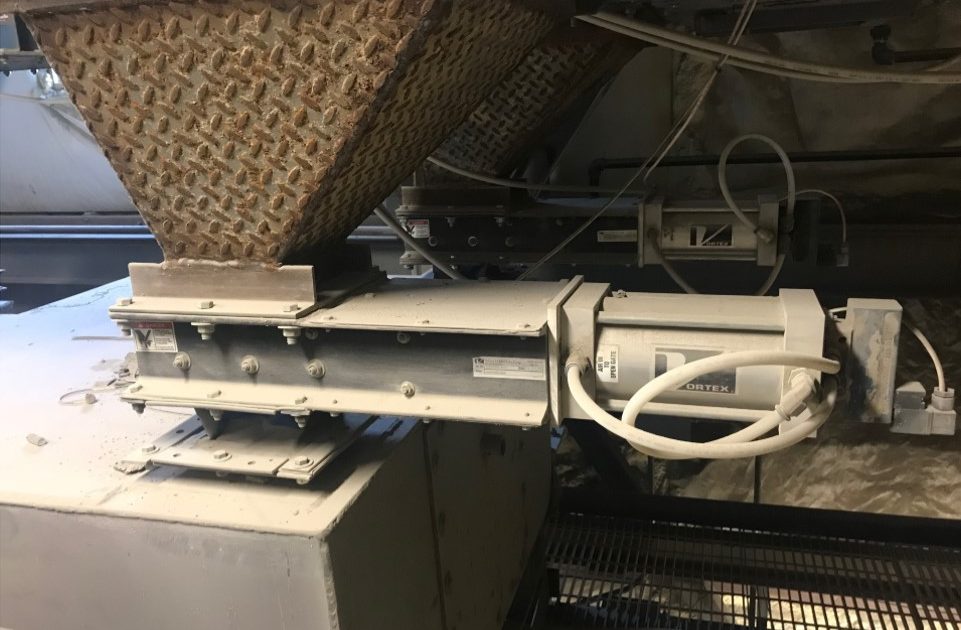
Client:
Cement Mortar Mix manufacturer
Quantity:
Size:
6 in. (152 mm)
Application:
Each Vortex Aggregate Gate is installed below a surge hopper and is used to feed fine sand materials into a mixer. The TSG Gates are also installed below separate surge hoppers and are responsible for feeding fine sand & mortar mixes onto a scale. Once weighed, the mixes are transported to a packaging line. There, they are packaged as 5 gallon units – either into bulk bags or buckets
Features (Aggregate Gates):
- Gate body constructed from heavy-duty carbon steel.
- Blade & material contact areas constructed from AR 400 carbon steel.
- Rollers are externally greased & constructed from hardened steel.
- Equipped with inlet deflectors to reduce wear (pictured).Inlet deflectors protect the gate’s rollers & seals from blast abrasion as materials flow through the valve.
- Gate features a displacement pocket (pictured). Instead of packing and jamming material into an end seal, the gate’s blade stops part way into a displacement pocket. This allows materials remaining at the leading edge of the blade to fall away into the process line below, rather than packing into the end seal.
Features (TSG Gates):
- Gate body constructed from heavy-duty carbon steel.
- Blade & material contact areas constructed from AR 400 carbon steel.
- Leading edge of the blade is beveled.
- Rollers are CAM-adjustable & constructed from hardened steel.
- Built with replaceable bonnet seals. Seals are removed through bonnet access doors along the lateral aspects of the gate (pictured). New bonnet
seals can be driven into the gate as the worn seals are simultaneously ejected out the other side. - Gate features a displacement pocket (pictured). Instead of packing and jamming material into an end seal, the gate’s blade stops part way into a displacement pocket. This allows materials remaining at the leading edge of the blade to fall away into the process line below, rather than packing into the end seal.
Results:
All 6 Aggregate Gates were installed in November 2006. All 5 TSG Gates were installed in November 2015. Since install, the gates have required no maintenance. The client enjoys the improved performance and efficiencies the gates have brought to their process.
