how easily a harder material can scratch a softer material. Softer materials, such as talc, have a Mohs hardness rating of 1, while harder materials, such as diamonds, have a Mohs hardness rating of 10. When selecting metal valve components, it’s important to select the proper construction materials that can resist the hardness and wear of the material handled.
Material Shape Has an Impact on the Effects of Abrasion
The shape of the material being handled is another important consideration. Sand can have a Mohs hardness rating of 7, and exists in a variety of shapes. Some sand particles can be round, while others can be angular. An angular particle will abrade valve components much faster than a rounded one.
How the material is handled is yet another consideration. For example, is the material being gravity-fed through the valve, or is the material being conveyed pneumatically through a system at 3,000 feet per minute? Talc, one of the softest minerals, can eventually chisel its way through a substantial metal plate if given a small exit hole and considerable force behind it.
Hard Metal Wear Liners can Alleviate Component Breakdown
Utilizing hard metals or metal alloys for the wear areas is always a consideration. Valves may be manufactured to incorporate abrasion resistant plates, chromium carbide overlays, or metals like Hastelloy® to reduce wear from material abrasion. Diverters may also be manufactured with replaceable wear liners, typically constructed from the above-mentioned materials.
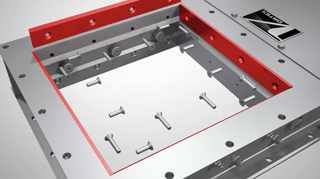
Over time, worn liners may be replaced with new ones. This extends a valve's life cycle and reduces costs by allowing replacement of parts, rather than full-valve replacement. In certain applications, an additional valve feature as simple as an interior rock box may be added to address abrasion and prolong valve life. A rock box is an area within the valve designed to trap small amounts of material while subsequent material traveling through the valve impacts atop the trapped material, as opposed to abrading a liner or plate. When material cross-contamination is not of concern, this feature is extremely effective.
Manufacturing Experience with Abrasives is Critical
Companies that deal with abrasive products are cognizant of the fact that new equipment begins to wear quickly, starting day one. Equipment installed in these environments must be continuously maintained. Sourcing valves from an established supplier with the ability to provide support after installation can help alleviate the burden of dealing with challenging applications. Supplier expertise can address the many challenging factors experienced in unique applications, and can assure your company is purchasing the best slide gate or diverter valve available for handling abrasive materials.