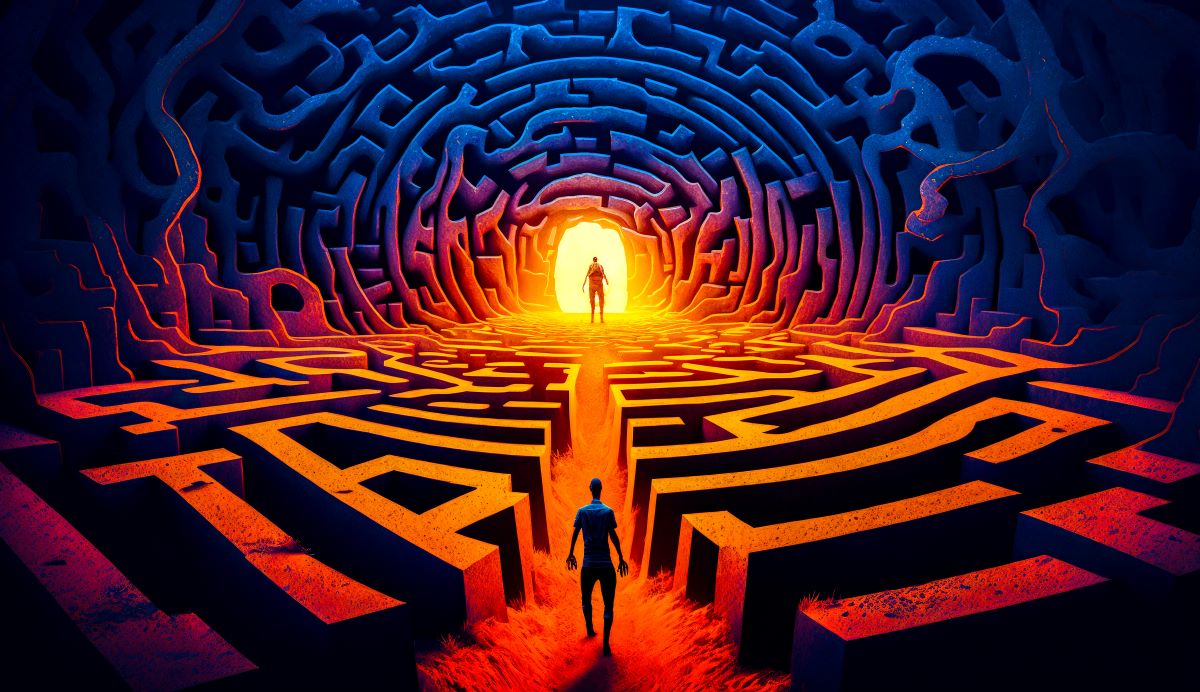
Client:
Quantity:
Size:
Application:
As Published in World Cement
Loading dry bulk solids presents a complex set of challenges that industry professionals must tackle to ensure smooth and efficient operations. Key concerns such as labour, safety, environmental impact, and system efficiency play crucial roles in the loading process and can give rise to various issues if not properly addressed. For instance, the continued scarcity of labour makes innovation and automation critical to supporting ongoing demand, while overlooking safety measures may result in workplace accidents and potential damage to equipment. Environmental considerations, such as dust emissions and spillage, are vital in maintaining compliance with regulations and protecting the surrounding ecosystem. Furthermore, optimising efficiency in the loading process ultimately impacts the bottom line, making it essential to adopt innovative technologies and strategies that streamline operations. By understanding and addressing these challenges, companies can deliver a high standard of performance, ensuring the successful handling and loading of dry bulk solid materials.
Labour and safety challenges
Loading dry bulk solids into trucks with hatches involves a combination of labour and personnel safety challenges that must be effectively managed to ensure efficient and secure operations. A primary labour and safety concern is the coordination between spout operators and truck drivers, as miscommunication can lead to errors and potential accidents. Manual handling of the loading spout, alignment with the truck hatch, and monitoring material flow requires skilled labour and constant attention. In terms of safety, controlling dust emissions is crucial to protect workers’ respiratory health and maintain environmental compliance. Another safety challenge is preventing material spillage during loading, which can create slippery surfaces and increase the likelihood of accidents. Employing level-sensing devices and ensuring proper alignment can minimise spillage and enhance safety. By addressing these labour and safety challenges, companies can perfect the loading process for dry bulk solids while maintaining a safe work environment for their personnel.
