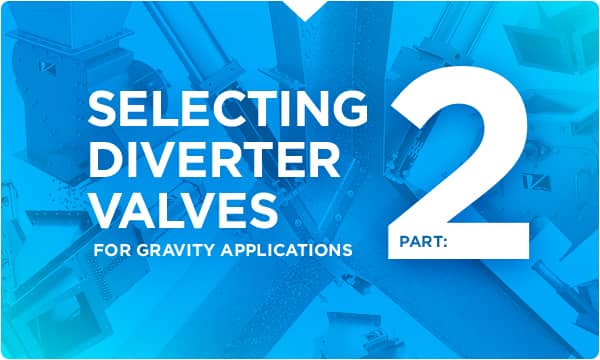
Client:
Quantity:
Size:
Application:
When you browse through Vortex’s product catalogue, you may notice a wide variety of standard and engineered diverters for gravity flow applications. This is not by accident or due to the fact that we love to design multiple products that achieve the same result! This article covers the differences between multiple diverters and address factors that impact selection, based on application.
To be clear about the term “gravity flow," Vortex defines it as an application where air pressure or vacuum is not used to assist material conveyance. The primary factor that drives the selection of a gravity diverter is the particle size and/or abrasiveness of the material handled. Another driving factor is the bore size of the valve required.
Vortex manufactures six types of diverters that are suitable for handling material in gravity flow:
- Seal Tite Diverter
- Gravity Vee Diverter
- Flex Tube Diverter
- Aggregate Diverter
- Titan Lined Diverter
- Pivoting Chute Diverter
As a continuation of a three part series, this article will cover the Flex Tube and Aggregate Diverters.
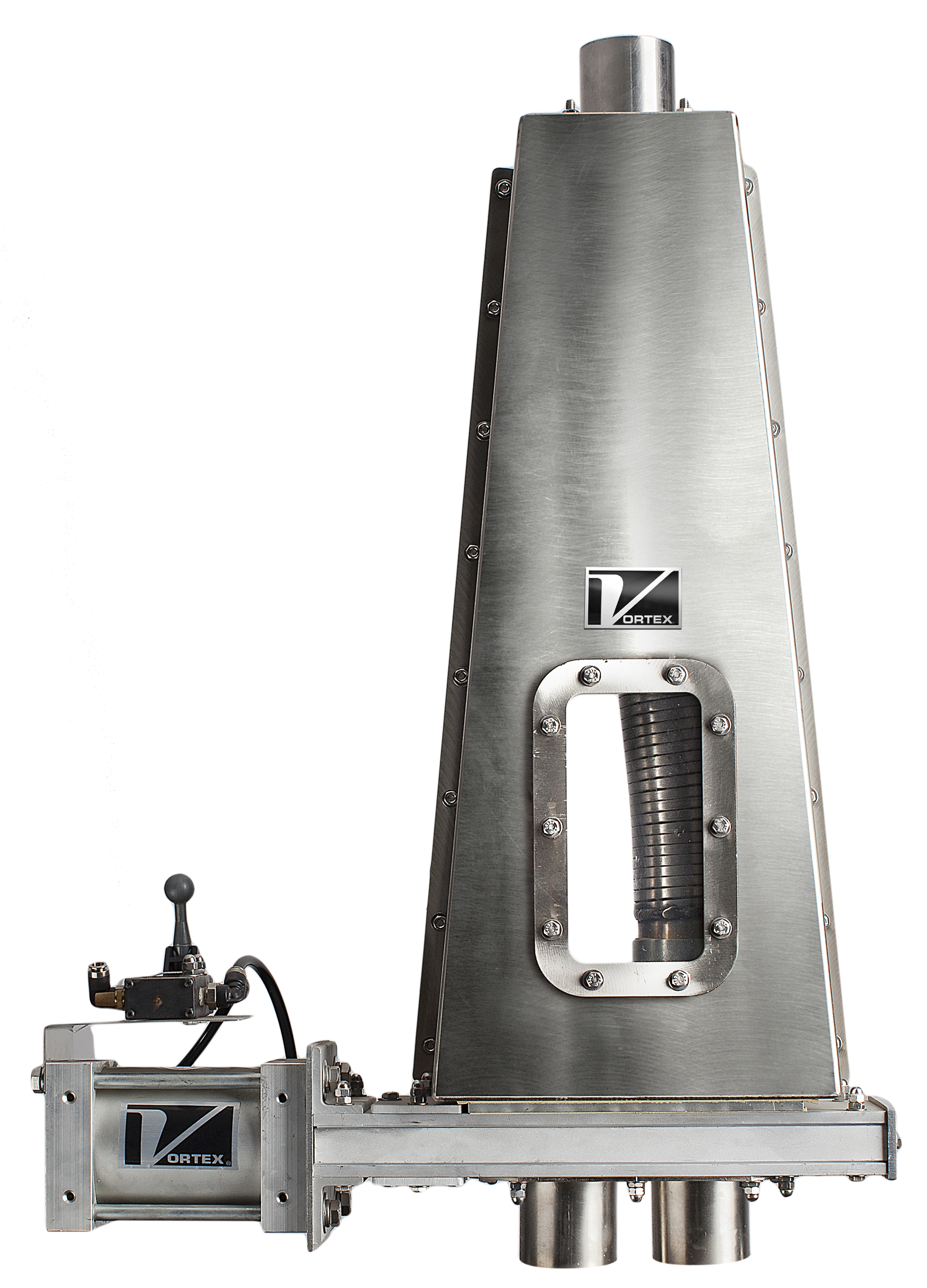
Flex Tube Diverter
The Flex Tube Diverter was designed for diverting most dry powders, pellets, and granules in low pressure/high velocity pneumatic conveying systems. From a gravity flow perspective, it can be an excellent option for applications with less than 100 mm | 4 in bore sizes.
The Vortex Flex Tube Diverter is available in two and three-way configurations, as well as, having the capability to go from two or three sources to one destination.
The unobstructed flexible tube shifts from one port to the other, eliminating dead pockets and the potential of cross contamination between conveyed materials. The flexible tube reduces any abrupt bends and potential impact points, making it a preferred diverter for handling friable products such as whole coffee beans or nuts.
One of the main features of the Flex Tube Diverter is the maintenance friendly design. If the diverter shows signs of light dusting, the diverter’s removable shims allow it to be easily maintained inline. While remaining in service, simply loosen the bolts along each side of the unit and remove a shim. After re-tightening the bolts, the diverter will seal as if it was new again. This process significantly extends the life of the valve and reduces your downtime.
Though it may not be practical for gravity flow applications in larger sizes, Vortex’s standard range does up to 250 mm | 10 in.
