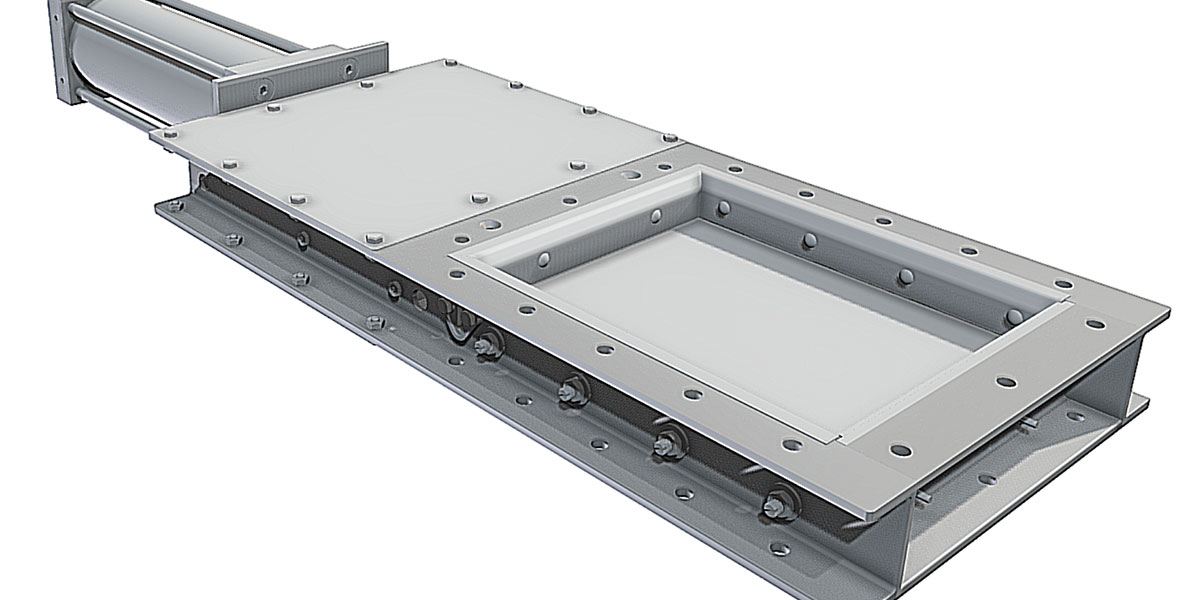
Client:
Quantity:
Size:
Application:
As published in Powder & Bulk Solids
When selecting equipment for the handling of dry bulk solid materials in gravity flow applications, there are several factors that should be taken into consideration. Among these include the particle size of the material being handled and the abrasiveness of the material. Another driving factor is the bore size of the valve required. Several types of slide gates and diverters may be suitable for handling materials in gravity flow applications.
Roller Gate
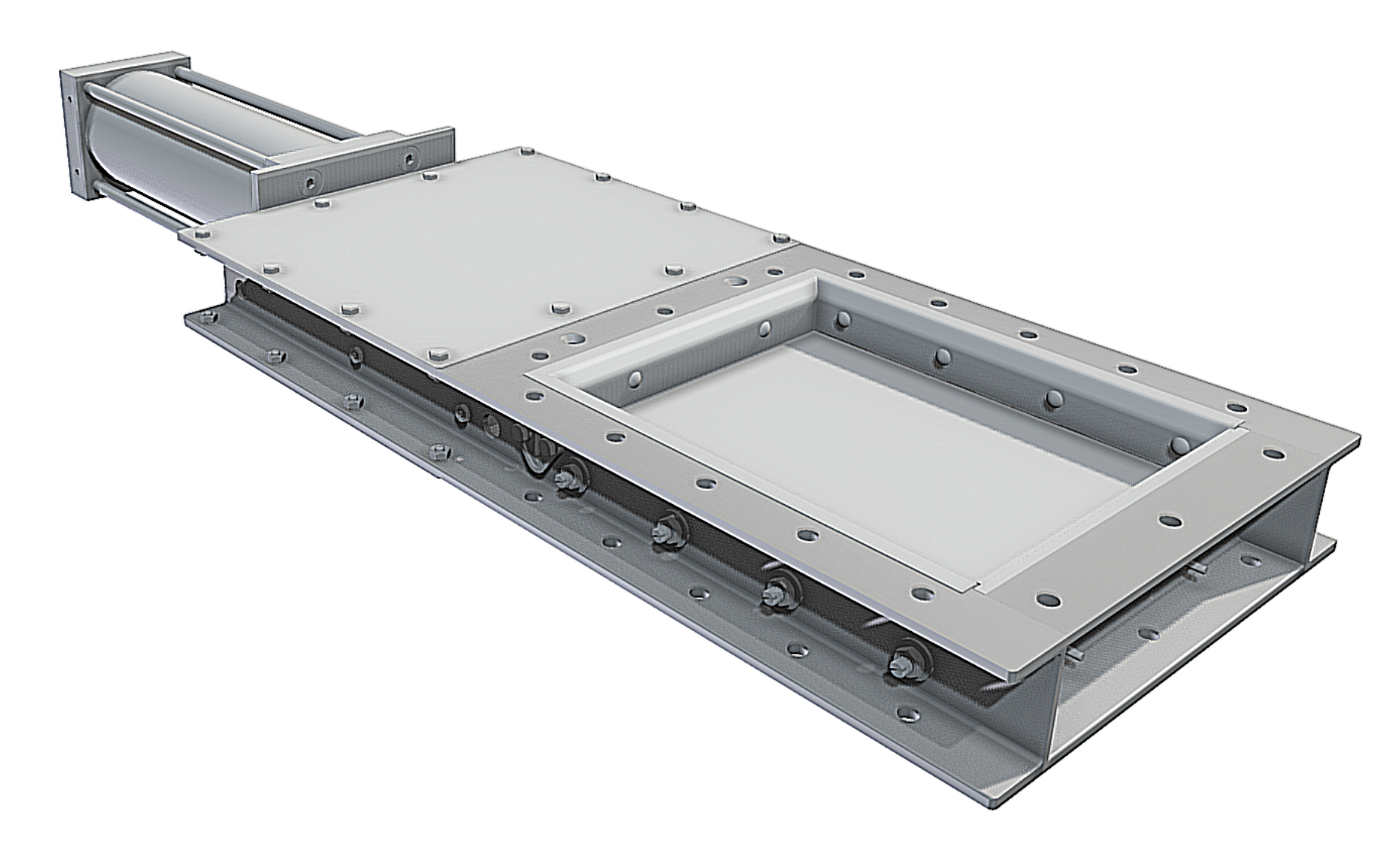
The roller gate is ideal for handling dry bulk material in gravity flow applications where positive material shut off and