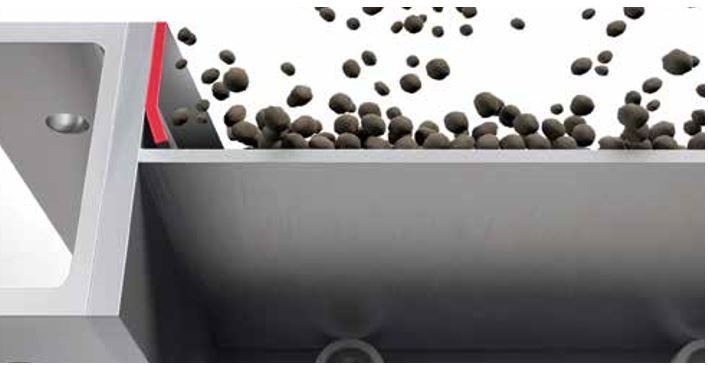
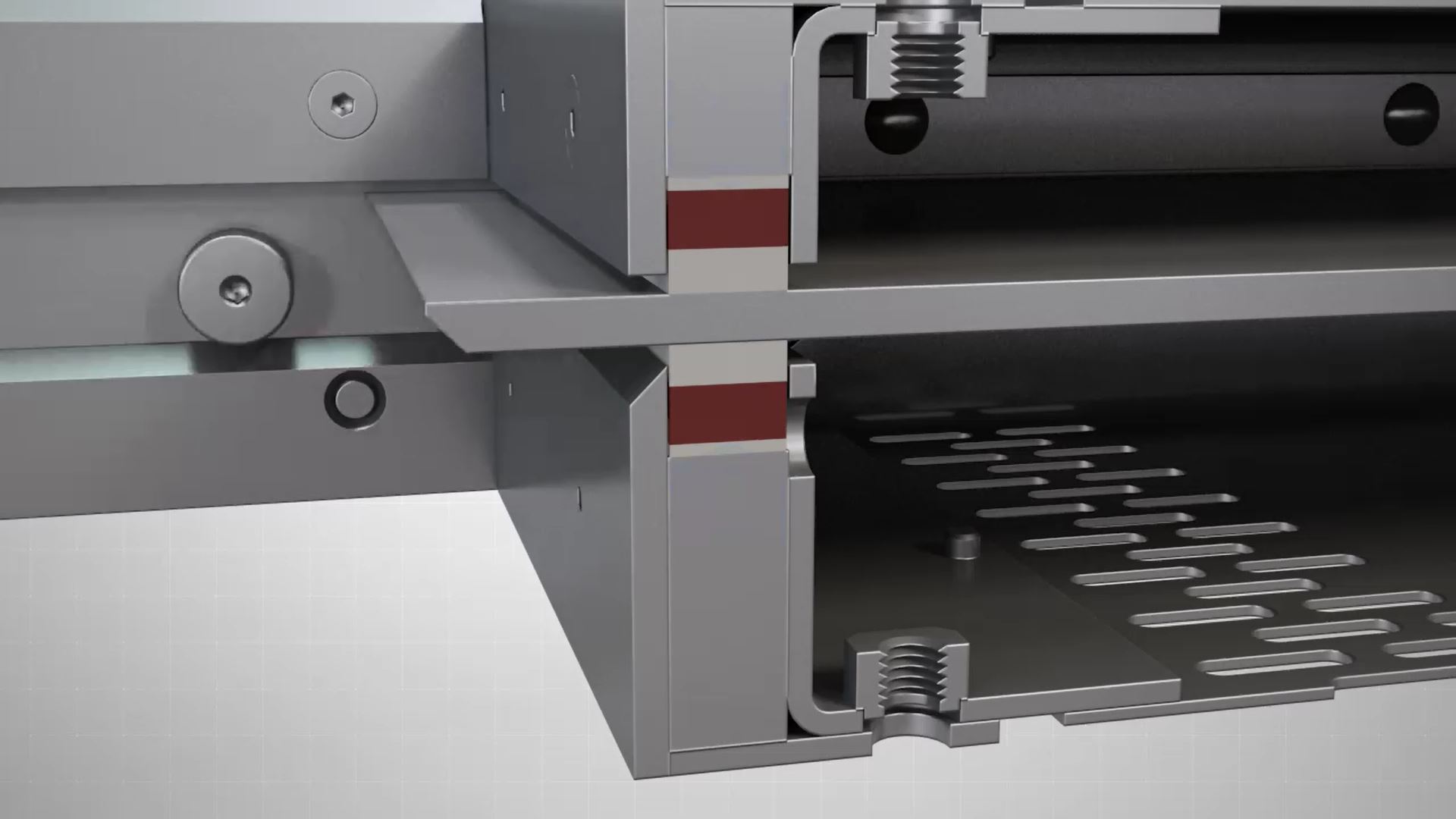
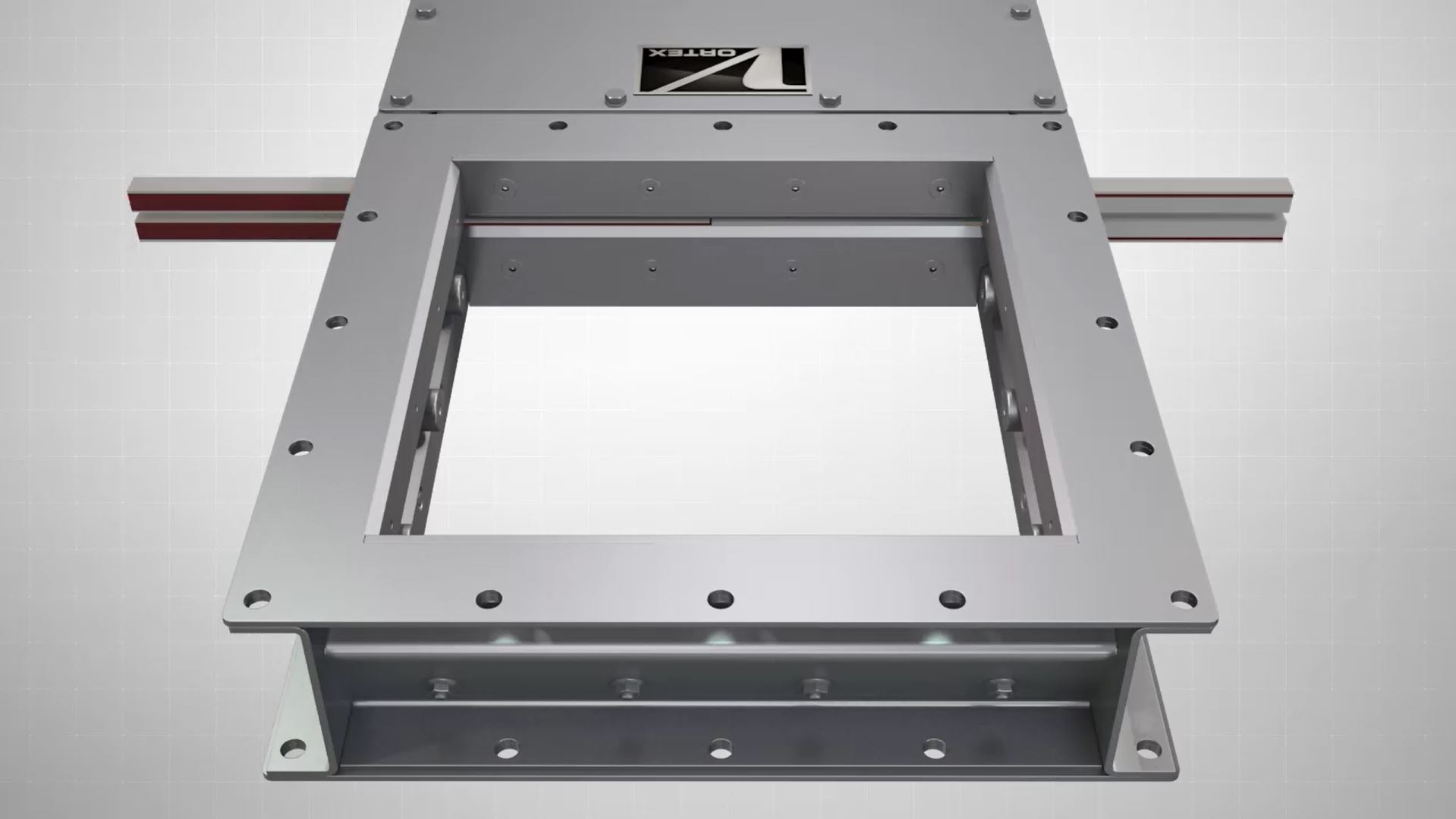
