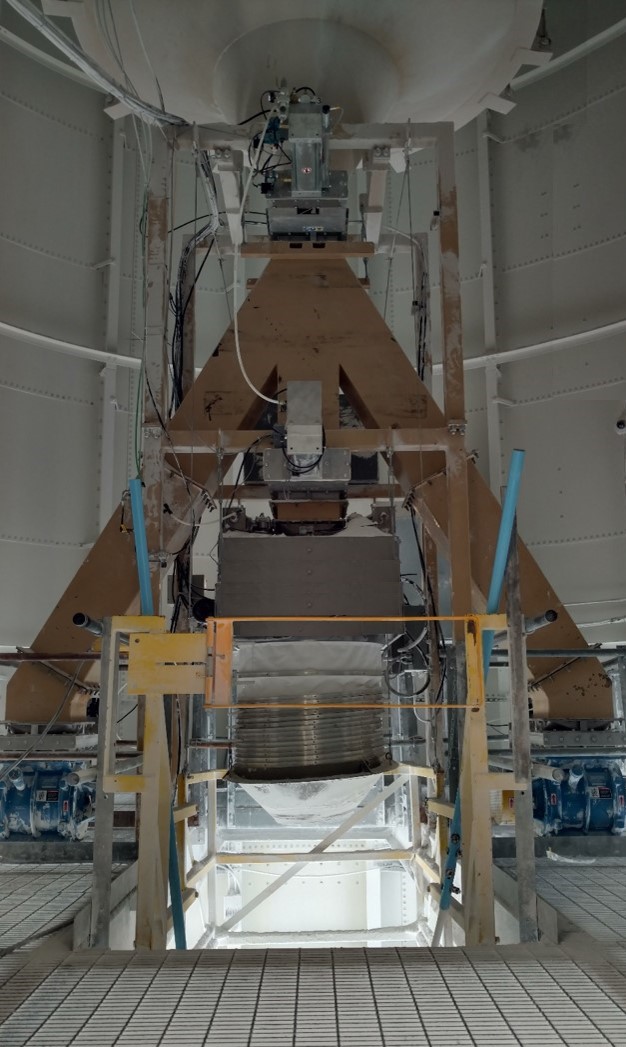
Client:
Quantity:
Size:
Application:
Vortex completed a project with a limestone processor to provide more than 10 Clear Action Gates for handling finished limestone powder. Upon installation, the Clear Action Gates began having complications in the given application. A Vortex field service technician immediately traveled to Ohio to troubleshoot the client’s issues and make necessary gate modifications. Because of this outstanding field service, Vortex and the client have formed a lasting relationship for future projects.
The Process: Transferring Finished Limestone Powder in a Pneumatic Conveying System
The client uses three silos to store finished limestone powder.
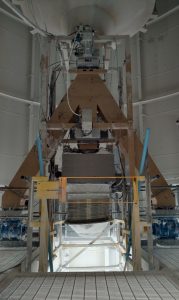
Below each silo, a Vortex Clear Action Gate is used to isolate the silo from the process line. Once the gate is opened, finished limestone powder is discharged into a three-way gravity diverter.
Below the diverter’s straight-through channel, a second Vortex Clear Action Gate isolates the diverter from a loading spout. When the gate is opened, finished limestone powder is discharged through the spout to fill open trucks at the loadout station below.
A third and fourth Clear Action Gate are installed at each of the diverter’s outside channels. Each gate is used to isolate the diverter from a rotary airlock below. Once materials are fed through each rotary airlock, they are discharged into two pneumatic convey lines. Each line transfers materials to two separate bagging stations, so that finished limestone powder can be packaged for bulk sale.
To allow metering into the diverter, the client equipped each Clear Action Gate installed below a silo (qty. 3) with a Vortex Infinite Variable Positioner (IVP). At center, this allows volumetric flow rate to be adjusted throughout the loading process. To each side, this allows material flow control
through each rotary airlock, to ensure accurate batchweights for transfer to each bagging station.
The Project: Replacing Pre-Existing Slide Gates with Vortex Clear Action Gates
Prior to this project, the client was using slide gates supplied by another manufacturer. Over the 2 ½ years that the previous gates were in service, the client had constant issues with poor sealing and material leakage. To resolve these issues, the client insisted that their pre-existing gates be replaced with Vortex Clear Action Gates.
For this project, Vortex supplied:
- Quantity: 12 Clear Action Gates
- Size: 14 in | 355 mm
- Each gate was equipped with a Special Service Inlet.
- Each gate was equipped with an Air Purge Assembly.
- (qty. 3) gates were equipped an Infinite Variable Positioner (IVP).
Once the Clear Action Gates were installed, the client realized the Vortex gates were also having complications in this application. A Vortex field service technician immediately traveled on-site to assess the client’s issues. It was determined that because of the unique characteristics of finished limestone powder, adjustments would need to be made.
To resolve this issue, Vortex modified the Clear Action Gate’s pressure plate and bonnet seal designs. With this adjustment, a better seal was made across the blade to prevent material migration into the gate’s body.
This subtle alteration was the difference and today, the client has more than 20 Vortex Clear Action Gates – all of which are running smoothly and without error. In fact, the revised seal designs have been so effective that Vortex now classifies them as standard.
Once the previous slide gates were removed and the Vortex Clear Action Gates were installed, it took less than two months for the client to realize a significant improvement in the efficiency of their loadout and bagging processes.
Feature: Special Service Inlet
In this client’s process, finished limestone powder is being pneumatically conveyed via positive pressure at 7 – 9 psig | 0.48 – 0.62 barg.
The purpose of a Special Service Inlet is to direct material flow through the center of the gate. In doing so, a dead pocket is created along the edges of the inlet that allows materials to fall away from the leading edge of the blade as the gate closes. This hinders materials from packing in the gate’s seals, which would otherwise allow material migration into the gate body, material leakage through the valve, and blade actuation errors.
Feature: Infinite Variable Positioner
The purpose of IVPs is to control the volumetric flow rate of materials, in order to improve process accuracy with more precise batchweight calculations and reduce fill times between workstations. IVPs may also be used in batching, bulk bag filling, dribble flow, loading and transport, loss-in-weight feeders, maintaining volumetric flow rates, controlling material flow into screw conveyors, scaling, and more.
Unlike other flow control assemblies, the IVP allows total control of blade positioning on both the opening and closing strokes. Using a linear output transducer, the IVP relays blade position feedback along the full stroke of the blade. An IVP can be set up for either manual operation using an IVP Controller, or automated to be controlled through a PLC system.
If an operator decides to make adjustments in flow control, a primary benefit of the IVP over other flow control assemblies is rather than having to make manual adjustments at-the-valve, all flow control adjustments are made remotely using technology.
The Vortex Infinite Variable Positioner is the industry’s most accurate technology for controlling material flow. When automated, the IVP can actuate in increments of +/- 2%. When manually controlled, the IVP can actuate in increments of +/- 4%.
Project Completion
After working through these issues alongside a Vortex field service technician, this limestone processor was very impressed by the intimate customer service Vortex provided throughout the resolution process. With this field service trip, a high level of trust was created between Vortex and this new customer. Moving forward, the client plans to replace other equipment in their facility with Vortex components – largely due to the peace of mind they now have in Vortex and the great lengths Vortex will go to ensure satisfaction.