dust tight sealing are required. Roller gates are commonly used for several dry material applications such as mixing and blending. The Roller gate can be applied to shut off or meter the flow of fine and mildly abrasive powders and small to large granules or pellets. It also handles sticky materials, horizontal or vertical valve orientation, and is ideal for the food, chemical, plastics, and textile industries.
Curved Blade Gate
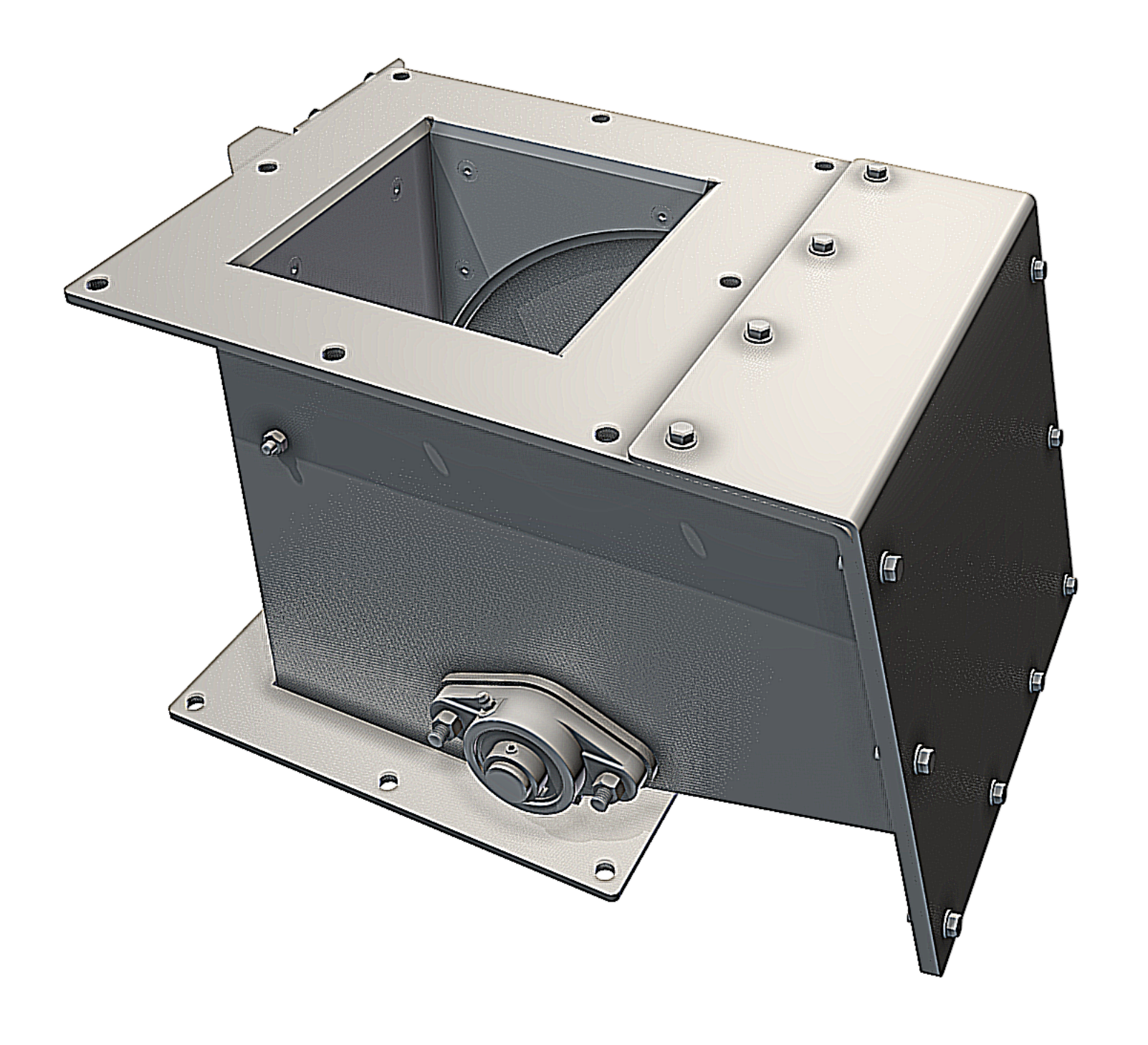
The curved blade gate is an ideal solution for handling abrasive materials and for applications that may require metering. The rapid actuation of the blade controls material flow rates by quickly starting and stopping the flow of material. Designed to handle highly