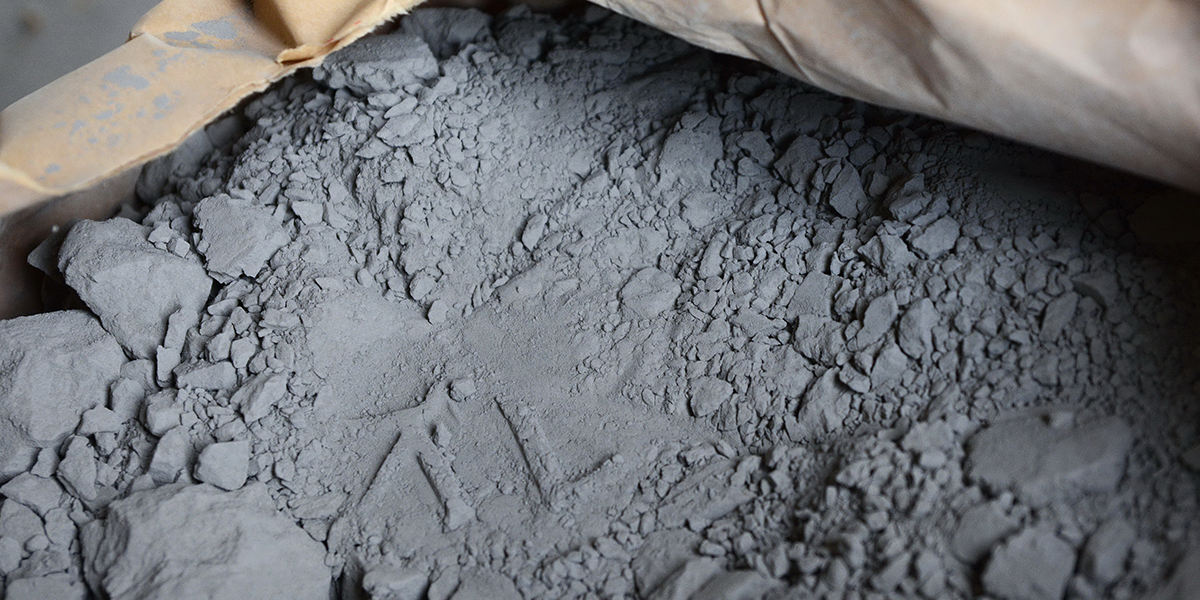
Client:
Quantity:
Size:
Application:
As published in Dry Cargo International
By Austin Anderson
Loading of cement can be a complex endeavor. From environmental and safety concerns to efficiency, many factors are taken into consideration by cement plants when developing a loadout process. Vortex Global has identified key wear points, reinforced those areas with abrasion resistant materials, and added features to reduce the time it takes to perform maintenance on various components.
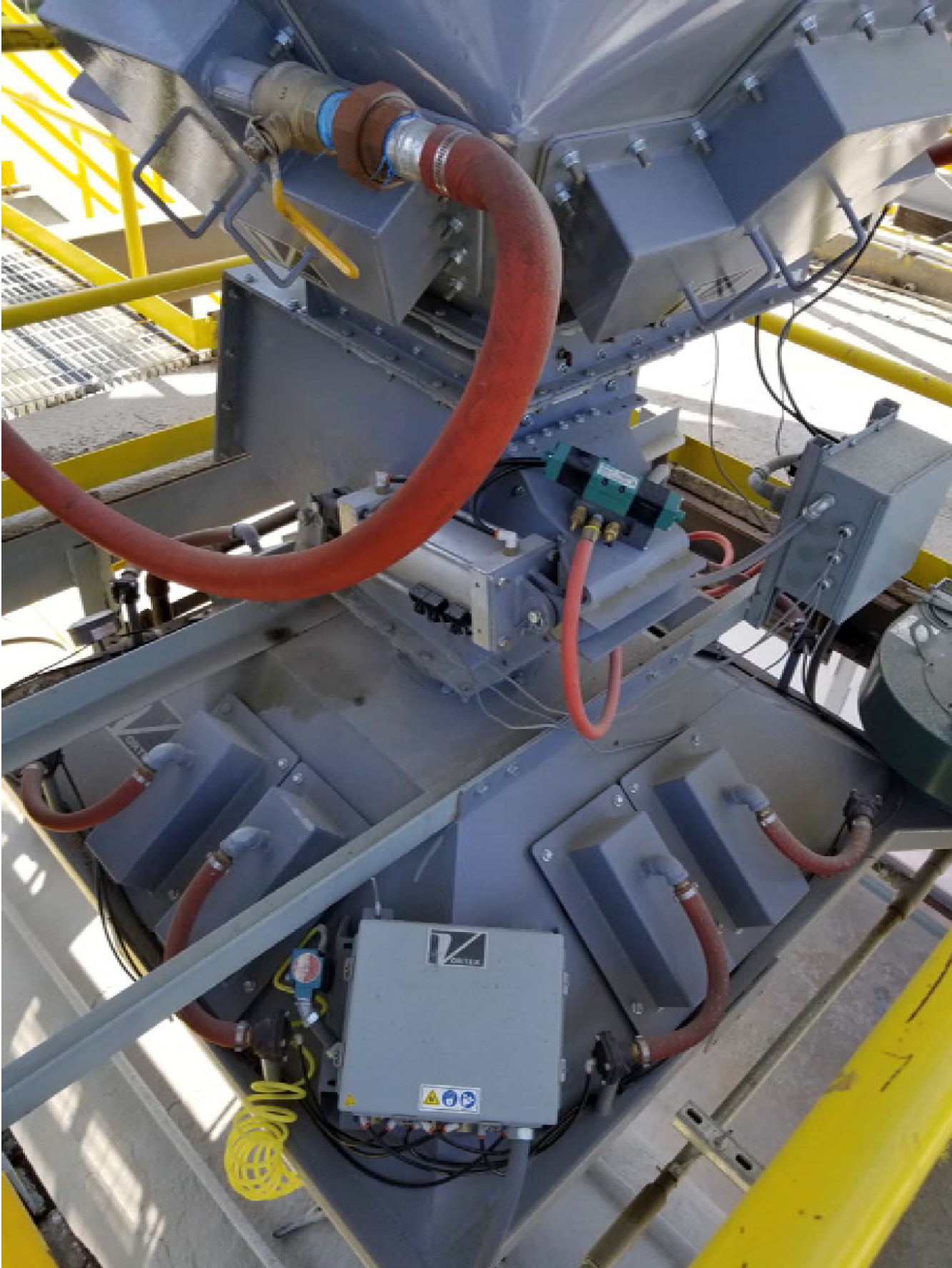
Loading Systems Provide Solution for Cement Handling
Loading spouts provide facilities with fast and steady material flow during the loading of dry bulk solid materials in open or enclosed vessels such as trucks, railcars, ships, and barges. Cement plants across the globe use loading spouts in their systems. Designed to capture fugitive dust, prevent material waste, and ensure plant and environmental safety — Vortex Loading Spouts require minimal maintenance and service expenses. When loading trucks and railcars with dry bulk solid materials, including cement, the speed of load out is a key concern. For optimal performance, loading spouts can be used in tandem with accessories specifically designed to accelerate the loading process.
Capturing Dust with Filtration Systems
In applications where dusting is a concern, the addition of an in-line filtration system can prevent dust from escaping to the atmosphere which addresses not only safety concerns but maximizes profits by eliminating the loss of product. The Vortex In-Line Filtration system is located at the material feed inlet to collect fugitive dusts by means of air withdrawal. Fugitive dusts are captured in pleated polyester filter cartridges. Throughout the loading process, automatic reverse pulse jets inject compressed air to purge the captured dusts back into the load. In enclosed loading applications, the addition of a self-sealing discharge seals off the outlet scavenger to prevent dusting to atmosphere between loading cycles.