Environmental challenges
Loading dry bulk solids also presents a range of environmental safety challenges that need careful consideration of design, safety standards, and loading processes. A primary concern is managing dust emissions, as excessive airborne particulates can lead to environmental compliance issues and pose health risks for operators. To address this issue, implementing efficient dust collection systems and using sealed loading spouts are essential in minimising fugitive dust emissions. Material spillage during the loading process can also have an environmental impact, which can result in the contamination of the surrounding area and the waste of valuable resources. Adhering to established safety standards and best practices is crucial in maintaining environmentally responsible operations. This includes regular equipment inspection, maintenance, and operator training on safe handling procedures and potential hazard identification. Integrating innovative design elements and technologies, such as automated positioning systems and retractable spouts, can enhance the loading process’s environmental safety by reducing human error and improving operational efficiency. By addressing these environmental safety challenges, companies can contribute to a cleaner and more sustainable future while loading dry bulk solids.
A new automated loading system
Introducing the Vortex Automated Loading System (VALS). A new Vortex solution designed to optimise loading operations for dry bulk solids. Combining the robust capabilities of Vortex Loading equipment, this innovative system streamlines the loading process, minimises material spillage, effectively controls dust emissions, decreases direct labour costs, and enhances overall operational efficiency.
System overview
The primary purpose of the Vortex Automated Loading System is to facilitate the efficient and precise loading of dry bulk materials into hatches on trucks. The system operates through the seamless integration of a few core components: Vortex camera and PLC system, Vortex Loading Spouts, In-line Filters, and Positioners. These components work together to provide a clean, accurate, and reliable loading solution that meets the highest industry standards for safety and performance.
Automated loading
Automated loading fully automates the loading process by removing the labour typically used to locate the spout inside the truck through hatch finding technology using cameras and images to automatically seat the spout scavenger into the truck hatch. Once the truck driver has parked on the scale and positioned the hatch in the target area on the screen display, they are then able to remain in the truck while the automated loading system goes to work loading material into the truck.
Camera and PLC system
The Vortex Camera system along with a PLC (Programmable Logic Controller) locates the hatch and controls the Vortex Positioner and Loading spout to properly seat into the vessel hatch that the material is being loaded into. With the VALS system your company will see more consistent load times as it is being controlled by the PLC instead of human interface. The PLC is programmed to load each container in a consistent manner. This ensures each time the system is triggered to load it goes through the same process without receiving any distractions (phone calls, etc.) that would typically be part of a manned operation.
Loading spouts
Loading spouts are designed to handle various types of dry bulk materials, offering flexibility and adaptability to different loading applications. These spouts feature cone-in-cone stacking technology, enabling smooth extensions and retractions while maintaining material containment and dust control. The outer sleeve material options provide durability and resistance to wear, ensuring longer service life and reduced maintenance requirements.
In-line filters
In-line Filters play a crucial role in controlling fugitive dust emissions during the loading process. These filters capture dust-laden air, separate the dust particles from the air, and reintroduce the filtered dust back into the load. The compact design of the Vortex In-line Filtration System allows for easy installation in limited spaces, while the vertical mounting of filter cartridges ensures optimal performance and extended service life.
Positioners
Positioners are essential components of the system, being able to automatically seat the spout into the open hatch, providing precise positioning of the loading spout above the truck hatch. The Vortex Dual-Axis Positioners allow for smooth and accurate movement along X and Y axes, enabling the system to achieve optimal alignment with the loading vessel. This feature significantly reduces material spillage and ensures a safe and efficient loading process.
Additional equipment
Aero-Troughs, Aero-slides, Bin Bottoms, Shut off valves, and Flow Control valves are examples of equipment that is utilised in many load out operations. Though this equipment is not required for automated loading in a number of circumstances it can be programmed into the automated system functionality to further improve the capabilities and efficiency.