abrasive materials such as minerals, frac sand, fly ash, and whole grains, the curved blade gate handles dry material in gravity flow applications where positive material shutoff and dust-tight sealing are required. The gate can be equipped with a wide variety of actuation choices including pneumatic, electric, and hydraulic.
Abrasion-Resistant Steel Slide Gate
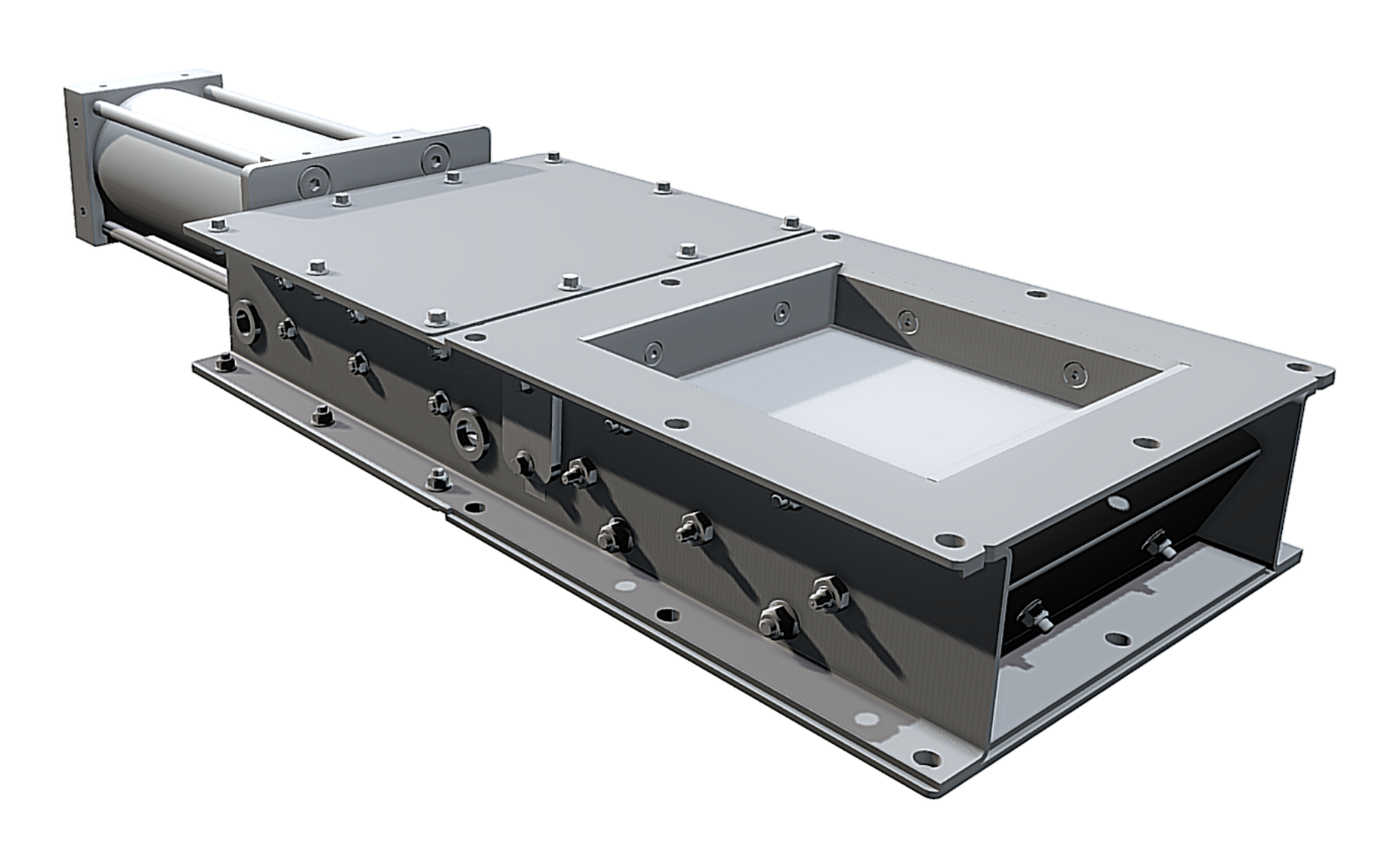
The abrasion-resistant steel slide gate is designed to meet the most demanding applications when handling heavy-duty abrasive materials such as sand, gravel, coal, whole grains, metal powders, or minerals. The gate handles dry material in gravity flow applications where positive material shut-off and dust tight sealing are required.
