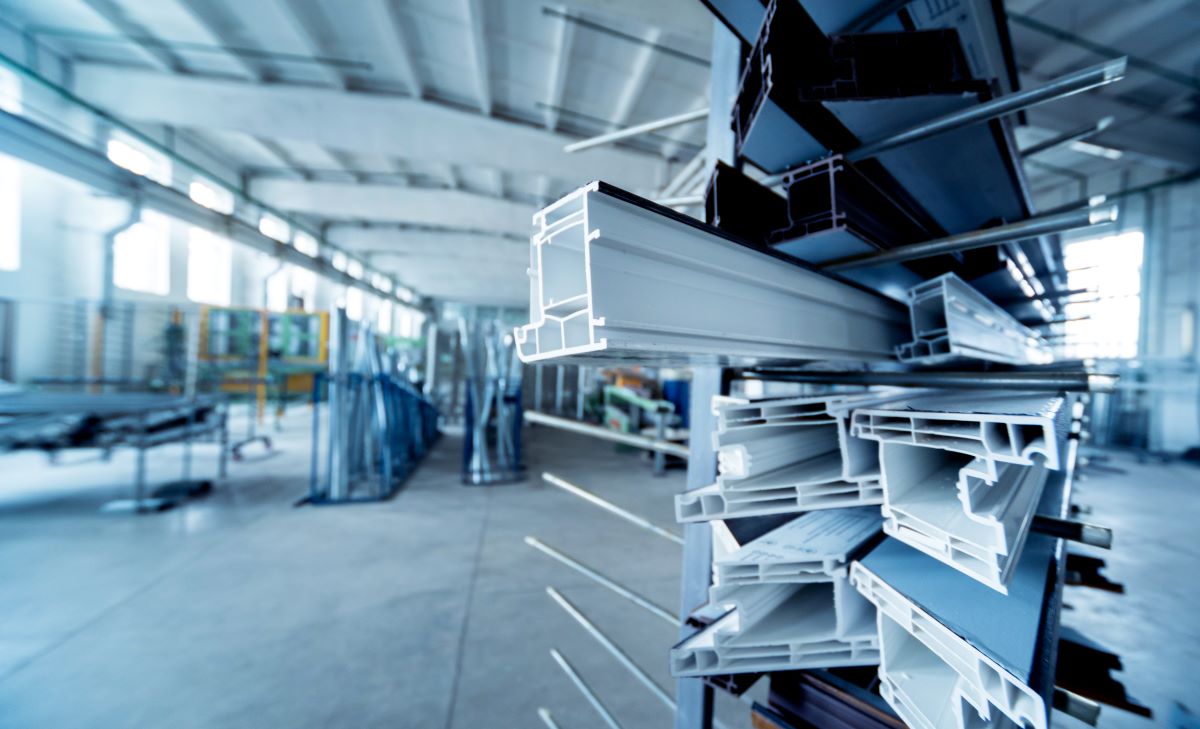
Client:
Quantity:
Size:
Application:
This customer specializes in manufacturing PVC window and door system profiles. They use Polyvinyl Chloride (PVC) in their manufacturing process, a versatile plastic with a wide range of applications. In the production process, this customer utilizes PVC powder to create high-quality products. PVC material is used in the extrusion process. In this process, the PVC powder - often mixed with other materials to achieve desired properties - is heated and forced through a die to form the shape of the profile. This method allows them to produce a variety of different shapes and sizes of profiles, making it possible to cater to a wide range of customer needs. This customer also pays attention to the environmental impact of their operations. They have a PVC recycling process in place, where they separate metals from the material and sort them into the correct color groups. This allows them to reuse PVC, reducing waste and contributing to sustainability.
PVC powder, while a highly useful material in manufacturing processes, can be abrasive due to its physical and chemical properties. This abrasiveness refers to the property of a material to wear down another material when rubbed against it. The hardness and grainy texture of PVC powder contribute to its abrasive nature. The abrasiveness of PVC powder can present several challenges during handling and processing. It can cause wear and tear on machinery and equipment, reducing their lifespan and increasing maintenance costs. This is particularly true for diverters that are not designed to handle abrasive materials.
Vortex Global provides several abrasion resistance options for the Vortex® Wye Line Diverter™ as well as many other equipment models. For additional insights into abrasion resistance you can read more here.
In this application, Ceramic Backing was chosen as the preferred choice for providing the longest service life possible for these Wye Line Diverters. Ceramic wrappings play a crucial role in pneumatic conveying applications, providing protection to the Wye Line Diverters against wear and abrasion typical in dilute phase material conveyance. The ceramic backing serves to safeguard a diverter’s inlet weldment from substantial wear caused by material flow, ensuring continuous operation by retaining conveying line pressure and preventing leakage. This strategic use of ceramic backing enables the diverter to function effectively amidst abrasive conditions, eliminating the need for frequent component replacements.
