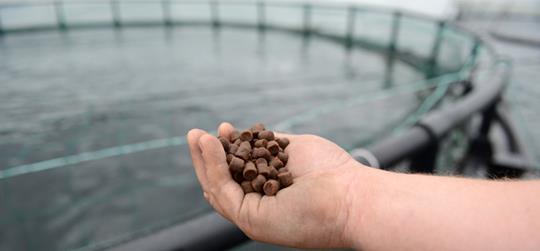
Client:
Quantity:
Size:
Application:
Client:
BioMar’s extrusion technology produces a wide range of feed pellets with unique technical qualities. The company is a world leader in high performance diets for more than 45 different fish and shrimp species in more than 80 countries. Founded in 1962 by a group of Danish fish farmers, BioMar’s heritage is a long-term commitment to developing the aquaculture industry in a responsible and sustainable way.
BioMar’s main focus is supporting their customers by delivering healthy, great tasting seafood. BioMar does this by innovating efficient, safe and nutritious feed for aquaculture with minimal environmental impact. Their global scale, local agility and execution focus ensures that they can meet individual customer needs – always with departure in proven results with a meticulous focus on food safety.
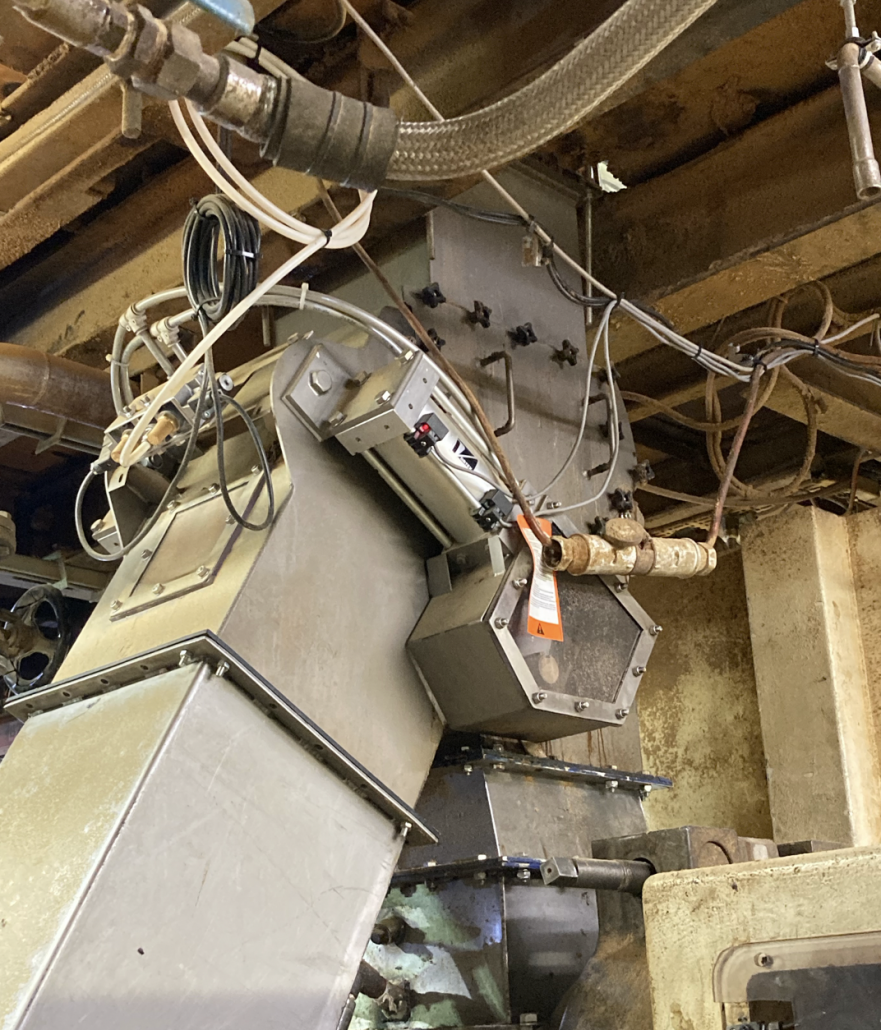
Application:
This client’s manufacturing process mills include bulk storage, bulk material discharge and transfer of raw material for aquaculture pellet feed production.
Challenges:
The client had a need to replace a flap type diverter valve which had been in service for a considerable period of time. The existing diverter valve had reached the end of its service life and was difficult to clean and maintain due to its design.
The new diverter design stipulated by the client had to cope with various granular and powdered materials, varying in their nature which could include variable bulk densities, particle size, abrasive and sticky feed materials. Focus was placed on durability, security to avoid leakage and have a maintenance friendly design that ensured access for cleaning and maintenance activities.
Results:
The Vortex Seal Tite Diverter was identified as the ideal replacement. The Seal Tite Diverter is designed to handle fine materials in gravity flow applications, providing positive material shut off and dust tight sealing capabilities.
The client specifically liked the twin access panels, which not only allows access for inspection and cleaning, but allows for the internal parts of the diverter to be removed and replaced, which means the diverter valve can be maintained in situ, minimizing plant downtime.
The valve was also complete with twin pneumatic cylinder controls to provide additional torque to overcome potentially sticky material with a high moisture content.
The valve was designed with seals to handle material temperature of 90°C and manufactured to have the same dimensions as the existing diverters to allow ease of replacement.
Features:
- Twin quick release access panels allowing quick access to the interior of the diverter for inspection, cleaning or maintenance purposes.
- Vision windows on discharge legs.
- Designed to channel material flow from the leading edge of the internal flap, preventing leakage and material cross contamination.
- Live loaded wear compensating seal under the shaft, minimizing material leakage down the closed leg.
- Full 316 stainless steel construction, polished internally.
- Bespoke design matching the dimensions of the existing valve for ease of installation.