Available in a wide variety of configurations with rectangular sizes and customer specific hole patterns, the gate has “live loaded” bonnet seals that extend service life by compensating for wear and provide an exceptional material seal across the gate and to atmosphere. These seals can be swapped while the valve is still in-service vastly reducing downtime. To extend the life of the slide gate, the gate has abrasion-resistant liners that can be replaced when needed. The slide gate utilizes easily accessible, hardened steel cam-adjustable rollers, and polymer blade guides – a feature that is critical to maintaining a positive seal.
Flap Diverter
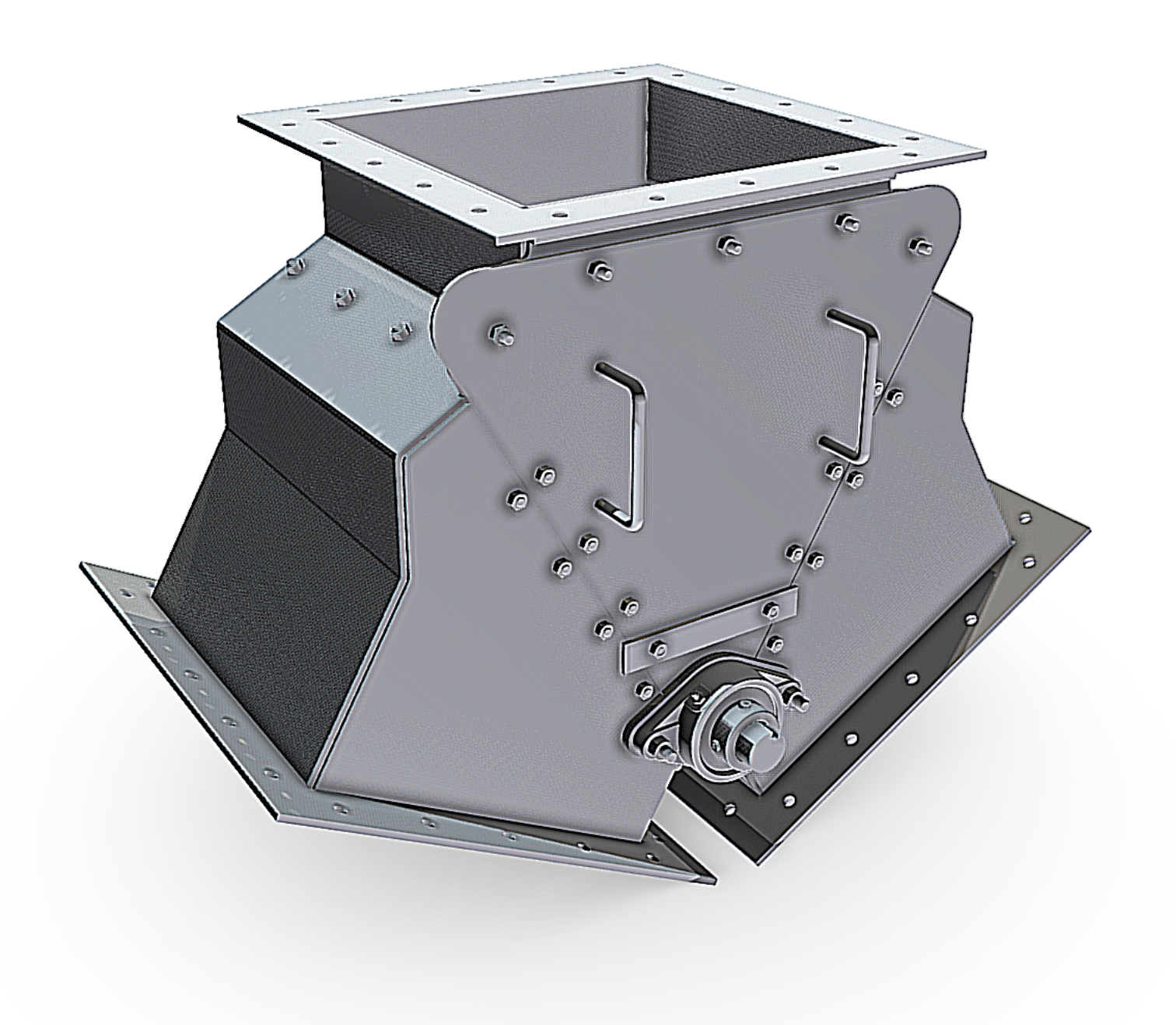
The flap diverter utilizes an interior, angled blade to divert material flow from one source to two, three, or more destinations. This diverter can be used for a variety of nonabrasive to moderately abrasive materials and can handle particle sizes as small as 50-75 microns. It is ideal for use in plastic, food, chemical, and agricultural applications that require a dust-tight seal to minimize cross contamination. Another benefit of the flap diverter is its capability to channel the flow of material away from the leading edge of the flapper vane, maintaining the seal integrity and inhibiting material leakage across the closed legs of the valve.