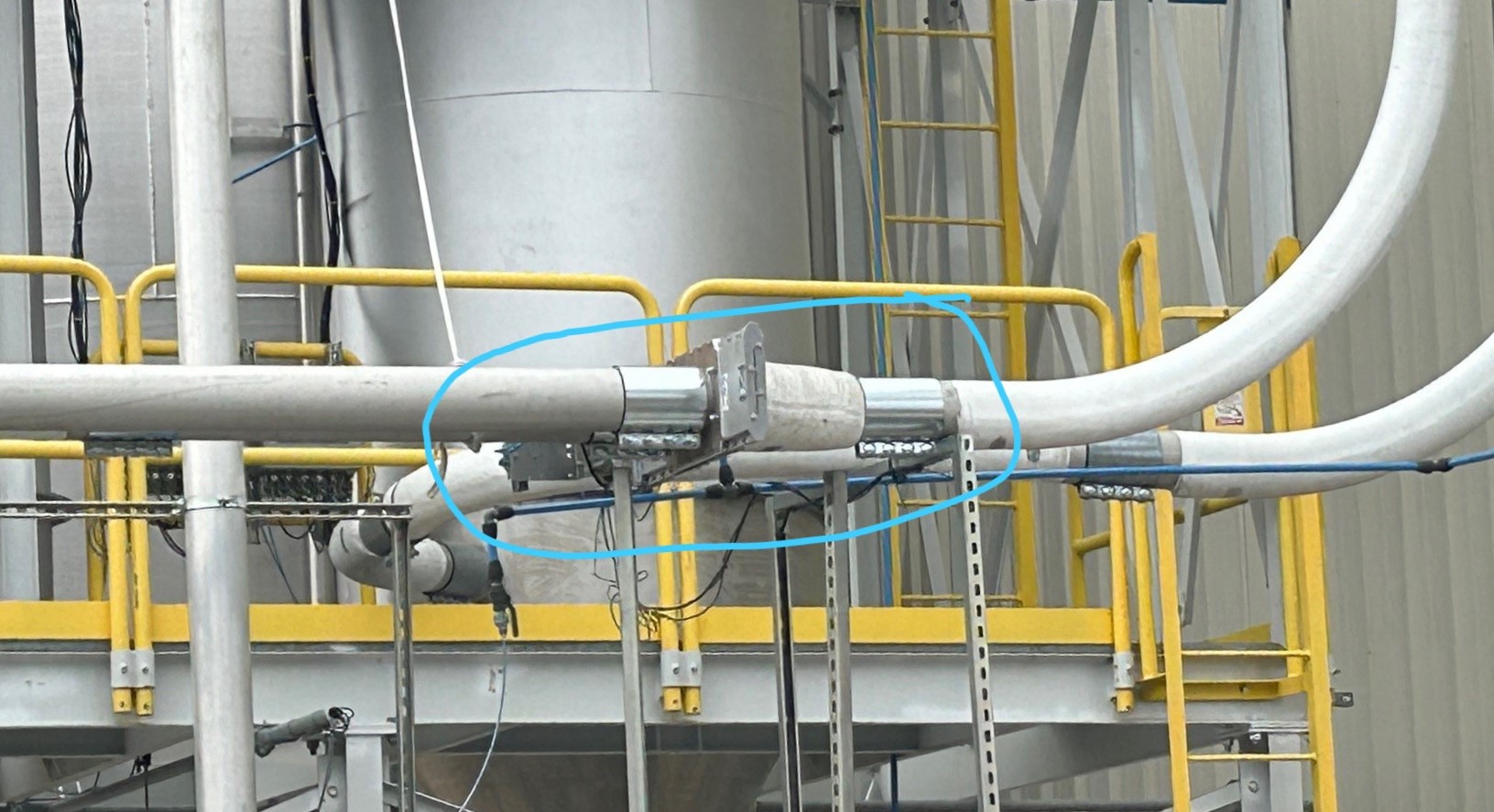
The necessity for ceramic backing varies based on specific applications, as materials can react differently to system configurations and air pressure despite similar handling characteristics. The application of ceramic coatings requires precision to maintain smooth surfaces that align with material flow direction, reducing turbulence and friction that could damage the material or accelerate ceramic wear. On average, ceramic coatings can extend the durability of steel components by 30-40%, enhancing their service life significantly. This makes them a cost-effective solution for companies looking to increase the longevity of their equipment and reduce maintenance costs. Your Vortex Global Sales Application Specialist will be able to advise you on the appropriate measures required for you specific application. Contact us today!