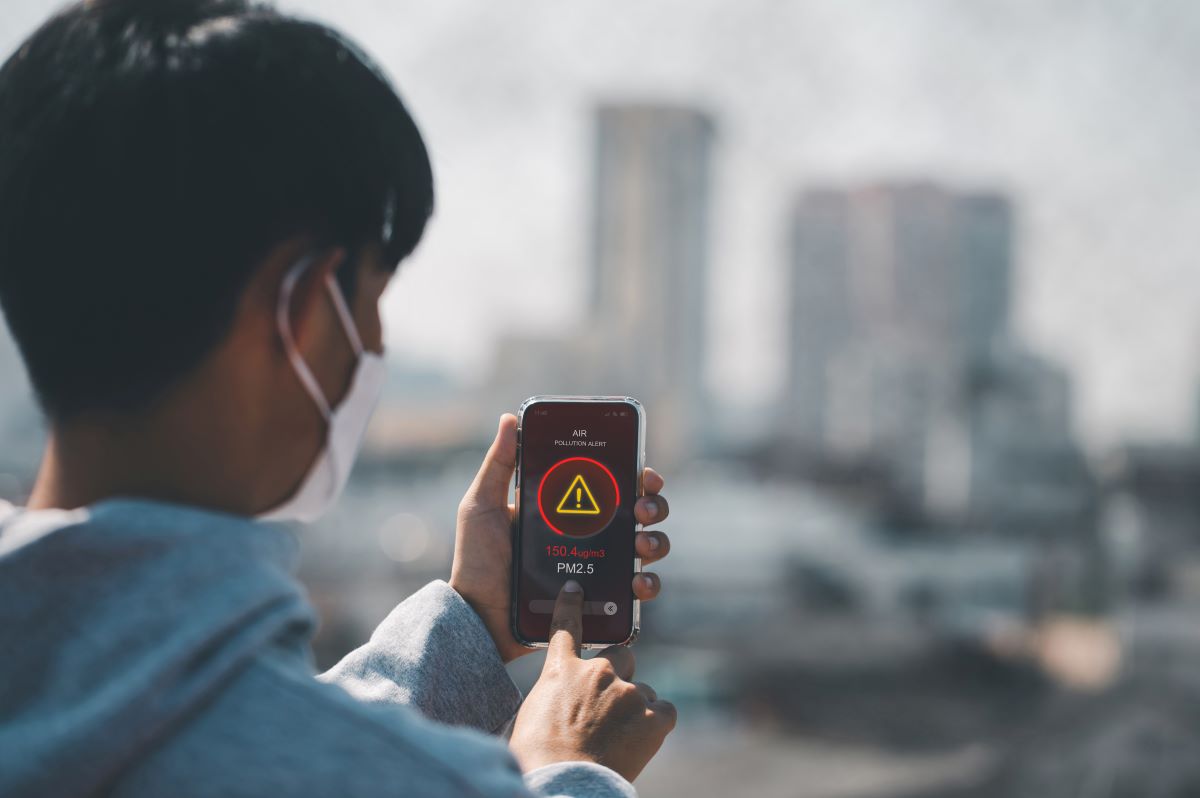
Client:
Quantity:
Size:
Application:
As published in World Fertilizer Magazine:
Fertilizers are vital to modern agriculture, enhancing plant growth and improving crop yields. However, handling and storing these materials can generate dust particles with significant risks to human health and the environment. This article will delve into the different types of fertilizers, their potential hazards, and how having proper material handling components can help reduce exposure to fertilizer dust.
Types of fertilizers and dust generation
There are three primary categories of fertilizers: organic, synthetic, and bio-fertilizers. Organic fertilizers originate from natural sources like animal manure, compost, or plant matter. Synthetic fertilizers are chemically manufactured compounds supplying specific nutrients such as nitrogen, phosphorus, and potassium. Bio-fertilizers consist of living microorganisms that enhance nutrient availability in the soil.
Fertilizer dust generation occurs during production, transportation, and application, with factors like abrasion, mechanical handling, and air displacement contributing to dust particle formation.
The loading of fertilizers can also generate dust particles, especially when it is done in bulk. During the loading process, friction can be created between fertilizer and the wall of the container or between different components of the fertilizer itself. Additionally, if the material is being loaded with a scoop or shovel, this can cause additional abrasion and air displacement — both of which contribute to dust particle formation. Other factors that can lead to dust generation during loading include excessive vibration from conveyor belts and mechanical handling devices like hoppers and augers. Furthermore, any sudden changes in temperature or humidity during the loading operation can trigger condensation, which can create airborne dust particles.
To reduce exposure to fertilizer dust during loading operations, dry bulk storage equipment should be used whenever possible. These systems are designed to optimise airflow and contain any loose materials that could disperse into the environment. Keeping surfaces clean and free of buildup will help minimise abrasion and dust production.
Proper maintenance for mechanical handling equipment is also essential as worn parts or loose connections are common sources of dust escape.
Human health impacts
Human health impacts of fertilizer dust emissions can be far-reaching and devastating. Inhalation of airborne particles can cause damage to the lungs, leading to serious respiratory illnesses such as asthma, bronchitis, and chronic obstructive pulmonary disease (COPD). Prolonged exposure can also damage the heart and circulatory system, increasing the risk of developing cardiovascular problems such as heart attacks and strokes. Exposure to certain types of synthetic fertilizers may even lead to cancer, as some contain toxic substances which are classified as carcinogens.
