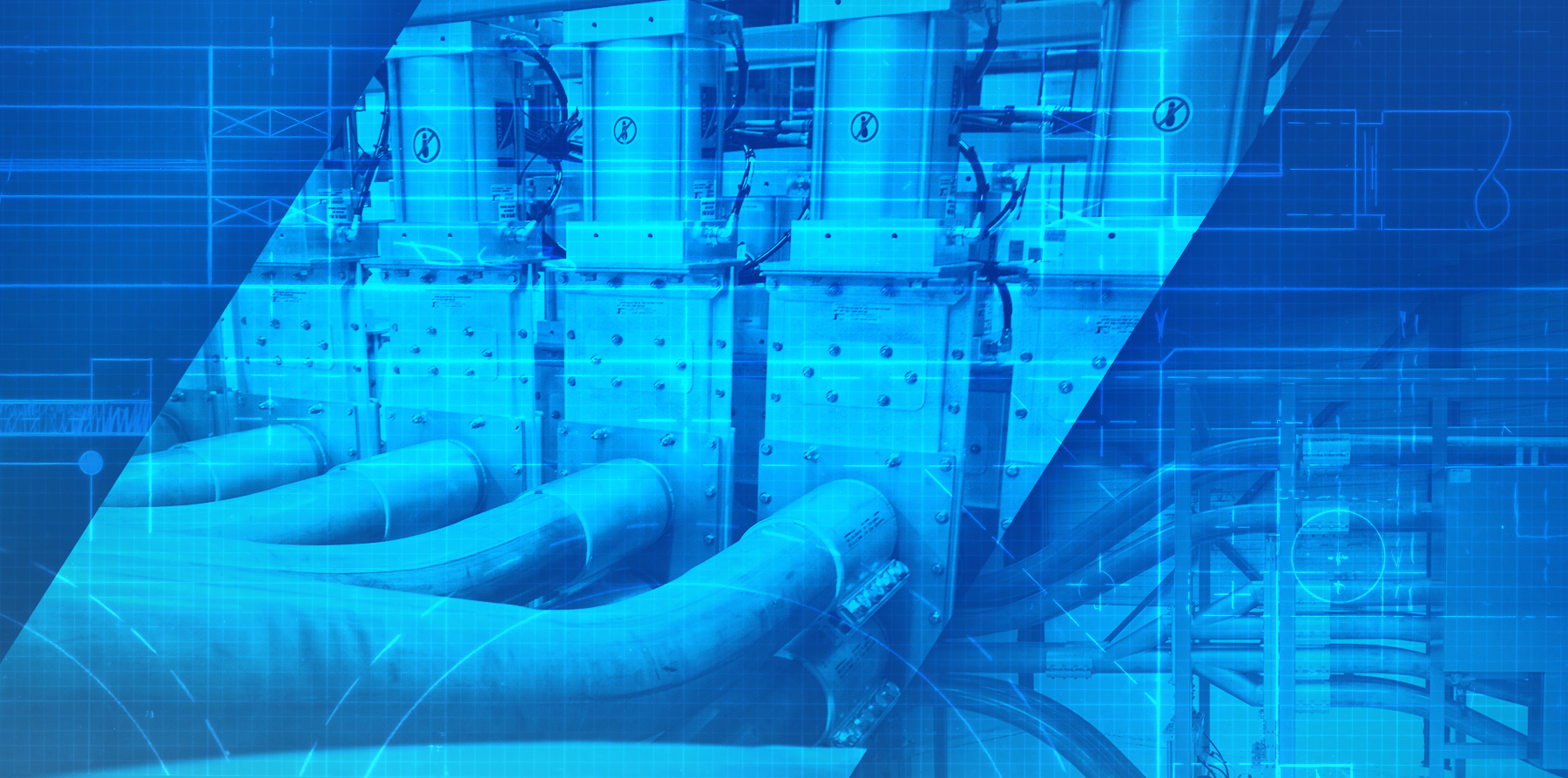
Client:
Quantity:
Size:
Application:
What it is
A Multi-Port Diverter is an integrated and automated solution for diverting and/or converging dry solid materials. Depending on the application, a multi-port diverter can be designed to transport materials from a single source or several sources toward any number of destinations.
Why it is used
Multi-port diverters are more often used to replace manual hose manifold stations. Because multi-port diverters are automated for PLC control, they solve many issues that exist with manual hose manifold stations. Because hoses are heavy and repositioning them is a manual process, this creates risk for employee injury and other safety concerns. Also, if source hoses are reconnected to channel toward incorrect destinations, product contaminations and bad batches will result. In many cases, the costs associated with one wasted batch have been more expensive than the acquisition cost of a multi-port diverter. By automating the process with a multi-port diverter, the risk of making process errors is reduced.
Because they are compact units, multi-port diverters are also used to add production capacity while minimizing a system’s overall footprint. Depending on application, a multi-port diverter can be installed either vertically or horizontally. Common installation examples include on a rooftop or mounted along a wall. Because multi-port diverters allow for better utilization of vertical space, in many cases, facilities have improved their production capacities by more than 30 percent.
