
Client:
Quantity:
Size:
Application:
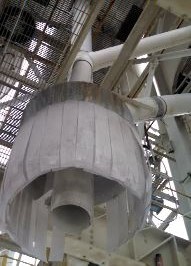
Application
A talc supplier was experiencing issues with their truck loadout station. In their process, talc was discharged from a storage bin into chutework. At the end of the chute, a loading sock was used to load talc into enclosed trucks below. A skirt encompassed the loading sock, in an attempt to limit dust emissions at the point of loading.
Complications of this process included:
- Trucks were constantly being repositioned, in order for the sock to be properly placed inside the loading hatch.
- Talc would suspend upon entering the containerized truck.
- Because the loading sock did not have automated engineering controls, trucks were often over- or underfilled.
- Talc would often bridge in the storage bin above, creating flow issues.
Collectively, these issues created long load times and product loss, which was a profitability concern.
Solution
In 2016, the talc supplier consulted Vortex to discuss their loadout issues. The application engineers at Vortex had several ideas to improve their loading efficiency. The ideal solution was determined to be a Vortex Aero Bin-Bottom; a Vortex Aero-Slide Conveyor, a Vortex Aero-Slide Gate Valve and a Vortex Aero-Slide Drum Valve; a Vortex Maintenance Gate; a Vortex Clear Action Gate; a Vortex In-Line Filtration System, a Vortex Single-Axis Spout Positioning System and a Vortex Loading Spout.
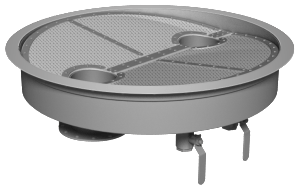
Vortex Aero Bin-Bottom at the Storage Bin Discharge
The Vortex Aero Bin-Bottom aerates talc as it exits the storage bin, to prevent bridging.
Specifications:
- Diameter: 18 in | 455 mm
- Aeration connection & manual balance valve: 2 in | 50 mm
- Angle of decline: 8° from horizontal
- Includes (1) bottom outlet & (1) side discharge outlet.
- Constructed from A36 mild steel.
- Porous media constructed from ¼ in | 7 mm (thickness) 100% needled polyester. Media is supported by a steel grate.
Vortex Aero-Slide Conveyor for Air-Gravity Conveyance & Vortex Aero-Slide Gate Valve for Maintenance
In the client’s previous process, talc could pack and create line plugs in the chutework as it conveyed toward the loadout station. To resolve this issue, a Vortex Aero-Slide is used to convey talc from the storage bin to the loadout station. Because air-gravity conveying is gravity flow conveyance in the presence of slight aeration, it is among the most cost-effective options for conveying lightweight, fluidizable dry bulk powders.
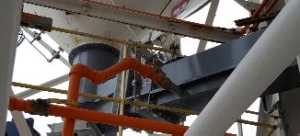
Specifications:
- Length: 8 ¼ ft | 2.5 m
- Inlet & outlet flanges: 10 in | 255 mm (round). Constructed from ¼ in | 7 mm (thickness) A36 mild steel.
- Top inspection hatch & bottom clean-out hatch: 6 in | 150 mm (round)
- Aeration connection & manual balance valve: 2 in | 50 mm
- Angle of decline: 8° from horizontal
- Conveyor constructed from A36 mild steel.
- Porous media constructed from ¼ in | 7 mm (thickness) 100% needled polyester. Media is supported by a steel grate.
A Vortex Aero-Slide Gate Valveis installed between sections of the Vortex Aero-Slide Conveyor. For this application, the Aero-Slide Gate Valve is being used as a maintenance gate and is open the majority of the time; only closed in the case of an upset condition or if maintenance of downstream equipment is required.
Specifications:
- Gate size: 10 in | 255 mm (square)
- Plenum to match Aero-Slide Conveyor’s aeration chamber.
- Hand crank actuator.
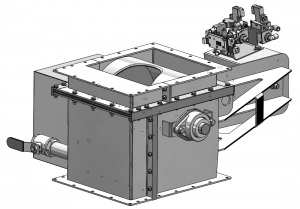
Vortex Aero-Slide Drum Valve for Metering
Also installed between sections of the Aero-Slide Conveyor, on the outlet side of the Aero-Slide Gate Valve is a Vortex Aero-Slide Drum Valve. The Aero-Slide Drum Valve is used to meter flow of talc through the Aero-Slide Conveyor, so not to flood downstream equipment.
Specifications:
- Valve size: 10 in | 255 mm
- Double-acting pneumatic air cylinder actuator.
- Equipped with a Vortex Infinite Variable Positioning (IVP) Assembly, to allow total metering control at +/- 2% accuracy on both the opening and closing strokes.
Vortex Maintenance Gate for Maintenance
At the end of the Aero-Slide Conveyor run is a Vortex Maintenance Gate. It is open the majority of the time; only closed in the case of an upset condition or if maintenance of downstream equipment is required.
Specifications:
- Gate size: 10 in | 255 mm
- Top bonnet cover constructed from metal, and is sealed and gasketed for weather resistance in this outdoor installation.
- Body constructed from 6061-T6 aluminum.
- Blade constructed from 304 stainless steel.
- Inlet & outlet flanges constructed from carbon steel.
- Material contact areas constructed from carbon steel & 304 stainless steel.