Dual Slide Gate Diverter
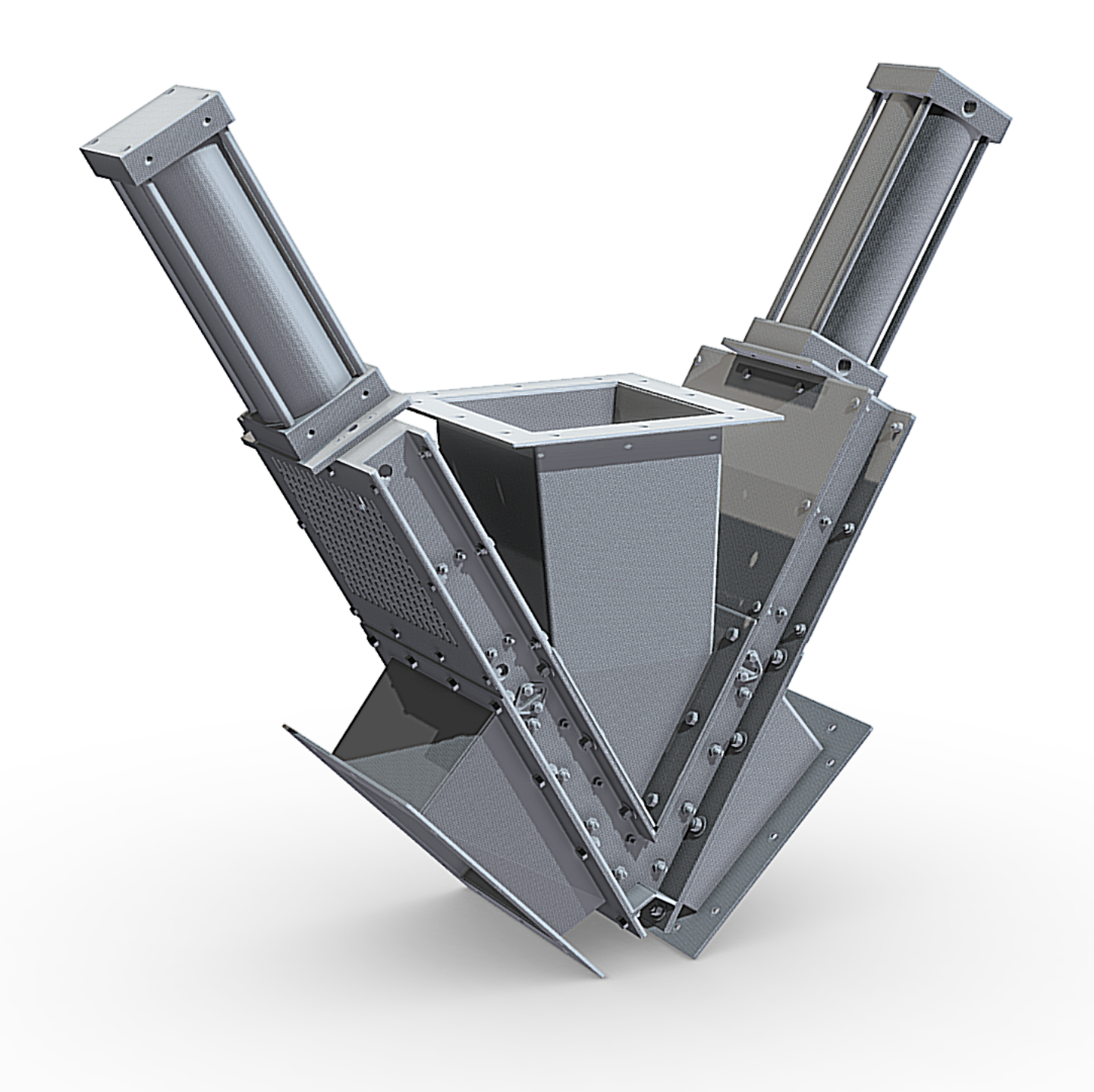
Dual slide gate diverters offer a unique design that provide several advantages traditional flap-type diverters do not. Their design provides more versatility and reduces the need for additional shut off gates. The diverter can divert material in one or two directions and completely stop the flow when necessary. The implementation of positioning controls allows for the control of flow rate through either leg simultaneously. The dual slide gate diverter also offers sealing capabilities and is easily maintained while in service.
