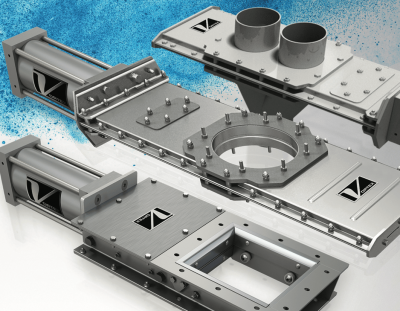
Client:
Quantity:
Size:
Application:
Transporting and conveying dry bulk solids is never a straightforward task. Many in the industry would go as far as saying success takes a mix of "black magic", science, and engineering. Indeed it can be difficult, but the reality is that it takes many years of experience to have some reasonable guarantee you'll get it right. Even then, perfection can be fleeting!
The characteristics of dry bulk solids are endless, so there is no all-encompassing solution for every application. It doesn't matter if it is a silo, sieve, sensor, conveyor, or feeder. With solids, an "out of the box" solution is often not possible. This is why Vortex offers such a wide range of slide gates, diverters, and loading solutions for handling nearly any type of dry solids, from fine powders to heavy ore. In fact, approximately 60% of products manufactured by Vortex has some type of engineering modification.
Over the past 40 years as an engineering partner and supplier to the dry bulk material handling industry, you could say that Vortex has acquired a lot of that "black magic" in the form of experience. As painful as the occasional misapplication can be, it is a part of that learning curve we all face in the industry.
Most importantly, from experience comes innovation. At Vortex we take great pride in developing new products that take care of problems our customers face. Always asking ourselves how it can be done better, especially from the end user's perspective. The following case histories highlight how experience leads to innovation and an ultimate solution.
Standard Modifications
Although each manufacturer will have their own standard products, some may or may not offer extra features. Here are a few standard product modifications that Vortex offers to enhance performance across varying applications.
Abrasion-Resistant Liners – Abrasion resistant liners on the inlet of the gate address potential wear issues from either the volume or the abrasiveness of the material being handled. The liners are replaceable when needed.
Abrasion-Resistant Blade – The gate's blade can also be manufactured of abrasion resistant steel. The combination of the abrasion resistant blade and liners are important in providing a gate that offers longevity and an exceptional life-cycle cost.
Adjustable Rollers – Externally-greased steel adjustable rollers are used to keep the blade dust tight.
Bonnet Purge – The optional bonnet purge is utilized to keep material out of the body of the valve and in the material stream.
Displacement End Pocket – A pocket displaces the material at the leading edge of the blade as the blade closes. Rather than the blade jamming and packing this material into an end seal, the blade stops part way into the pocket. Material falls away from the blade and re-enters the material flow stream area. This feature can increase the valve's service-life and reduce downtime costs related to maintaining and replacing end seals.
Optional Configurations – Available in straight leg and wye line configurations.
Replaceable Seals – Seals reduce interior valve dusting and can be replaced while the valve is in-line.
Return Pan – A return pan can be added to seal fine material internally or to atmosphere. With this feature, material that enters the bonnet of the valve is returned to the material flow stream, thus reducing material leakage to atmosphere.
Wear-Compensating Seals – Pressure loaded, polymer bonnet seals offer a dual purpose. They act as a wiper for material that may be on the blade as the blade retracts. They also seal material from entering the bonnet area of the gate. The "live load" on the back of the seal strip continues to apply pressure to the seal even as it wears. At a certain wear point, seals may be accessed and replaced from the outside of the gate, while the gate remains in-line.
Wear-Reducing Material Deflectors – Material deflectors are placed around the inlet of the valve and protect it from the material flow stream. By deflecting material away from the hardened steel rollers and blade seals, this feature significantly reduces wear and downtime keeping the valve in service longer.
Wear-Resistant Bucket Design – A wear-resistant bucket constructed from durable abrasion resistant steel and an optional ceramic liner can be added to reduce potential wear to the bucket. For even more durability, the addition of an optional honeycomb liner allows material to abrade on itself instead of the bucket.
Knowledge & Experience in Application Engineering
Vortex has engineered well over one billion variations of slide gates, diverter valves, and loading spouts. There are times we can take one of our standard products and make some minor modifications to fit the applications. There are other times when the only thing left standard on the product is the Vortex logo. Vortex’s design philosophy is to develop products that compensate for wear, require minimal spare parts, provide in-line maintenance, and maintain a longer service life than market alternatives. We will continue to innovate solutions for you.