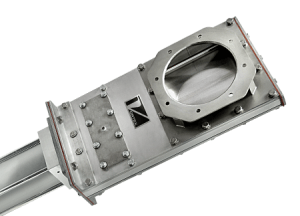
Vortex Clear Action Gate for Material Flow Control
After the Maintenance Gate is a Clear Action Gate, used to control flow as talc is discharged through the loading stackup.
Because talc is a packable, fine material, this Clear Action Gate was equipped with an air purge assembly. An air purge assembly provides differential pressure in the gate’s bonnet area, in order to prevent talc from migrating and accumulating in the gate body. Otherwise, actuation issues may occur.
Also because of talc’s material characteristics, this Clear Action Gate was equipped with a Special Service Inlet. A Special Service Inlet acts as a funnel to direct material flow through the center of the gate. The purpose of a Special Service Inlet is to create a slight void between the sliding blade, the hard polymer seals, and the material flow stream. This allows materials remaining at the blade’s leading edge to fall away into the process line below, prior to entering the end seal. This hinders material packing into the end seal, which could otherwise prevent the gate from fully closing.
Specifications:
- Gate size: 10 in | 255 mm
- Equipped with a Vortex Infinite Variable Positioning (IVP) Assembly, to allow total metering control at +/- 2% accuracy on both the opening and closing strokes.
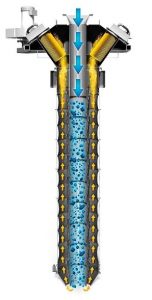
Vortex In-Line Filtration System for Controlling Dust Emissions at the Point of Loading
The Vortex In-Line Filtration System is specifically designed to (1) displace dust-laden air from its source; (2) separate dusts from the air; (3) exhaust the cleaned air to atmosphere; and (4) re-entrain the filtered dusts back down into the load. The Vortex In-Line Filtration System is an “active unit,” meaning an air withdrawal forcibly pulls displaced air and dusts through the filter cartridges to initiate the filtration process.
Once the loading process begins, the attached blower draws up fugitive dusts as they are generated by the material flow stream. Once arriving at the In-Line Filtration System, the fugitive dusts are captured in a series of pleated polyester filter cartridges. Throughout the loading process, automatic reverse pulse jets introduce compressed air to purge the captured dusts back into the load.
Thus, the In-Line Filtration System is designed to minimize product loss and prevent dusting to atmosphere.
Specifications:
- Load rate capacity: 25 ftᶾ/sec | 0.7 mᶾ/sec
- Drive motor voltage: 230/460 VAC/3HP/60Hz
- Accessory voltage: 24VDC
Vortex Single-Axis Spout Positioning System for Load Time Efficiency
The Vortex Single-Axis Spout Positioning System is designed so that talc is discharged through a fixed inlet. Below, a traversing hopper slides across a fixed support pan. A loading spout is attached below the traversing hopper to allow exact positioning of the spout above the truck waiting below.
This Vortex Single-Axis Spout Positioning System was configured for side-to-side movement above a truck.
Specifications:
- Travel: 1 ft | 0.3 m in either direction
- Traversing hopper – angle of decline: 50° from horizontal
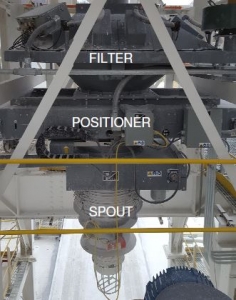
Vortex Loading Spout with Engineering Controls for Loadout Automation
The Vortex Loading Spout features a stacking, cone-in-cone design with an outer sleeve that contains fugitive dusts. Once the spout is lowered, its outlet scavenger “seats” into the truck’s loading hatch. As talc fills into the truck, the Vortex Loading Spout creates an enclosed pathway to prevent dusting into the atmosphere.
To resolve the client’s previous issue of over- or underfilling trucks, this Vortex Loading Spout was equipped with a vibratory probe material level sensing device and an auto-raise kit. Vibratory probes are primarily used when handling lightweight dry solid materials, such as talc. Throughout the loading process, a vibratory probe gives off a consistent vibration frequency. When contacted by the material pile, the probe’s vibration frequency is altered. This triggers an auto-command to the Clear Action Gate above to close/shut-off material flow, which then triggers an automated spout retraction process.
This Vortex Loading Spout was also equipped with a manual material sampling unit, which allows a small sample to be manually extracted as talc passes through the spout’s outlet scavenger. This provides a final test of product quality at the point of loading.
Specifications:
- Vertical travel distance/length: 25 ft | 7.6 m
- Load rate capacity: 250 ftᶾ/min | 7 mᶾ/min
- Outlet scavenger size: 14 in | 355 mm
- Drive motor voltage: 230/460 VAC/3HP/60Hz
- Accessory voltage: 24VDC
- Stacking cones & other material contact areas constructed from 304 stainless steel.
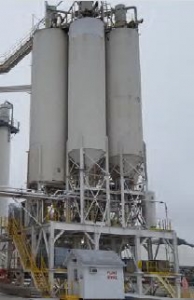
Results
This new loading system has significantly reduced loading times and product loss, and has made an immediate impact on profitability and efficiency.
Uses of Talc
Talc is used worldwide across various industries, including adhesives, agronomy, appliances, automotive, building materials, ceramics, coatings, cosmetics, food, paints, paper, pharmaceuticals, plastics and polymers, putties, recycling, and rubber, among many other applications.