Advantages of Aerated Bin Bottoms
The addition of an aerated bin bottom provides many advantages to a cement handling process. These products are utilized to move lighter weight material that is capable of being fluidized. During the process of fluidization, air is passed through static, dry material, causing the material to acquire fluid-like characteristics. The dry, solid material flows better and is easier to handle in its fluid-like state. The aerated bin bottom is located at the bottom of a silo or a hopper and can be especially beneficial on storage silos with especially large diameters. Aeration of the material within the bin eliminates the bridging and ratholing commonly associated with bin storage and allows the material to flow at a much smaller angle of repose.
Implementing Slide Gates into Loadout Process
In some loading applications, slide gates are sourced to assist in various aspects of the loading process. Vortex Global’s slide gates are ideal for controlling the flow of dry bulk material. Designed to extend the service life of the valve and the ability to perform maintenance without taking the valve out of line, Vortex slide gates are commonly used in the chemical, cement, coal, food, grain, minerals, plastics and mining industries. The Vortex Rounded Blade Gate is designed to meet the most demanding applications when handling heavy-duty abrasive materials. The RBG Gate handles dry material in gravity flow applications where positive material shut-off and dust-tight sealing is required. In loading applications, the Rounded Blade Gate can be used to meter the material being handled. Should maintenance or work need to be completed, a slide gate can be used as a maintenance gate. The Vortex Titan Slide Gate can be used in these circumstances to stop material flow while maintenance is completed downstream.
