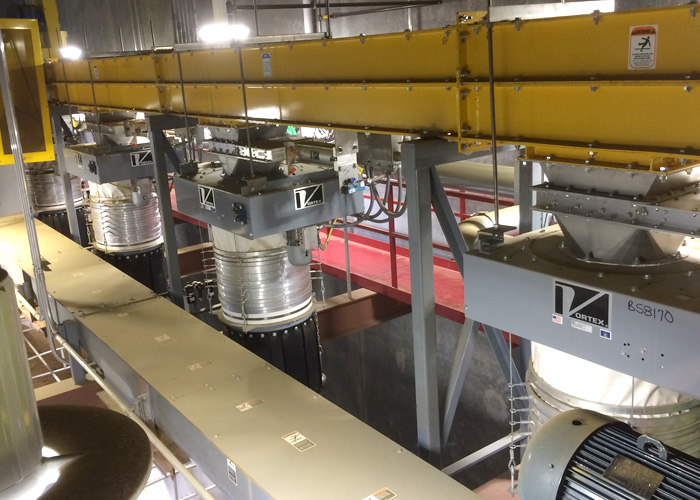
Client:
Quantity:
Size:
Application:
A loading spout attached to the bottom of a silo or hopper, or located at the end of an air conveying system, is used for distributing dry bulk materials in open trucks, stockpiles, railcars, tank vehicles, barges and ships. It is used mostly in grain elevators, ship ports and cement plants conveying dry bulk material.
Here are three reasons why every operation which loads dry bulk material into open or closed vehicle containers needs retractable loading spouts as part of their process.
#1 – Capture Fugitive Dust: Health & Safety Issues
Clouds of debris and dust are formed when dry materials such as grain, coal, cement, and rock are loaded in bulk. The airborne fugitive dust can cause employee health issues including chronic lung disease, eye sight problems and skin allergies.
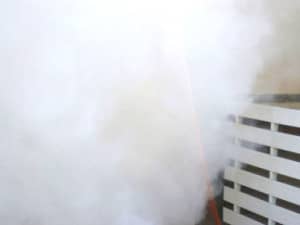
Employees are also prone to slips and falls when the fugitive dust accumulates on top of the vessels, elevated walkways, floors and ladder rungs. The dust accumulation problem in the grain industry can exacerbate because the dusting on top of building structural members, walkways, ducting, piping and equipment can cause dust explosions causing injuries, structural damage and even death.
Health and safety agencies can issue fines for job site injuries and citations if annual inspections are not up to par. These costs can add drain a company financially.
Installing a loading spout in your operation can contain the flow of material into a confined area reducing the radius of debris and dust. With an additional aeration system added to the spout, more dust can be contained. An aeration system can be installed on the inside bottom of a storage container or mounted to follow a specific path inside the plant. Aeration systems include aerated conveyor systems, aerated bin bottoms, aerated trough systems and articulation arm positioners. All Vortex aeration systems are custom designed and manufactured to your individual project specification, so they can handle any material and desired flow rate.
#2 – Ensure Plant & Environmental Safety: Air Emission Issues
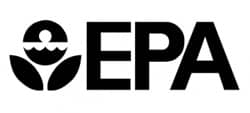
Airborne fugitive dusting is a leading concern of environmental agencies resulting in large fines. In some cases, the government can shut down operations until improvements are made, which lead to lost shipping profits, customers, etc, for a company.
Having a loading spout with a blower and integral filter can send the fugitive dust to draft back through the sleeve of the loading spout, trapping material dust temporarily in the filter cartridges. An automatic onboard pulse system dislodges the dust and fine particles, reintroducing them back into the product feed. It continuously purges the filters to keep the equipment working optimally and free of dust build-up. This prolongs the life of the filter cartridges significantly.
#3 – Prevent Material Waste: Lost Profits & Clean-up Costs
Material lost due to fugitive dusting and spills over a year’s time can result in lost profits. Also, labor costs associated with having to clean up accumulated material over a year’s time can often times exceed the cost of a complete load-out system.
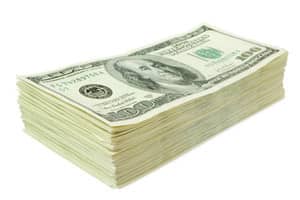
To overcome these problems, the loading spout’s discharge cone should be designed to seat directly into railcar hatches and semi tankers to minimize fugitive dusting. Sensors attached to the inside of loading spouts automatically measure product levels. The sensors also provide a signal that automatically stops the flow of materials to prevent overfilling and/or plugging within the spout.
The hopper’s discharge flange is designed to directly connect to the inlet of the loading spout. A pre-wired handheld control pendant with push buttons is available as an option to allow the operator to manually control the positioner, which can also be controlled remotely from a central location.
A loading positioner can also help minimize spills when loading. The positioner is used in with standard volume loading spouts to facilitate and speed up the loading of open or enclosed trucks and railcars at loadout stations. They allow for the fast and accurate single-axis or double-axis placement of the loading spout, which eliminates the need to reposition vehicles once they have entered the loading station and overestimating the location of the vessel opening.
Complimentary Components
Most often, loading spout systems will be used in conjunction with slide gates, diverter valves and spinloaders that control the material flow during the loadout process. Used at the bottom of a silo or hopper to shut off material flow, slide gates are placed right above dust collecting filter systems, loading spouts and positioners.
Vortex offers a complete line of versatile loading spout systems, gates and diverters for your loading process. We can also custom engineer any telescopic loading spout system to meet your most demanding loadout application requirements, including corrosive or hazardous materials, long distances, low and high temperatures, etc. Vortex fully assembles, factory tests and packages every loading spout system before shipping it to your facility to provide ease of installation and to ensure optimal performance once in use.
Vortex Warranty
Vortex’s loading spouts are unique for loading bulk materials into open and/or enclosed vessels because of their 4-cable lifting design providing maximum stability, compared to the standard 2- or 3-cable systems. The in-line drive system also incorporates special 3-piece CNC-machined pulleys that feature chamfered edges and precision cable grooves to significantly reduce cable wear and back lashing as the loading spout extends and retracts, especially during the misalignment of the hatch opening. Because the cables do not fray, cable failure is nearly eliminated and so is costly downtime for repairs.
The warranty covers any Vortex loading spout cable that breaks due to friction from the pulley. The 3-piece CNC machined pulley features chamfered edges and precision cable grooves to significantly reduce cable wear and back lashing as the loading spout extends and retracts. Because the cables do not fray, cable failure is nearly eliminated and so is costly downtime for repairs.