System features
VALS works in a variety of lighting and weather conditions and is capable of being integrated with most site-specific software. Vortex technical support is also available during installation and start-up. The system able to eliminate the need for physical interaction between employees and equipment during the load out process thus decreasing the chance for safety related incidents. Truck drivers can remain within their vehicles on the scale while VALS quickly goes to work loading the material. Similarly, its automation means it is no longer needed for multiple employees to be present for material loadout. Labour availability and costs are no longer a concern with VALS and the reduction of employee involvement means fewer chances for human error and a more streamlined loading process.
Case study: Cement Manufacturer in Eastern Kansas
This cement producer in Kansas was familiar with Vortex because they had utilised their slide gates and diverters at other facilities. When they decided to create a new cement terminal in Eastern Kansas to expand their capacity and improve logistics, they partnered with a renowned engineering firm who contacted Vortex about providing an automated loading solution. Vortex set to work designing a 500 tph system that could deliver top of the line efficiency and safety.
Equipment Provided
Aero Flow Troughs (Not Pictured)
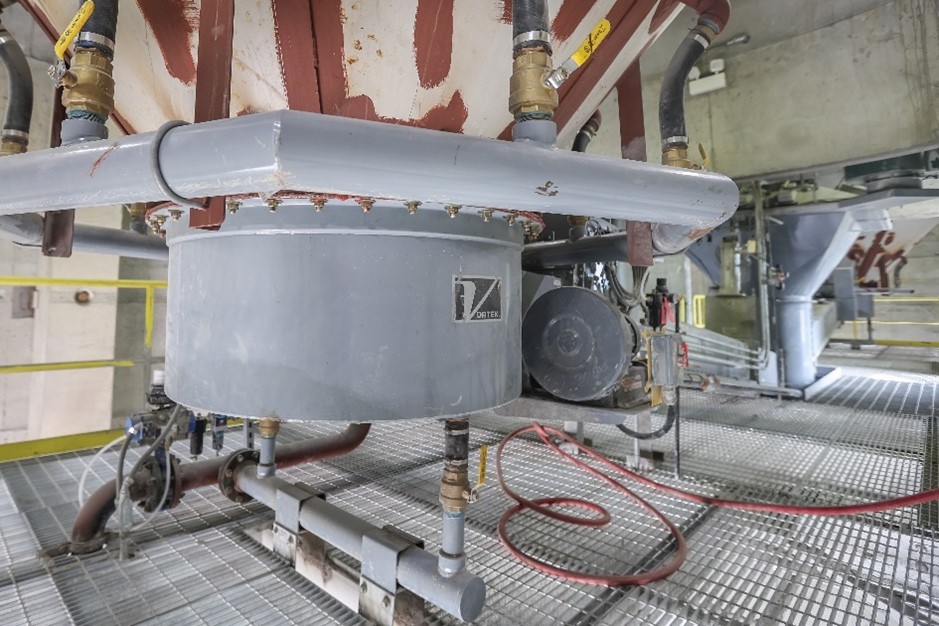
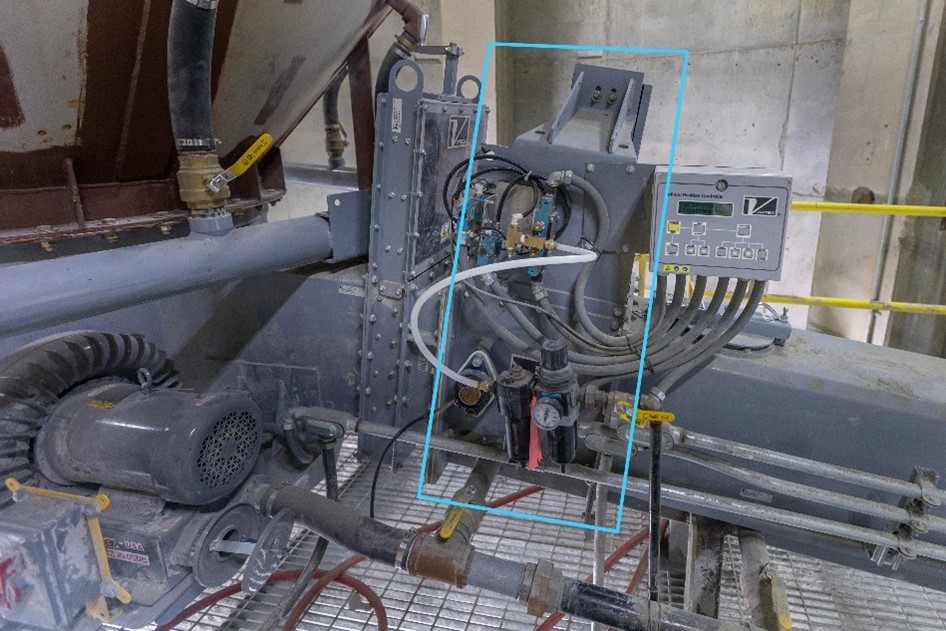
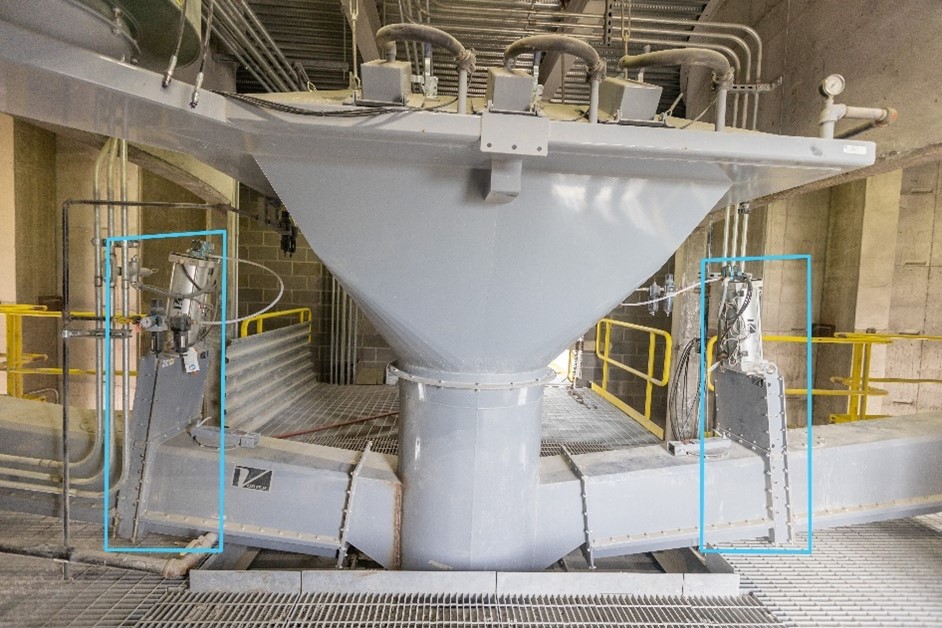
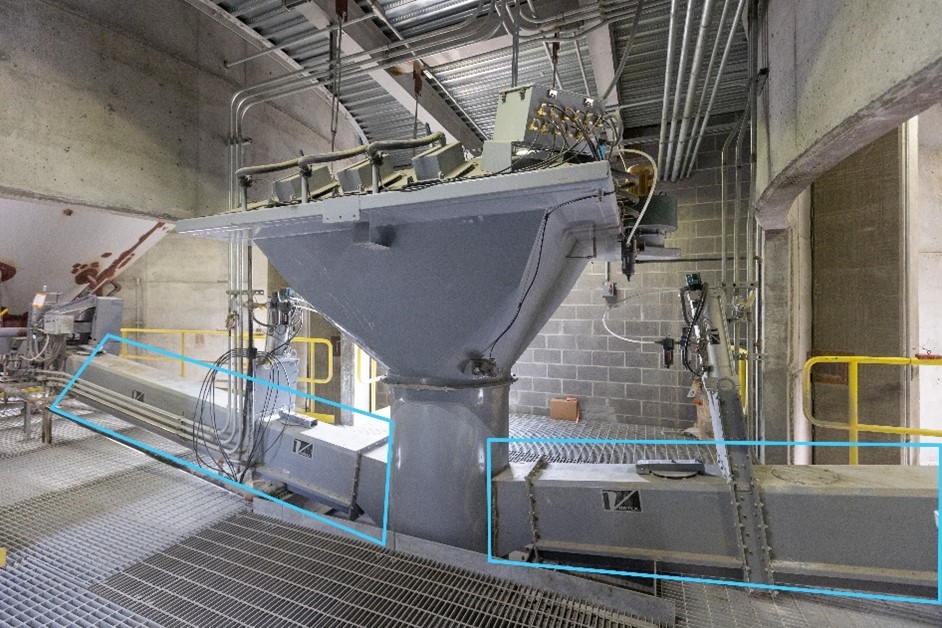
