
Client:
Quantity:
Size:
Application:
APCO Packaging was founded in the mid-1980s in Bridgeview, Illinois, as a leading contract manufacturer of powder and liquid blending, as well as packaging. They blend and package a wide array of products, including:
- Liquids
- Detergents
- Sanitizers
- Commercial and consumer cleaning products
- Eco-friendly, oxygen-based liquid and powder cleaners
- Foot & odor control powders
- Powders and liquids for pod production
- Granular powders, including metal
- Algae control
APCO can assist customers who require just one facet of the powder and liquid blending or packaging processes, and can also provide start-to-finish manufacturing services.
A Long-Standing Client Relationship
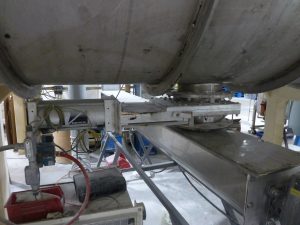
In 1990, APCO obtained their first Vortex product, an Orifice Gate, to be installed on a ribbon-paddle blender. APCO found that the gate worked so well in their application, they decided to specify Vortex gates on all future ribbon-paddle blenders that were to be ordered.
Since 1994, APCO has consulted Allen/Davis Technology Representatives, an equipment representative for Vortex, to find many other applications for Vortex products within their facility. Most prominently, all ribbon-paddle blenders in the facility utilize either a Vortex Orifice Gate or a Vortex Clear Action Gate.
“I specify Vortex products because of their reliability. It’s that simple,” said Clarence Totleben, manufacturing support engineer at APCO Packaging. “We work on tight schedules and our customers depend on their order arriving on time. We cannot afford to have our mixers down because of a component.”
In 2015, APCO contacted Allen/Davis Tech with a need to replace one of their original Orifice Gates for the first time. The gate had been used for 25 years to shut-off material flow when filling bulk bags and drums.
“I cannot even tell you how many times that gate had been actuated,” said Totleben. “When filling bulk bags and drums, the gate was constantly opening and closing during the process. In reality, the gate did not fail us; we accidentally damaged it when handling a sticky substance that was new to us. The gate did, however, complete the job.”
APCO has had few occasions where maintenance needed to be performed on their Vortex gates. Of those occasions, there has been little delay in production since maintenance can be performed while the gate remains in-line.
“A couple of our Orifice Gates had light dusting coming through the ports located at the front of the gate,” said Totleben. “We simply loosened the nuts along the lateral aspects of the gate and removed a shim from each side – without taking the gate out of line. After re-tightening the nuts, the gate sealed like it was brand new again. The whole process takes less than ten minutes.”
Totleben added, “As APCO continues to grow, we will continue to specify Vortex on new equipment. The performance of Vortex products, coupled with the company’s great customer support and their expert knowledge of material handling characteristics, is 100% worth the peace of mind I get.”