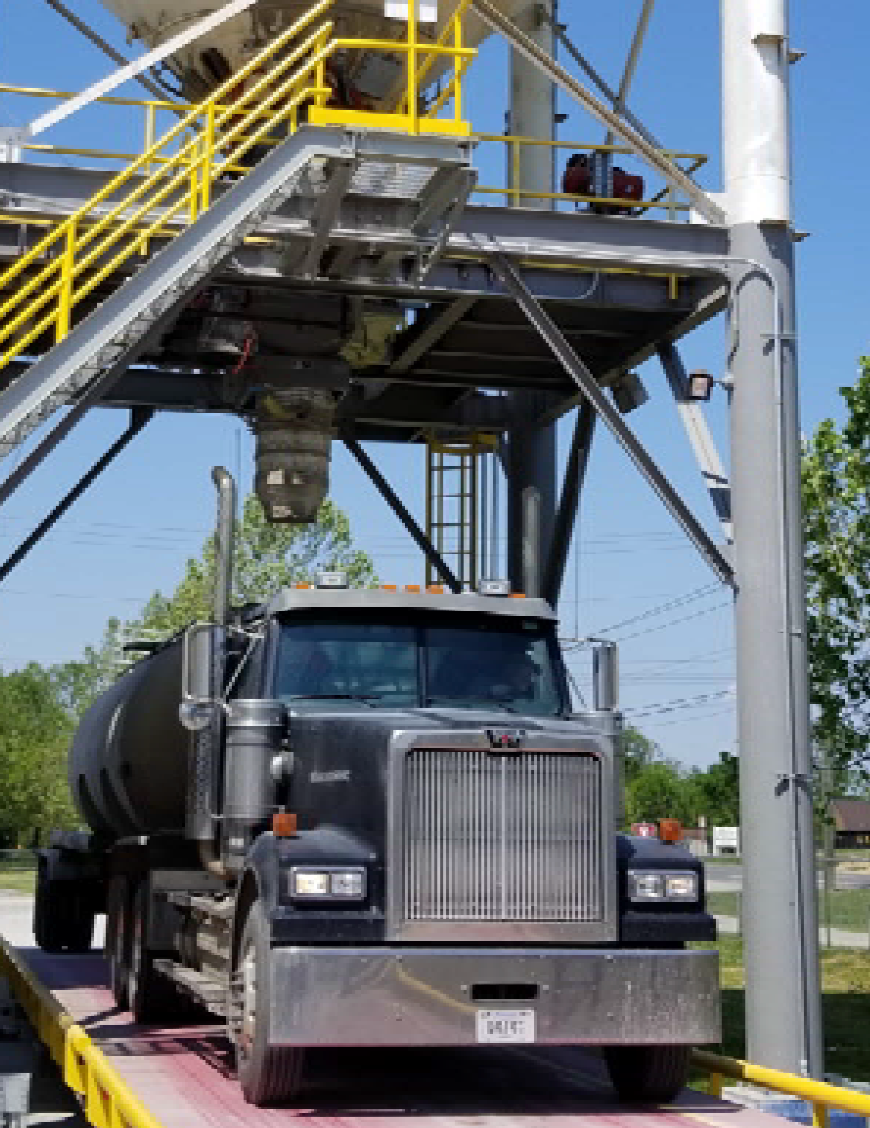
Case Study: Vortex Loading Solutions Assist at Cement Terminal
In this application, a cement terminal utilizes products from Vortex’s line of loading solutions and aerated conveying systems to handle cement.
Features:
This 14” (355mm) loading spout stack up features a Vortex Aerated Bin Bottom, Titan Slide Gate, Rounded Blade Gate, Dust Filter, and Retractable Spout with Self-Sealing Discharge.
Application:
The aerated bin bottom provides a constant material flow, the rounded blade gate offers metering of material, and the Titan slide gate is utilized as a maintenance gate should work on downstream equipment be required. The Dust Filter draws dust away from the loading hatch and then pulses that dust back into the load. The Self-Sealing Discharge closes when the spout is retracted — prohibiting internal dust from escaping to atmosphere. The previous 15-minute truck loading time has been reduced to less than five minutes per truck.