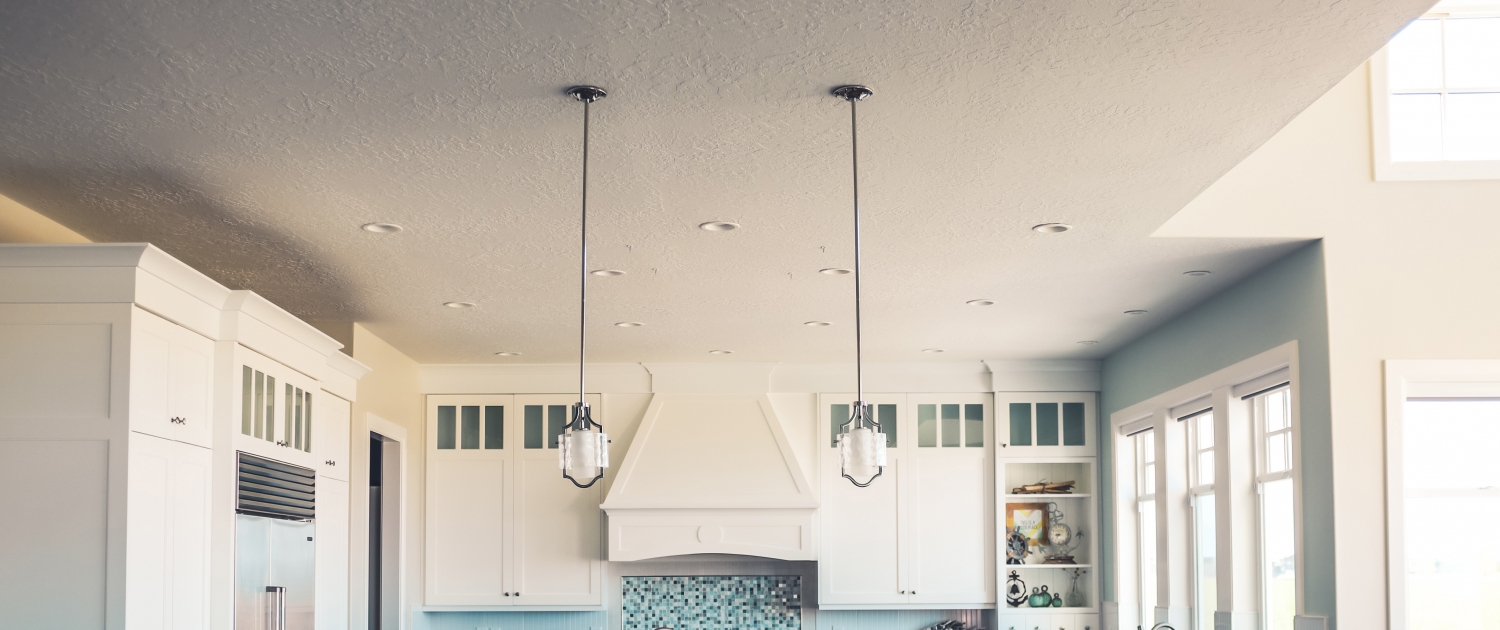
Client:
Quantity:
Size:
Application:
Handled Material Characteristics:
- Fine material particles
- Abrasive – 320 Brinell Hardness Number (BHN)
Results:
The client’s end product is ceiling textures, and wall and joint compounds. Phyllosilicates handling creates problems in many of the components within this company’s conveying system.
Previously, alternative slide gates were placed directly under rotary airlocks to protect the airlocks from the phyllosilicates being conveyed beneath them. As materials transported through the convey line at 10 psig | 0.69 barg, they abraded the slide gates’ blades and seals.
As a result, the gates were removed every 4 – 6 months and shipped back to the factory for rebuild. Each time this was done, total maintenance cost – including downtime, labor, shipping and repair – was estimated at $1,400 per gate.
Vortex identified the HDPV2 Gate as the ideal solution to this application. Because the HDPV2 was a new product at the time, Vortex approached the client with an opportunity to be a “test site” for this new equipment.
The Vortex HDPV2 Gate is specifically designed:
- To isolate pressures up to 75 psig | 5 barg
- To provide a positive seal of air, materials and dusts across the gate and to atmosphere.
- To handle moderately abrasive applications.
- To be easily maintained.
- With a partial Special Service Inlet and a beveled blade which “lifts” into a seat. This design replaces the standard slide gate’s “true end seal” design – therefore eliminating material packing into an end seal and associated sealing issues.
This client’s HDPV2 Gate was installed in March 2005. Four months later, it was removed for inspection – per their previous maintenance process. They found there was virtually no wear to the valve or its main seals. The gate was reexamined in December with the same results.
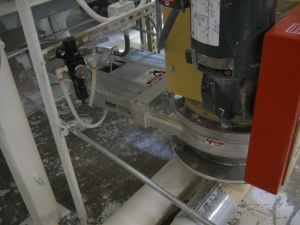
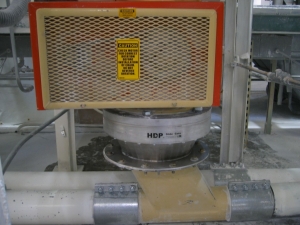