Bucket Diverter
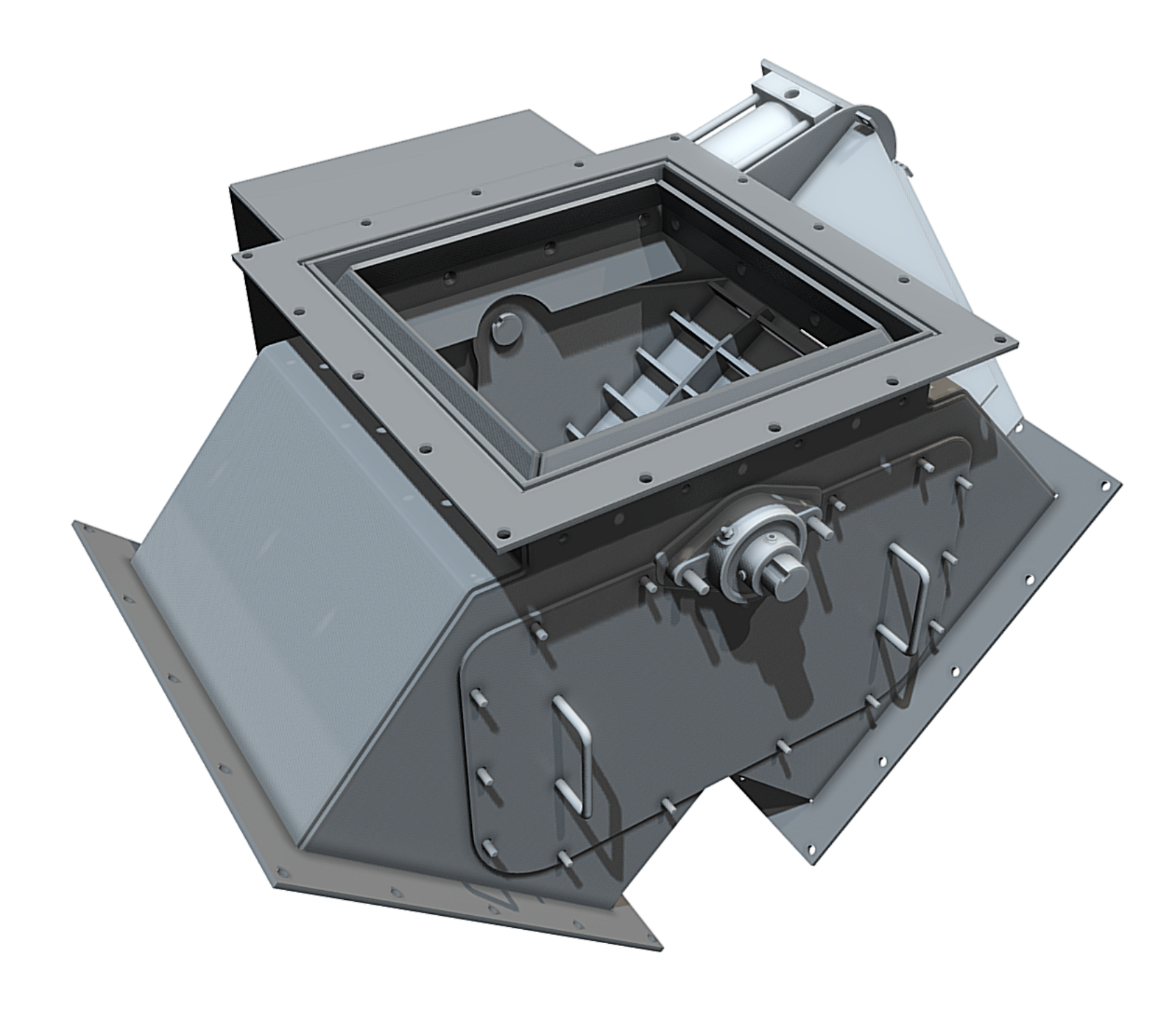
The bucket diverter is used to divert heavy-duty and/or abrasive dry bulk solid materials such as sand, gravel, whole grains, and coal from one source toward two destinations in gravity-fed applications. Optional inlets, chute liners, and bucket liners extend the life of this valve when handling abrasive materials. The diverter’s access panel allows for quicker entry to the interior of the diverter for inspecting and cleaning the valve. The heavy-duty abrasion-resistant bucket is also removable through this access panel for service.
