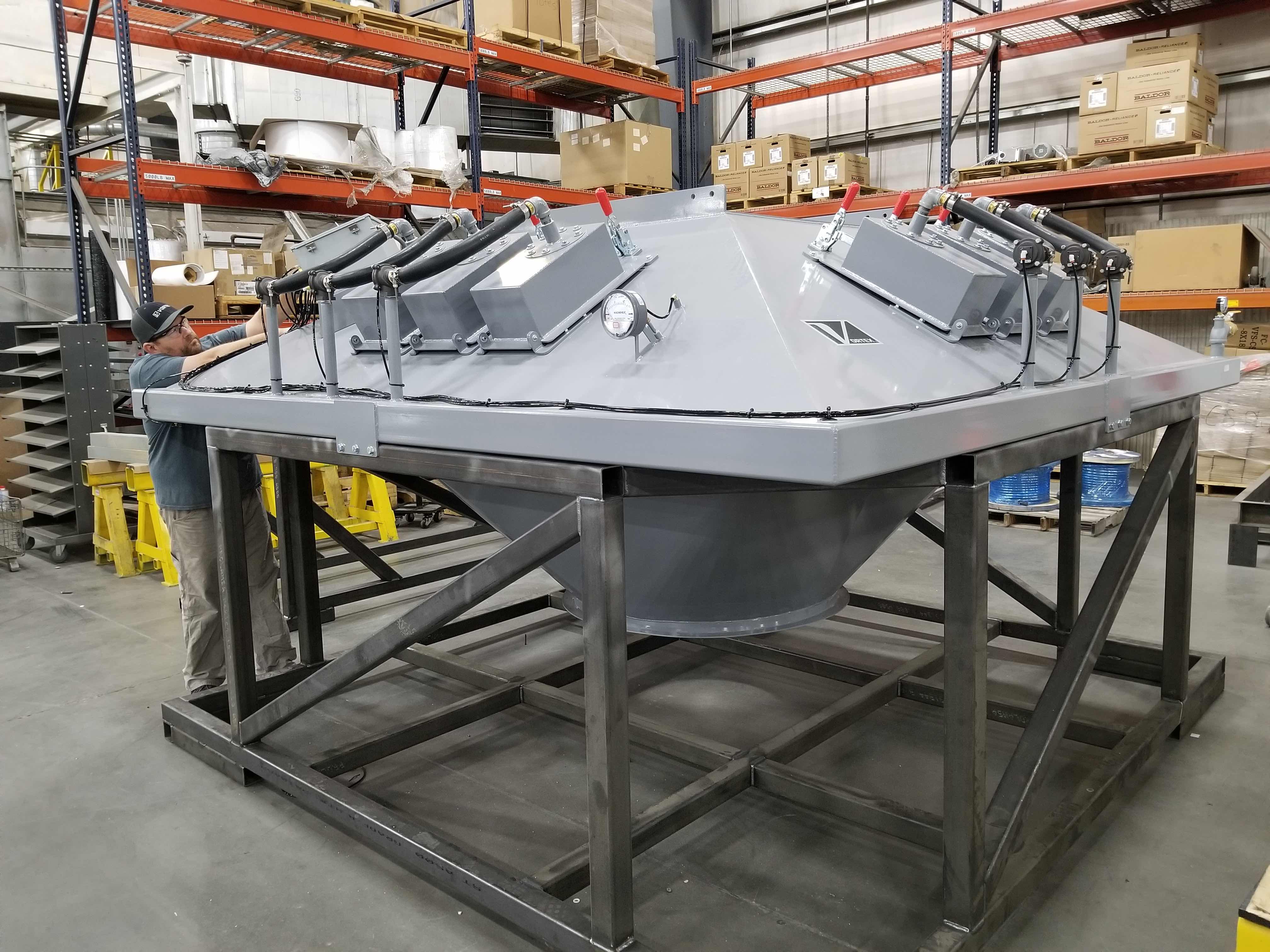
Client:
Quantity:
Size:
Application:
As featured in Bulk Handling Review
by Austin Anderson
Loading dry bulk solids can be a quick and effective solution for transporting product, but while the process provides many benefits, there are considerations that must be taken into account.