Aggregate Diverter
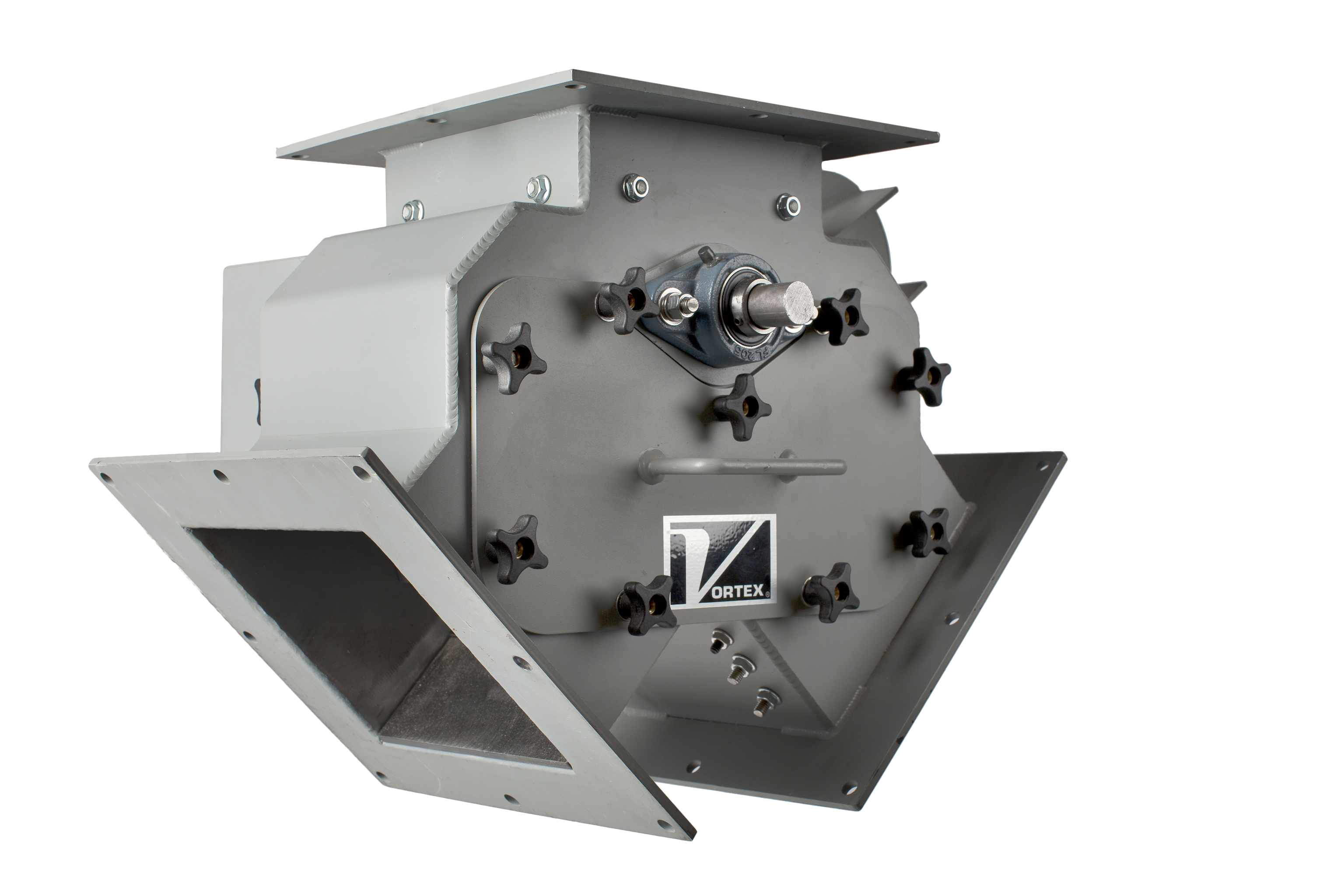
The Vortex Aggregate Diverter was originally designed in the early 2000s for a ready-mix cement application, where a common “bucket-type” diverter failed frequently due to high abrasion. In order to prevent wear and extend service life, Vortex incorporated several key design features:
- Dead pocket deflector – minimizes wear through the inlet.
- “Honeycomb” bucket and leg liners – applied in extremely abrasive applications where cross-contamination of material is not an issue.
- Durable rubber bucket seals – placed out of the path of the material flow stream. This standard feature aids in sealing material across the closed bucket chute.
- Removable access panel – facilitates diverter inspection or maintenance.
The design has proven to be a success by extending the service life from a few months to several years with little to no maintenance. Today the Aggregate Diverter is applied in many types of applications, including industrial sands, coal, recycled glass, and other abrasive materials.
Standard sizes of the Aggregate Diverter range from 150 mm | 6 in to 600 mm | 24 in. Custom sizes above 600 mm | 24 in may be prohibitive due to weight and actuation limitations. In such cases, the Titan Lined Diverter featured in the next article of this series might be more suitable.