Vortex Multi-Port Diverters
Among its many equipment offerings, Vortex also designs and manufactures Multi-Port Diverters. Because each unit is made-to-order for a customer’s specific application, standard sizes and configurations are not available. Worldwide, Vortex works closely with systems groups and engineering firms to design Multi-Port Diverters and other complex diverting/converging configurations that fulfill every requirement of a client’s unique application.
Materials Handled
Vortex Multi-Port Diverters are used to handle a variety of non-abrasive to moderately abrasive powders, pellets and granules. Common examples include silica, phenolic resin, flour, alumina and plastic pellets, among others. Multi-Port Diverters are commonly used in the agriculture, chemical, food & beverage, minerals, petrochemicals, plastics and textile industries.
Generally, Vortex Multi-Port Diverters are used to handle material temperatures no greater than 180°F | 82°C, though modifications can be made to handle material temperatures up to 400°F | 204°C.
Unique Design Features
- Low maintenance requirement As previously stated, multi-port diverters incorporate a series of pneumatic diverters. In Vortex’s case, a Multi-Port Diverter is comprised of several Vortex Wye Line Diverters. Each Wye Line Diverter features a sliding blade sandwiched between two live-loaded, wear-compensating hard polymer seal plates. With this design, materials are prevented from migrating into the body of the valve – which could otherwise cause actuation issues. Also, rather than closing into a true end seal, each Wye Line Diverter is designed to actuate into a recessed area on the closing stroke. In doing so, a small amount of materials are temporarily displaced in the recessed area. The Wye Line Diverter is designed to “self-clean” on the opening stroke, so that displaced materials are pulled back out of the recessed area before falling away into the process line below. Because the blade actuates into a recessed area instead of packing materials into an end seal, there is less risk for binding and other actuation issues. Because the Multi-Port Diverter is designed with Wye Line Diverters to eliminate the above concerns, maintenance requirements are reduced. When maintenance does become necessary, each Wye Line Diverter is designed with weep holes at the front of the valve. If for some reason the valve’s dust-tight seal has been compromised, slight dusting will occur through those weep holes to indicate a maintenance need. For ease of maintenance, each Wye Line Diverter is equipped with shims. By simply loosening the nuts along the lateral aspects of the valve, shims can be removed. Once the nuts are retightened, the valve’s dust-tight seal is restored. This maintenance process can be completed in approximately ten minutes – and can be performed while the valve remains in-line.
- Can be shifted “on the fly.” The Vortex Multi-Port Diverter is designed so that it can be shifted “on the fly” – and can do so through a moving column of material. If the same material is being conveyed from one source toward several destinations, this allows for improved processing speeds by continuously flowing materials. However, if different materials are being conveyed from a common source toward separate destinations, to prevent bad batches, it’s advised to purge the line before shifting the blade toward a new destination.
- Unobstructed opening. Allows material flow rates and convey line pressures to be maintained. Because each valve’s blade and seals are recessed from the material flow stream, wear is minimized – which further reduces maintenance requirements.
Additional Considerations
- Application limitations. Multi-port diverters can only be used in vacuum or dilute phase pneumatic conveying applications up to 15 psig | 1 barg, depending on convey line size.
Economic Advantages of Multi-Port Diverters
- Cost-effective. Vacuum and dilute phase pneumatic conveying are among the most cost-effective methods for conveying dry bulk solid materials. Also, by replacing a manual hose manifold process with an automated multi-port diverting system, this reduces labor costs by freeing up operators’ time so that they can perform other tasks at-hand.
- Eliminates human error. Because manual hose manifold stations have been replaced by automation, the risk for process errors is reduced. With that, there is less risk for bad batches or rework, which makes for a more efficient use of raw materials.
- Increased capacities. Because multi-port diverters allow for more efficient use of manufacturing space, more sources and destinations can be established – and with that, manufacturing capacities can be increased. When coupled with automation and the elimination of human error, this paints a picture of increased capacities, increased processing speeds, consistency and reliability. Their common denominator? Improved profitability and performance.
Safety & Environmental Advantages of Multi-Port Diverters
- Addresses operator health & safety concerns. The Vortex Multi-Port Diverter is specifically designed to provide a positive seal of air and materials across the gate and to atmosphere. This is also an economic advantage because it prevents waste of resources, such as material loss or air loss. For housekeeping purposes, the Vortex Multi-Port Diverter’s dust-tight design is advantageous because it prevents materials and dusts from accumulating throughout the production facility. Otherwise, serious employee health and safety concerns may result, such as slip hazards, explosion potential, or medical conditions such as silicosis. These health and safety issues will trickle down to human resources and result in expensive short- and long-term disabilities. When employees are injured or unhealthy, the response is either short-staffing or re-staffing on the production floor. Short-staffing typically results in lost production, while re-staffing accumulates expensive onboarding costs. If failure to manage materials and dusts is significant, expensive violations from OSHA and other health and safety organizations may also result. If hazardous materials are leaked to the external environment, they can contaminate local neighborhoods, ecosystems and waterways. Each of these expenses can be crippling to a facility’s reputation and cost management.