Dusts released into the atmosphere during loadout can have a plethora of negative effects on nearby populations and ecosystems. Dust can pollute waterways, contaminate nearby homes, businesses and vehicles, and if inhaled, can create health risks.
When properly applied using proprietary engineering controls (headchute, spout, dust collection), dust-free loading can be achieved.
Vortex Loading Solutions offer a complete line of versatile options specifically designed to capture fugitive dusts, prevent material waste, and ensure plant and environmental safety in the loading process with low maintenance and service expenses. Compared to traditional industry loading equipment, Vortex Loading Spout Systems offer many key benefits. Among them is the Vortex Filtration System.
A Vortex Filtration System is specifically designed to:
- Displace dust-laden air from its source.
- Separate dusts from the air.
- Re-entrain the filtered dusts back down into the load.
- Exhaust the cleaned air to atmosphere.
They are engineered to capture the fugitive dust emitted from the spouts and deposit it back into the material flow during the loading process, eliminating material loss. These systems are more cost-effective than a free-standing dust collection system, which often requires the installation of additional ductwork, discharge airlock and some way to reintroduce the material back into the system.
These very compact systems are used in conjunction with standard volume loading spouts in enclosed, open, or combination loading applications. They have a unique square-shape and are designed with a narrow profile to reduce stack-up height, as available space at the loading station is often limited, which allows for a lower profile and compact model.
Pulse jet system
An automatic pulse jet filter cleaning system uses high-pressure compressed air to purge trapped dust from the filters and send it back down the spout and into the vessel.
Throughout the loading process, the pulse jet system cycles from filter to filter. Once the loading process has completed and the blower is shut down, one final cycle frees the remaining trapped dust and sends it down the spout and into the load.
Continuously purging the filters of dust throughout the loading process increases filter life, minimises materials waste, and allows the filter system to maintain consistent suction.
Filter cartridges
Vortex Filtration Systems are ‘active units,’ meaning an air withdrawal forcibly pulls displaced air and dusts through the filter cartridges to initiate the filtration process. These systems feature pleated polyester filter cartridges that are easily replaceable through a quick-look filter cartridge access, reducing maintenance downtime. Panels are hinged and secured by a stationary clamping mechanism to accelerate the inspection and maintenance processes, and for access without additional tools.
Easily visible Magnehelic pressure gauges indicate when it is time to change the filters. These cartridge filters feature a reducing coupler above them that draws the air directly through. This design requires fewer parts that can wear or fail, keeping maintenance costs low.
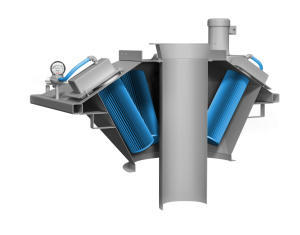
The multi-stage filter located at the bottom of the spout can be used for dust control in longer spouts with extended travel distances. It performs much like the compact in-line filter, except that it has four high-volume exhaust blowers. The unit pulls the material dust within the outer sleeve upward and into pleated cartridge filters. This system can be used as a stand-alone filter or in conjunction with the standard compact in-line filter.
The Vortex Filtration System is not a dust ‘collector’ – it is a dust ‘filter.’ This means dusts are temporarily captured before being purged back out of the filter cartridges and back into the material flow stream. Improved management of dusts at the point of loading instead of routing them to a central dust collection system leads to improved profitability and increased service life. If required, the Vortex Filter can be hooked up to a dust collector.
Available material contact options in a dust filter include 304 stainless steel, 316L stainless steel and A36 mild steel providing solutions for a number of applications, including food friendly options.
Vortex Telescoping Loading Spouts equipped with a Vortex Filtration System are ideal for the loadout of open, semi-enclosed and closed vessels including trucks, railroad cars, tankers, ships, barges and open stockpiling.
Standard volume filter systems / Compact in-line filter systems:
- Model VFS-10: 400 cubic feet per minute load rate capacity at eight inches static pressure. Features four cartridge filters.
- Model VFS-25: 1000 cubic feet per minute load rate capacity at eight inches static pressure. Features eight cartridge filters.
- Model VFS-40: 1600 cubic feet per minute load rate capacity at eight inches static pressure. Features eight cartridge filters.