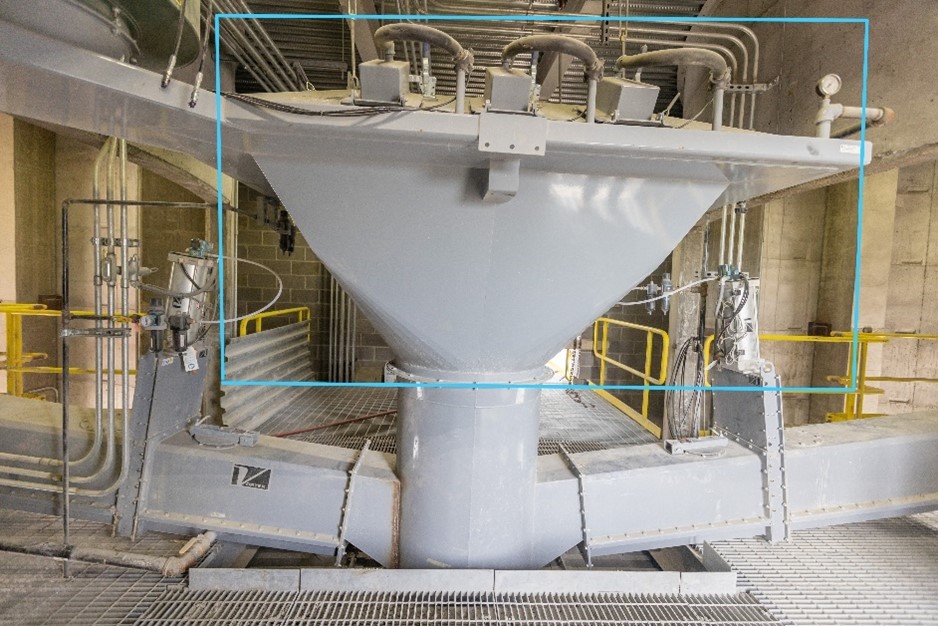
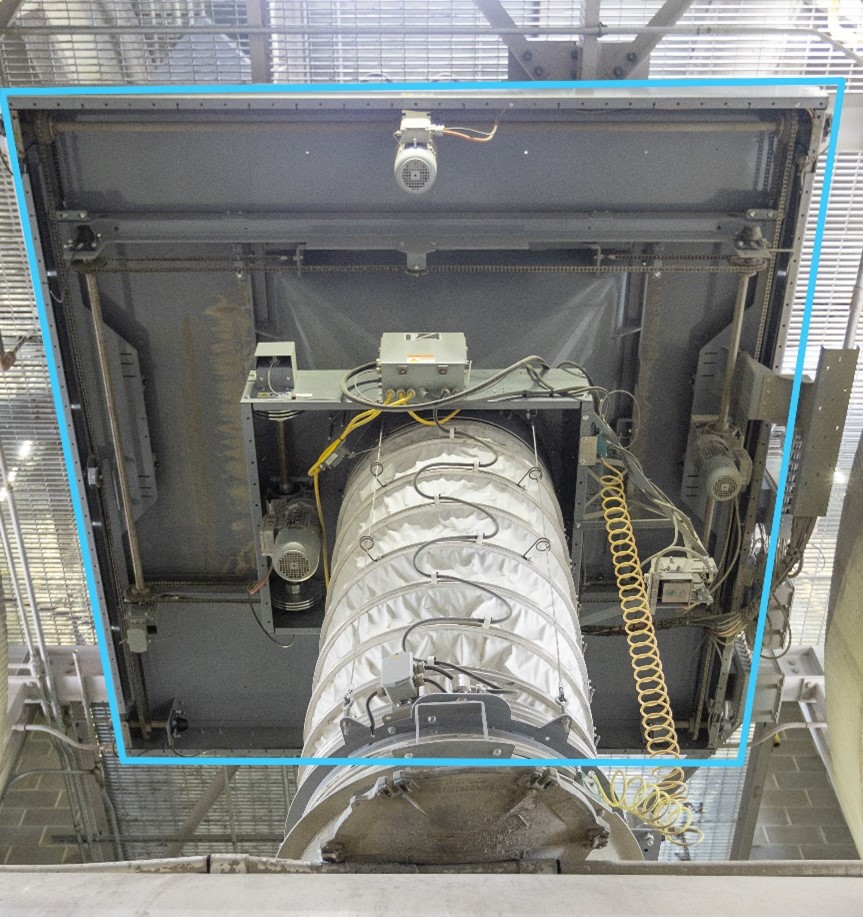
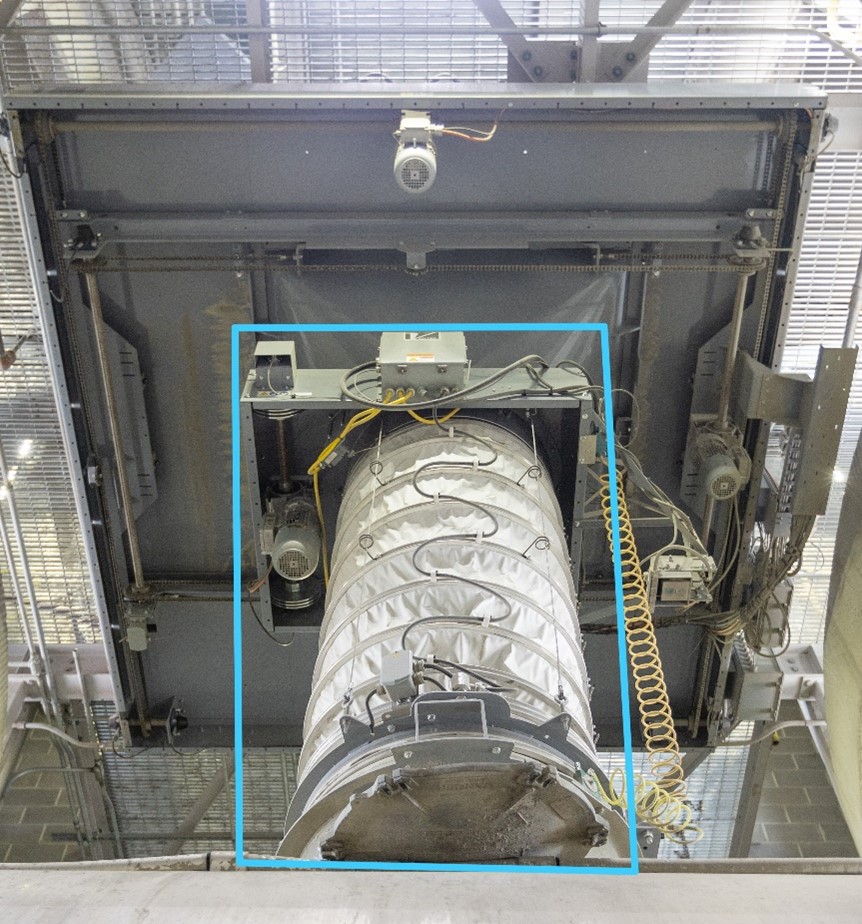
Results
With the implementation of an automated loading system this customer has been experiencing average load times of less than 7 minutes per truck. These loadout times have provided a new level of efficiency while also creating a safer work environment. This customer has been very satisfied with the benefits that automated loading has brought to their process.