Abrasion-Resistant Steel Lined Flap Diverter
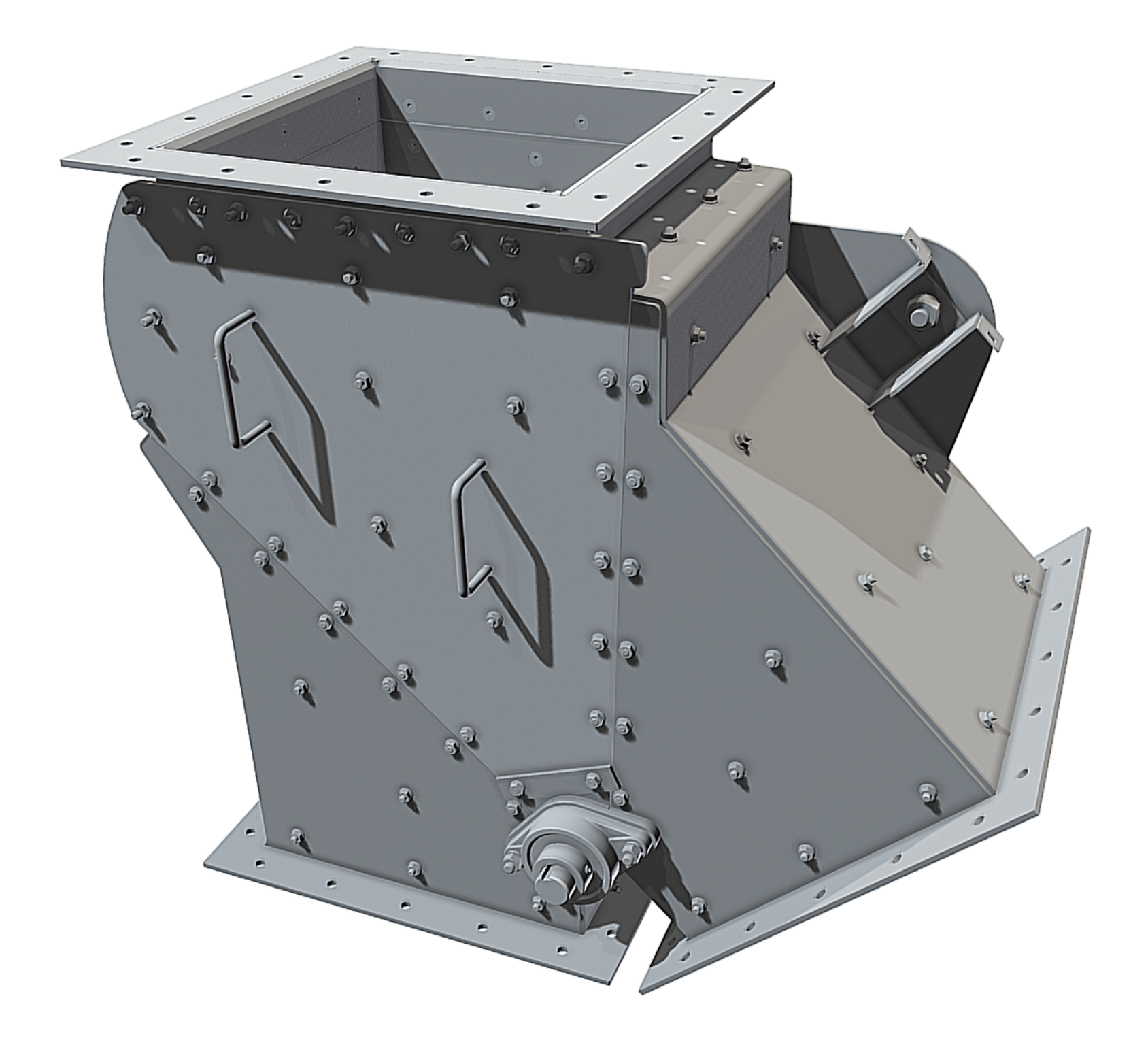
The abrasion-resistant steel lined flap diverter is designed for use in gravity flow applications handling abrasive materials such as coal, rock, or frac sand that require an environment sealed from dust and fine powders. The diverter channels the flow of material away from the leading edge of the flapper vane. This is critical to maintain seal integrity and inhibit material leakage across the closed legs of the valve. Traditional flapper diverters tend to leak past the vane shaft and trap material underneath, causing actuation problems. The diverter incorporates a shaft seal to eliminate these problems. To extend the life of the diverter, this diverter features abrasion-resistant liners that can be replaced when needed prolonging the life of the diverter. The abrasion-resistant steel lined flap diverter also comes standard with removable access panels for inspection, cleaning, and maintenance.