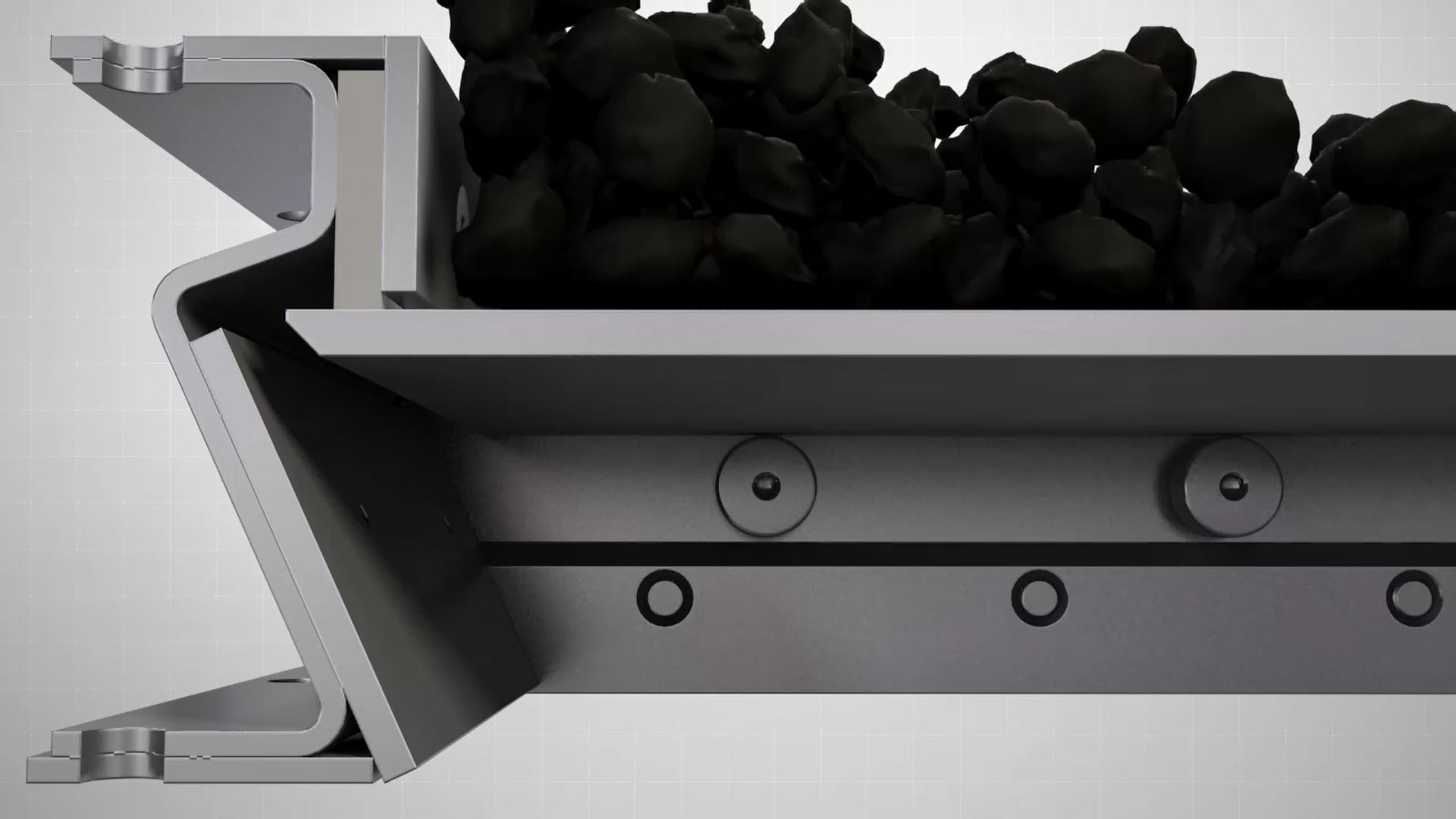