In addition to direct inhalation risks, fertilizer dust can also have indirect effects on human health. For example, when it is deposited onto crops or in watersheds, this dust can contaminate food and water supplies with toxins that can cause further health issues. Airborne deposits of soil containing fertilizer residues often lead to increased air pollution levels in nearby areas. This air pollution can exacerbate existing respiratory conditions or trigger new ones in people who live close to sources of fertilizer dust.
It is therefore essential that we take steps to reduce our exposure to fertilizer dust emissions. Proper manufacturing components are one solution which has been proven effective for limiting the impact of these hazardous particulates in the manufacturing and loading aspects of fertilizer production. By using technologies like dust tight slide gates, diverters, and loading spouts along with inline or remote filtration devices, these manufacturing components not only help protect us from immediate effects but also from long-term consequences that could arise from sustained exposure.
Environmental consequences
Fertilizer dust also poses threats to the environment. Soil degradation can occur when excessive dust accumulates on the ground, altering the soil's physical and chemical properties. Dust particles can be transported by wind or water, leading to water pollution and harm to aquatic life. Wildlife can be affected if they consume contaminated food sources or inhale the dust particles.
In addition to soil degradation, fertilizer dust can have detrimental effects on nearby ecosystems. Wind-borne particles can travel long distances, causing acid rain in areas far away from their source. This acidic rain can damage plants and soil structure, leading to the destruction of vegetation and disruption of nutrient cycling. Additionally, nitrogen-rich fertilizers can lead to eutrophication when they enter aquatic environments like rivers or lakes; these waters become overly enriched with nutrients which encourages algae growth and reduces oxygen levels in the water. This lack of oxygen is toxic for fish and other aquatic organisms, leading to massive die-offs which can devastate entire populations.
The impact of fertilizer dust on air quality is equally concerning. These particulates contribute to ground level ozone formation, a major component of smog which is known to cause a range of health problems including respiratory illnesses, eye irritation, and other adverse effects on lung tissue. Fertilizer dust also contributes significantly to climate change as it contains high levels of black carbon; this carbon absorbs heat from the sun and raises temperatures in the atmosphere as well as in bodies of water.
Ultimately these environmental impacts are not only damaging for animals and ecosystems but also for human beings that rely upon them for resources or recreation. It is therefore essential that we take steps to minimise our exposure to fertilizer dust emissions, both through appropriate safety measures such as wearing face masks or respirators while handling materials and by using proper dry bulk components which help contain and divert hazardous particulates away from workers before they reach breathing zones.
Dry bulk equipment: Reducing exposure to fertilizer dust
Vortex dry bulk equipment offers innovative solutions for minimising the risks associated with fertilizer dust. Key products and their benefits include:
- These filtration systems: actively displace dust-laden air from the source, separates dust particles from the air, exhausts the cleaned air into the atmosphere, and re-entrain the filtered dust back into the load. This process not only reduces waste but also improves profitability by loading out the dust as product. The in-line filtration system of the Vortex loading spout further enhances dust control by continuously purging dust from the filters, thereby increasing their service life and reducing the risk of clogs or overflow. This self- contained system eliminates the need for a central dust collection system, streamlining operations and reducing potential hazards in the workplace.
- Loading spouts: Designed for precise material loading, these spouts effectively contain dust emissions with overlapping rubber strips that act as a dust skirt and an outer sleeve. When combined with dust collection (in-line or remote) these design features drastically reduce dusting during load out to near zero levels.
- Dust control skirt: This optional detachable feature allows the Vortex loading spout to easily switch between open and enclosed loading applications, eliminating the need for multiple spouts.
- Self-sealing discharge: The cone-in-cone design provides a self-sealing discharge that minimises material spillage and dust emissions. This device is designed for use on trucks and rail cars with compatible hatches. The discharge extends into the hatch while filling and the closes once the spout is retracted from the hatch.
- Dust-tight slide gates: The implementation of dust-tight slide gates is an essential aspect of maintaining a safe and efficient fertilizer production facility. These specialised gates are designed to secure the flow of dry bulk materials, such as raw ingredients and processed fertilizer products, while preventing the escape of dust particles into the surrounding environment. The various types of slide gates that can be employed in a fertilizer plant include manual or automatic gates, roller or knife gates, and specialised gates engineered for unique applications. The selection of a dust-tight slide gate is crucial, as it ensures optimal sealing and material containment, contributing to a cleaner and more controlled production process.
- Dust-tight diverters: Diverter valves play a crucial role in the effective control and management of fertilizer dust emissions, ensuring both product quality and safety in various industrial processes. Designed to provide a reliable solution for handling dry bulk materials, these specialised valves are engineered to facilitate seamless material flow while preventing dust leakage during transfer processes. Implementing Vortex dry bulk equipment in fertilizer handling facilities can lead to reduced health hazards, cost savings from minimised product loss, and improved operational efficiency.
Conclusion
Fertilizer dust presents significant hazards to human health and the environment. Understanding the different types of fertilizers and their potential risks is crucial in addressing these challenges. By incorporating dry bulk equipment into handling processes, facilities can effectively mitigate fertilizer dust exposure, ensuring a safer and more sustainable future for agriculture.