Chute Diverter
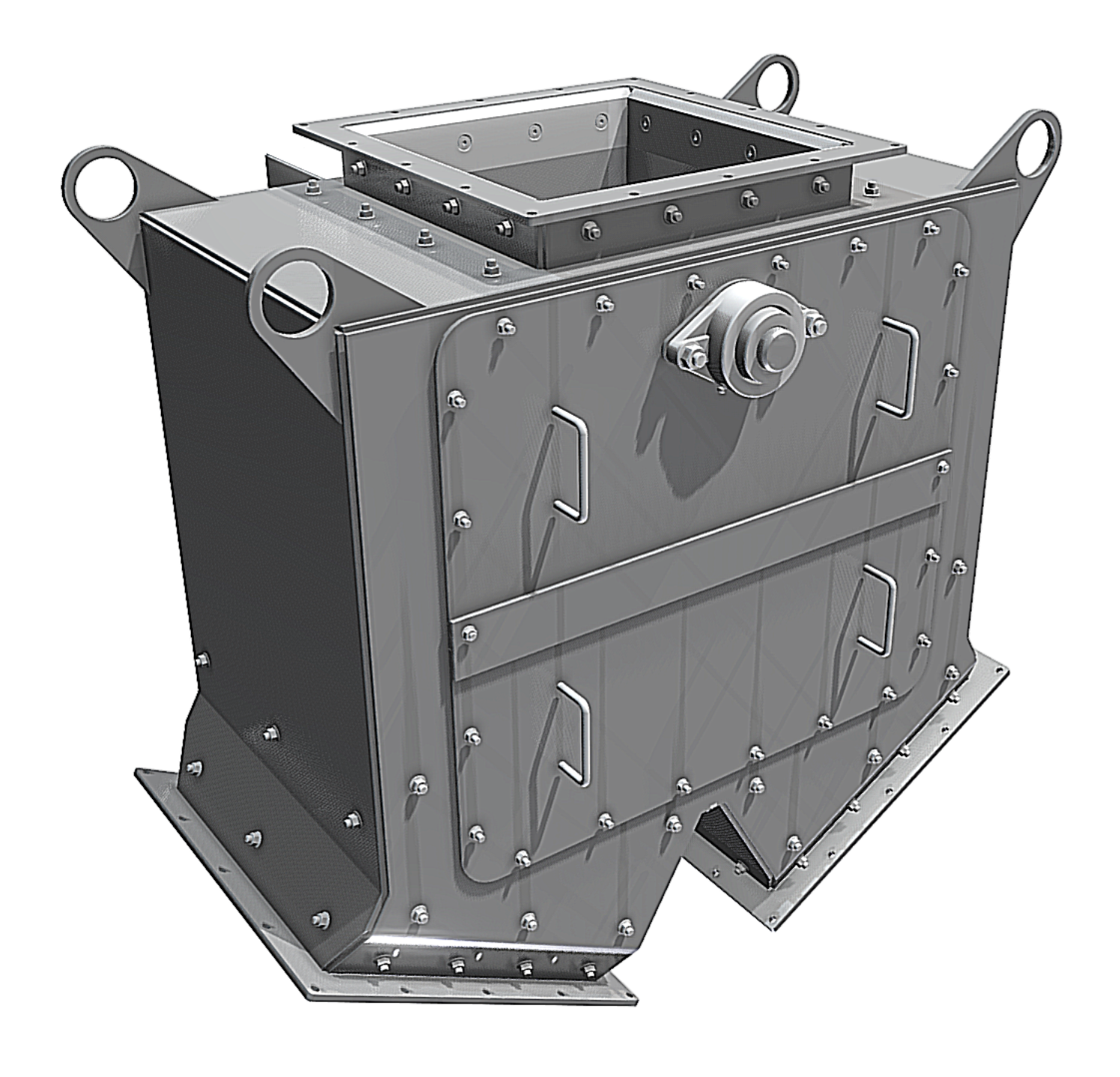
A chute diverter is intended for use with abrasive materials such as industrial sand, limestone, coal, gypsum, clinker, gravel, bauxite, whole grains, and minerals. The body houses an internal chute that pivots to direct material flow. A primary advantage of this diverter is that it features no internal seals to maintain. Material abrasion is addressed in its design and it can be constructed of, or lined with, wear-resistant materials. Inspection, maintenance, or repairs to the diverter may be performed from the front access panel – without removing the diverter from service. This diverter is dust-tight to atmosphere, may be shifted “on-the-fly,” and is available in two-way and three-way configurations. Additionally, the chute may be positioned to split flow to both directions simultaneously.
Conclusion
Sourcing a slide gate or diverter for gravity flow applications can be a complicated process. Each of products above provide excellent solutions for certain gravity flow applications. It is crucial to consult with industry experts when selecting a product for your process. With numerous variables to consider, ensure that your selection is truly the best for your particular application.
Vortex Global has provided slide gates, diverters, iris valves, and loadout equipment For more than 45 years, designed specifically for handling dry bulk solids in gravity, vacuum, dilute, or dense phase applications. Vortex products can be completely customized for individual applications or special installations. For more information, visit www.vortexglobal.com.